Our industry experts work alongside you from idea to prototype to product, providing design support and helping you make informed, validated material selections that meet your needs for unique applications and fit-for-use production technologies.
Our collaborative and problem-solving approach helps our customers both navigate and understand the possibilities in our extensive portfolio of advanced engineering plastics and composites.
The choice of materials can influence everything from manufacturing costs, to component performance and ongoing maintenance. We offer complete end-to-end consultation, providing expert guidance on which materials can overcome the challenges of your application, perform reliably throughout its life, and achieve your engineering goals.
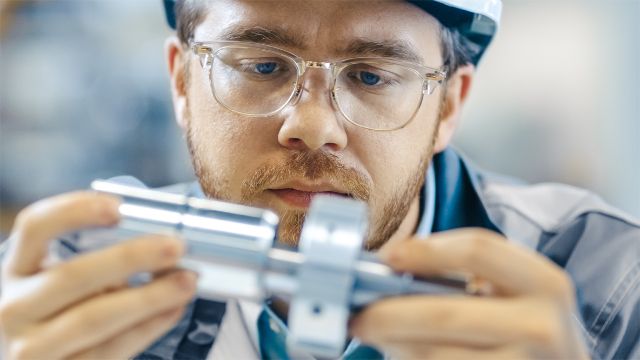
Material replacement
When existing components fall short, our experts can advise on the potential for engineering thermoplastics and composite materials to improve part performance, longevity, and costs. We go beyond just helping you choose a material that will outperform current parts, providing end-to-end consultation, cost and efficiency optimization, superior manufacturing capabilities, and the broadest portfolio of engineering plastics on the market.
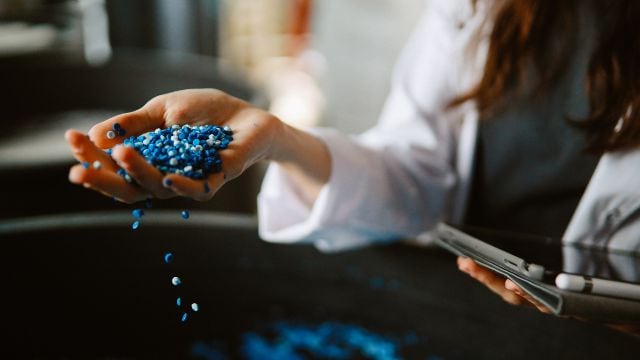
Compliance evaluation
Regardless of the industry and corresponding regulations, our engineering plastics are used in applications subject to rigorous compliance. We routinely work with regulatory bodies and raw material suppliers to ensure we have the most up-to-date compliance and safety data for each of our products, enabling us to present customers with the broadest range of candidate materials.
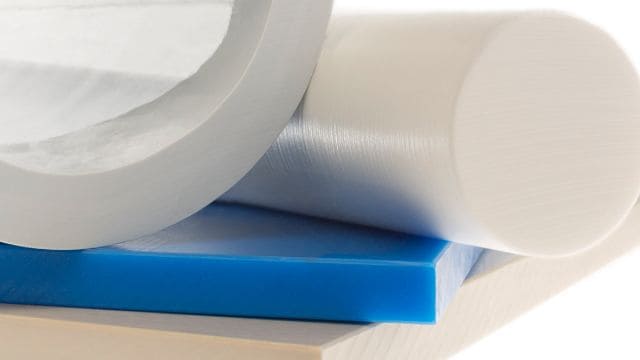
Stock shapes
Encompassing rods, plates, tubes, profiles, liners, and more, our portfolio of thermoplastic stock shapes provides designers with flexible material dimensions and configuration. We also fabricate near net shapes in a variety of processes, allowing you to comprehensively evaluate our full portfolio, reduce material and manufacturing costs, and minimize waste by starting with the most economical shape.
