As your partner in possibility, we connect you with the broadest portfolio of advanced thermoplastic and composite materials, as well as our deep understanding of applications for our products.
Our global teams provide end-to-end support and access to state-of-the-art technologies, leveraging our extensive industry experience to provide unlimited value to your development process. From ambitious initial designs to finished products, we offer a spectrum of services and capabilities to support your needs at every step of the journey, including in-house technologies for low volume, high volume, and scaling of production quantities.
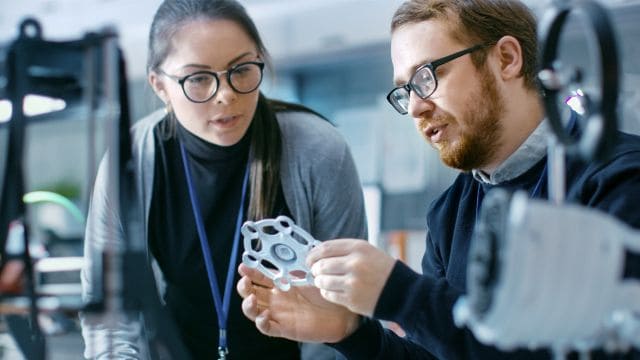
Design support
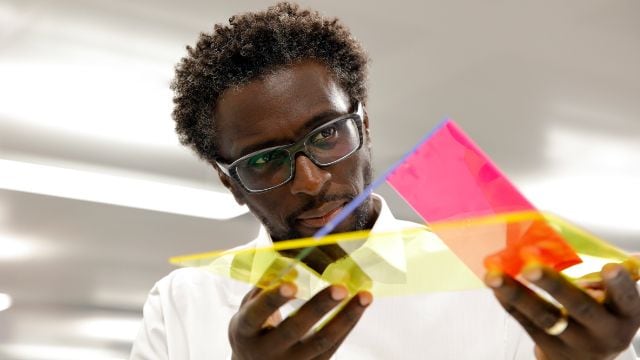
Material selection
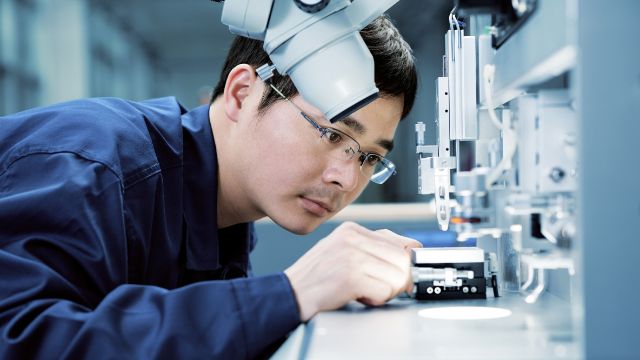
Prototyping, testing, and validation
With rapid prototyping technologies, in-house testing labs, and extensive expertise in flow and part analysis, we offer a complete spectrum of resources to quickly develop, test, and improve prototypes to get your product to market, faster.
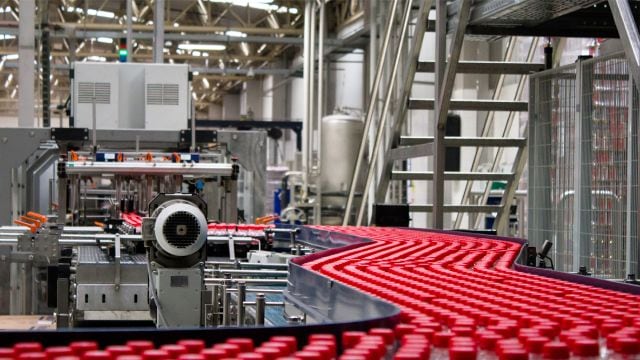
Production

Recycling
From unused scrap material to used parts at the end of their lifecycle, our takeback programs simplify your disposal process while contributing to a circular economy. We also help reduce carbon footprints and quantify overall environmental impact through both material selection guidance and Life Cycle Assessments (LCAs).