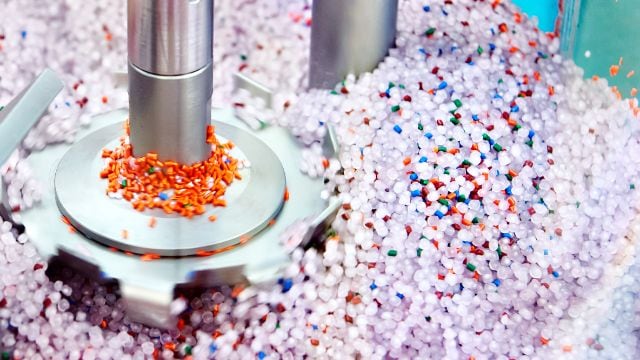
Custom compounding
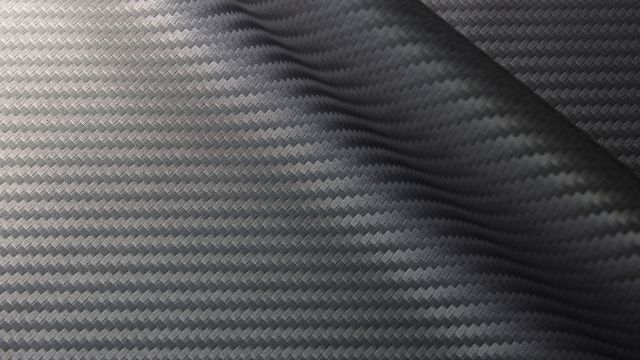
Composites
With unparalleled expertise and a cutting-edge portfolio of composite materials, our experts and products enable lightweight and sustainable solutions across a range of industries and applications. We help replace traditional materials with cost-effective, future-ready composites that enable scalable and market-driving innovations.
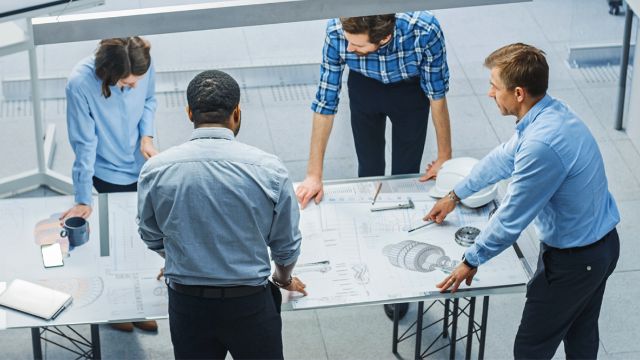
Material evaluation & sampling
From mechanical, physical, and chemical properties to cost-effective shapes and machinability, we detail our materials and products through in-depth technical and characterization data, allowing you to thoroughly evaluate material selections and alternatives and identify the correct material for your application.
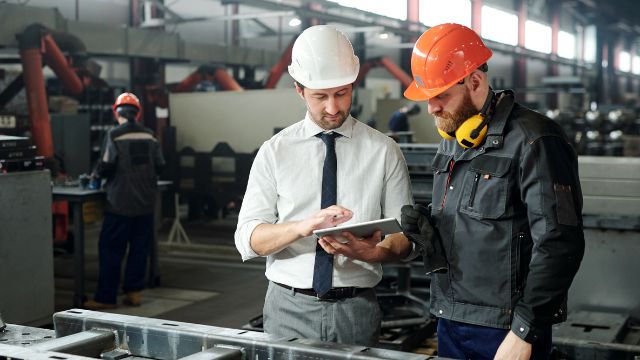
Supply chain support
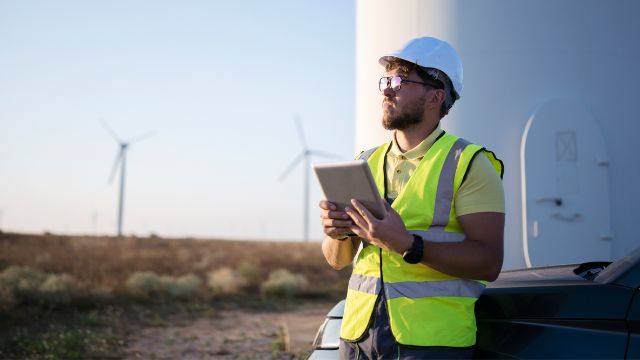
Sustainability & circularity considerations
Our KAITEKI philosophy drives our actions, including reducing carbon emissions and speeding up recycling and circular solutions within the lifecycle of our products. Beyond our own initiatives, we assist our customers in finding materials that can help them achieve their sustainability goals, offering carbon footprint evaluation and Life Cycle Assessment services.
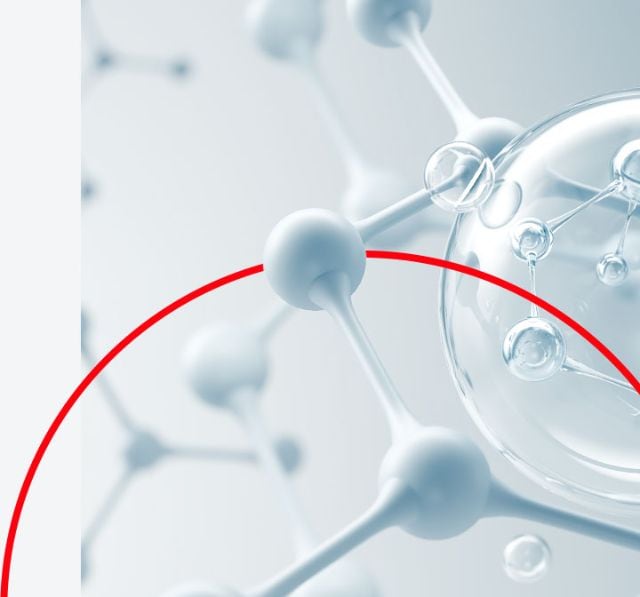
MatFind
Quickly find the optimal engineering plastic for your application. Simply input the performance properties you require, and MatFind will help you filter and compare materials.
Rethink what you know about plastic performance
Advanced material properties
Don’t think it’s possible? Our comprehensive portfolio of advanced engineering plastics covers a wide spectrum of materials with superior performance properties – from long-lasting wear resistance, to chemical compatibility, to dimensional stability.
Speak with one of our material experts to see how our advanced engineering materials can perform to your most ambitious specifications.
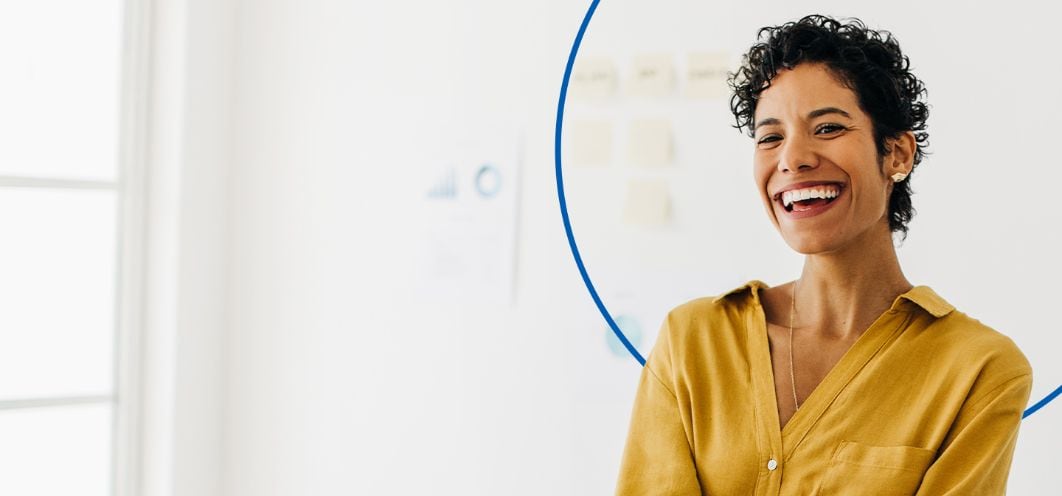
Wear resistance
Our wear-resistant plastics outperform metals in load-bearing and friction applications. Furthermore, they resolve many common engineering issues, such as inhibiting mechanical wear and damage, preventing contamination, reducing noise, and extending the mean time between repair.