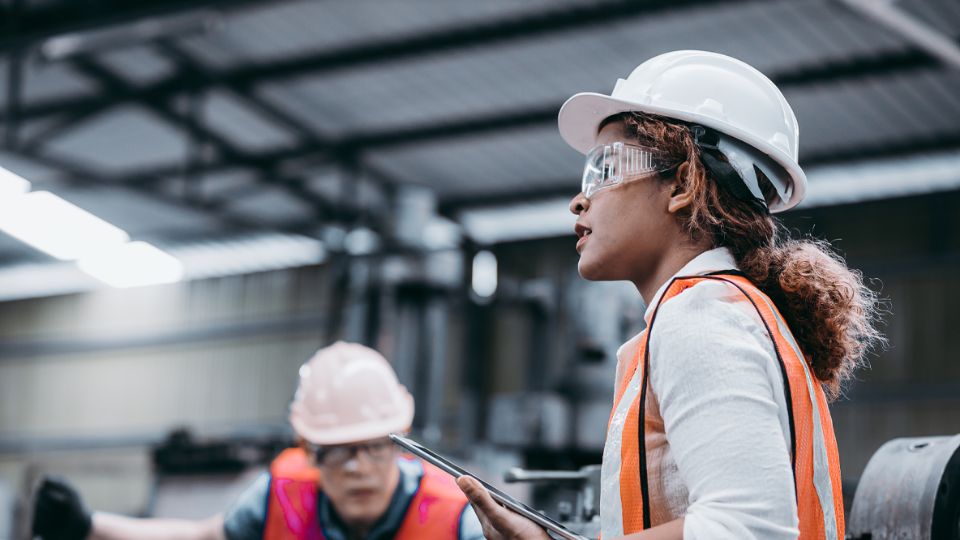
We work alongside engineers, fabricators, TIERs, OEMs, and suppliers around the world, providing services and expertise that generate tailored solutions, build innovative partnerships, and improve application efficiencies across an extensive range of leading industries.
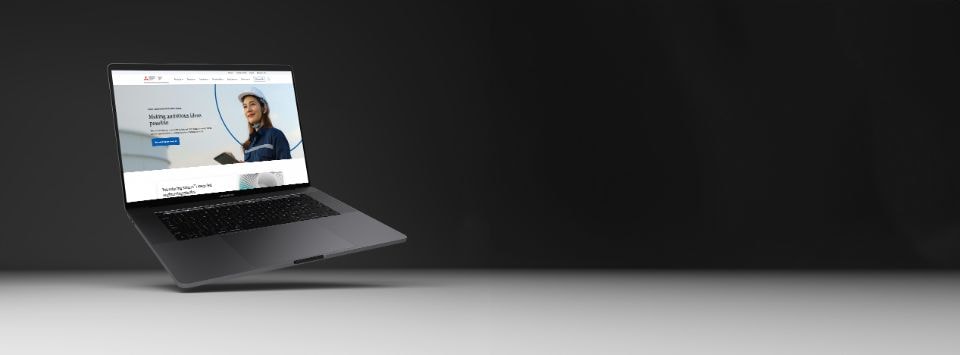
Get in touch with our specialist teams by filling in the contact form. We’re ready to meet your next challenge.
Contact us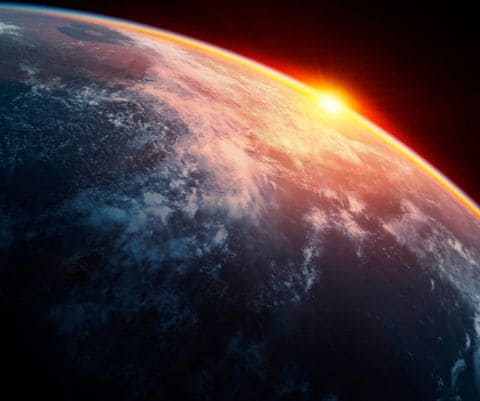