Characterized by a low coefficient of friction, high limiting pressure velocity, and low wear rates, our portfolio of wear-resistant thermoplastic materials offer longer-lasting, predictable performance in a wide range of conditions
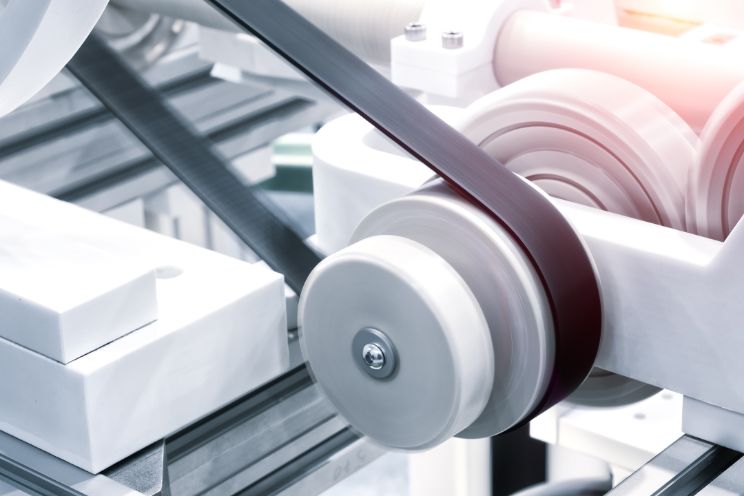
Dimensional stability
Even when exposed to high temperatures, moisture, and mechanical stress, our range of dimensionally stable thermoplastics retain their shape, exhibiting consistent performance and delivering cost savings over metal components.
With a low linear of thermal expansion, low moisture absorption, and high resistance to creep, plastic materials with exceptional dimensional stability can perform on the level of metals. They are also ideal for applications involving complex shapes, tight tolerances, and temperature fluctuations – especially where metal is too heavy or too costly to machine and assemble.
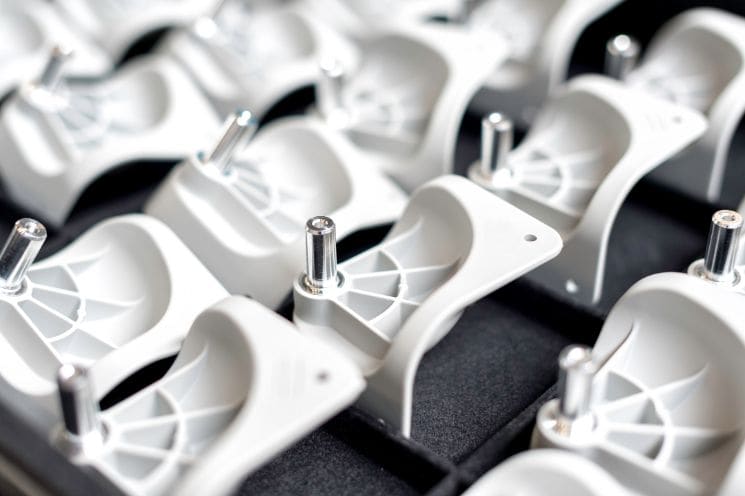
Corrosion resistance
Our range of chemical-resistant plastics can withstand even the most aggressive environmental conditions or sterilization processes, retaining their mechanical properties without added surface protection.
From acids to alkalis, from solvents to salt water, our comprehensive portfolio of advanced plastics covers an extensive range of chemical compatibility needs.
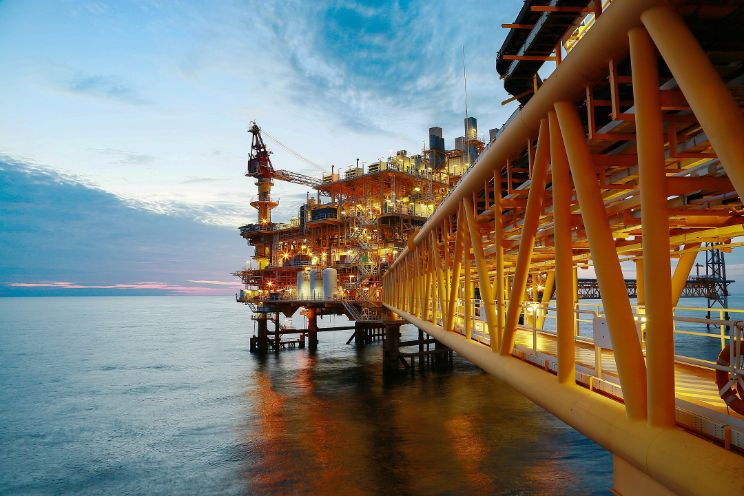
High-temperature resistance
For continuous operation at elevated service temperatures, our extensive range of high heat thermoplastic materials exhibit superior short- and long-term thermal stability, thermal insulation, flame retardancy, and resistance to radiation.
Our comprehensive portfolio consists of thermoplastics that retain their exceptional mechanical properties at operating temperatures ranging from 150°C to over 220°C, ensuring enduring performance even at extreme temperatures.
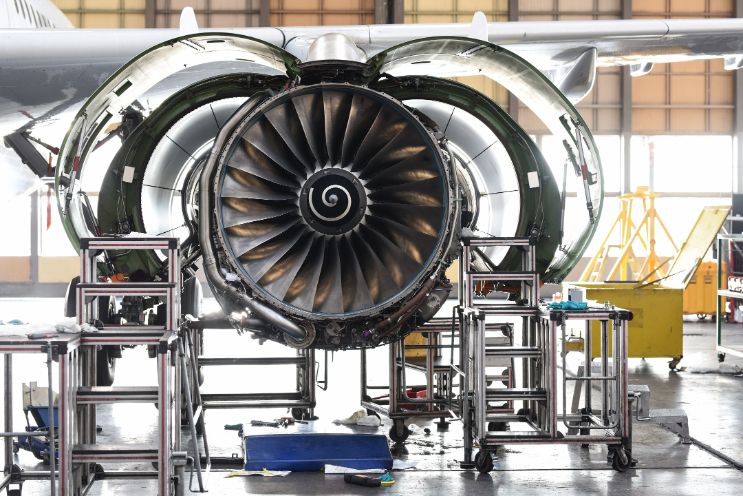
Weight reduction
All the performance at a fraction of the weight, thermoplastics and composites offer compelling productivity gains and cost savings compared with metals and open new doors for design freedom.
Our advanced engineering materials exhibit low density and cover a broad range of injection and machining capabilities, making it possible to engineer lighter, faster, better performing parts and components.
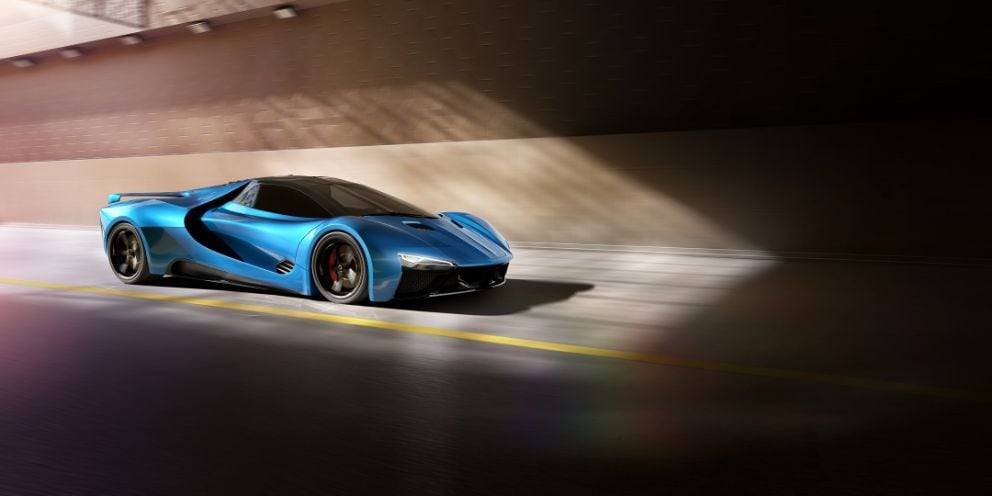
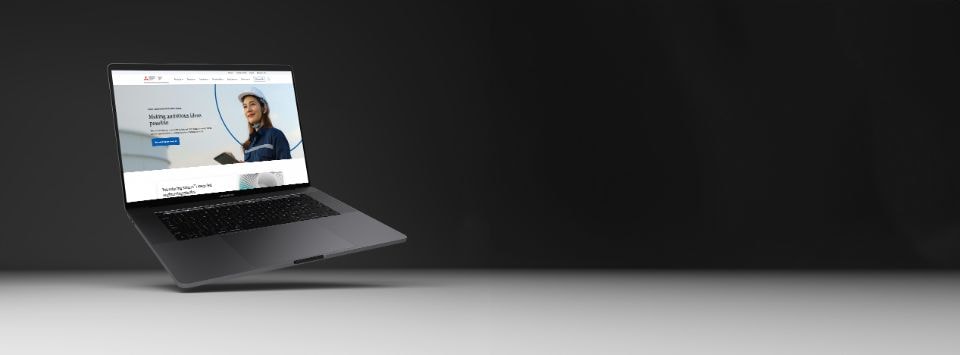
Processing techniques and shapes can impact not just the physical properties of materials, but the mechanical, chemical, and temperature properties as well. Our material development capabilities are always evolving to ensure we select the optimal material that will perform in every way you need it to.
Reducing costs and emissions with low-friction wing flap components
Our experts produced a self-lubricating polymer PAI solution that not only replaced the need for complex and labor-intensive parts, but also resulted in a lighter plane with reduced maintenance requirements and a lower risk of failure. This in turn led to better fuel efficiency and reduced CO2 emissions, helping to create a more sustainable aircraft.
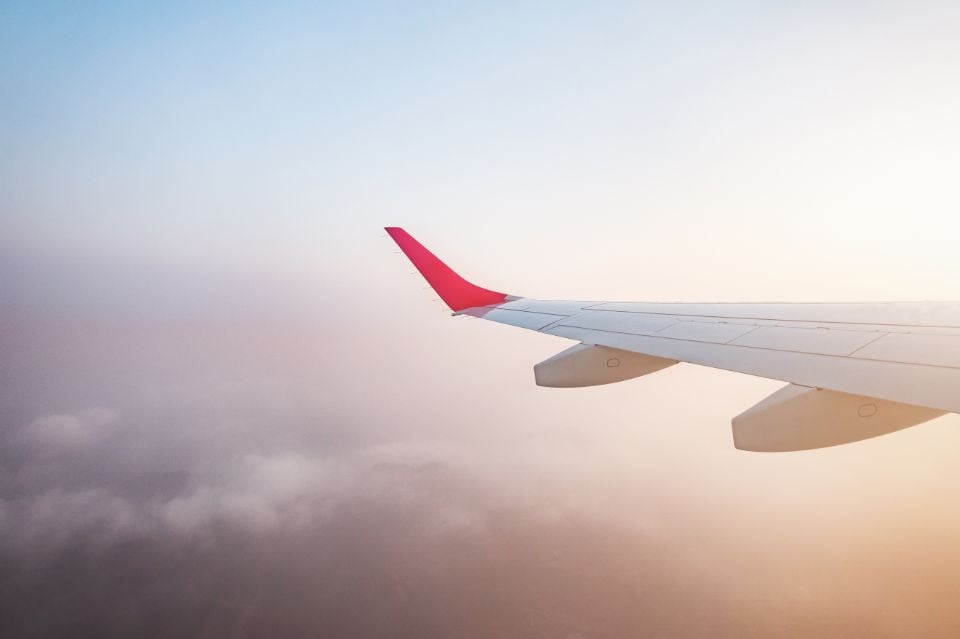
Replacing metal roller bearings in wind turbines through expertise and testing
By working closely with the OEM, we identified better-performing thermoplastic materials to develop more reliable parts for use in Yaw Slide Bearings, increasing cost savings and reducing time to market and service intervals. Our solutions were based not just on the initial yaw slide bearing, but the interaction of all mating parts within the turbine.
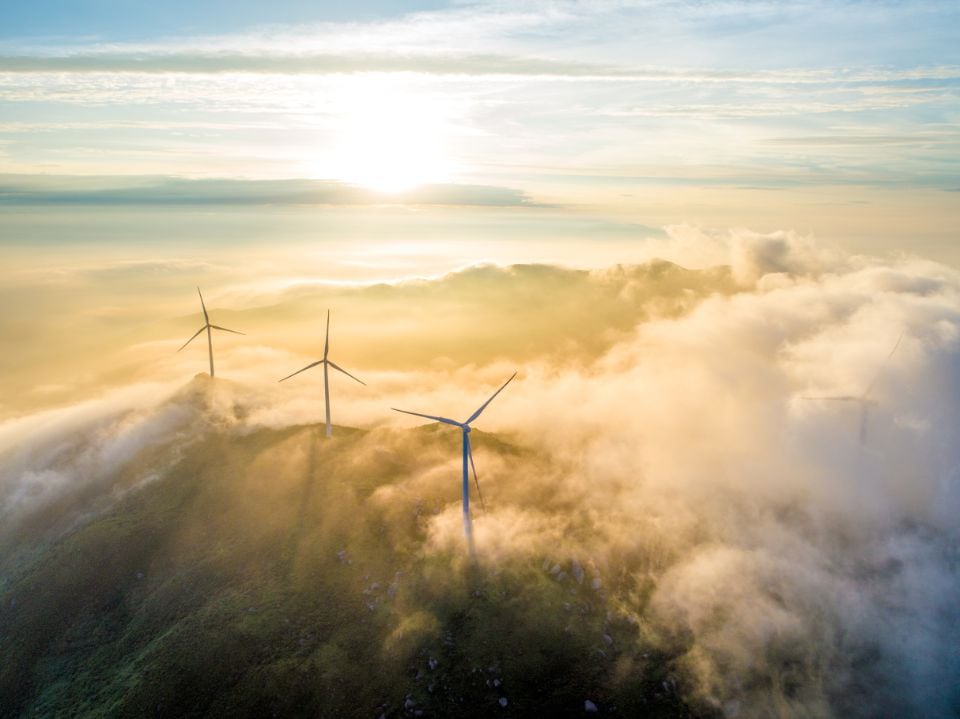
Improving food safety through part detectability
We helped our customers re-design their dairy processing food safe scraper blades for use in processing tanks. Our team not only identified highly 3-way detectable (Visual Metal X-ray) food safe materials that mitigated costly contamination risks, but also helped improve the overall equipment design processes.
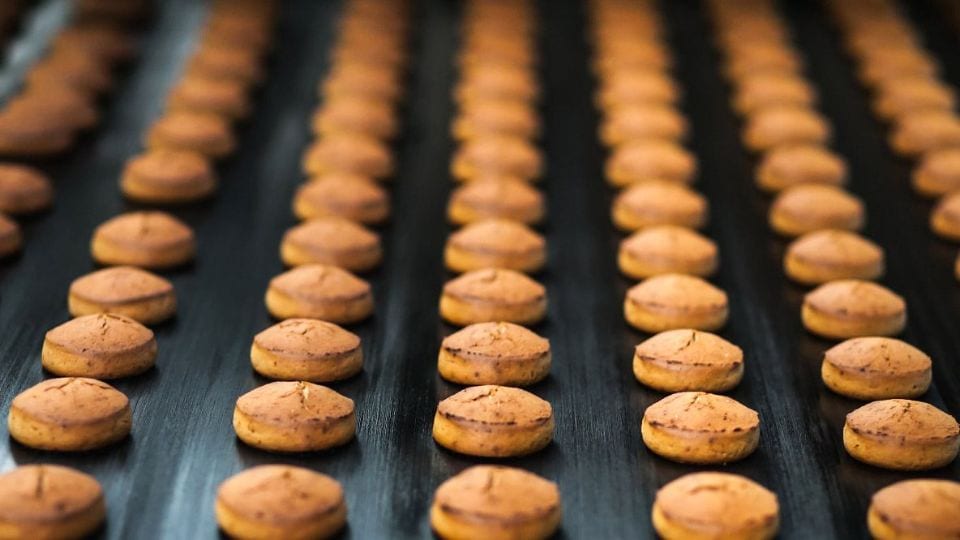
Molding carbon fiber composite brackets to replace steel
We partnered to help reduce the weight of steel brackets used in commercial vehicles, using mold flow analysis technology and our rigorous testing processes to inform the re-design of commercial vehicle brackets with carbon fiber composites in place of steel. Our KyronMAX™ injection moldable composites enabled a more sustainable, reliable, and lightweight bracket – resulting in a 79% overall weight savings.
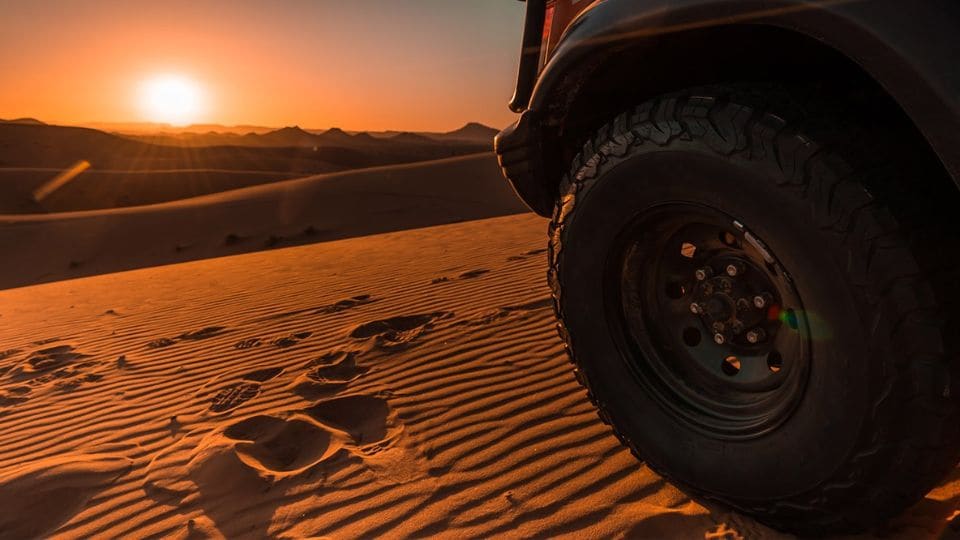
Get in touch with our specialist teams by filling in the contact form. We’re ready to meet your next challenge.
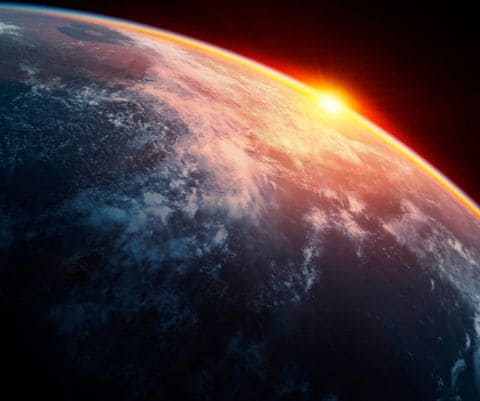

Recycling
From unused scrap material to used parts at the end of their lifecycle, our takeback programs simplify your disposal process while contributing to a circular economy. We also help reduce carbon footprints and quantify overall environmental impact through both material selection guidance and Life Cycle Assessments (LCAs).