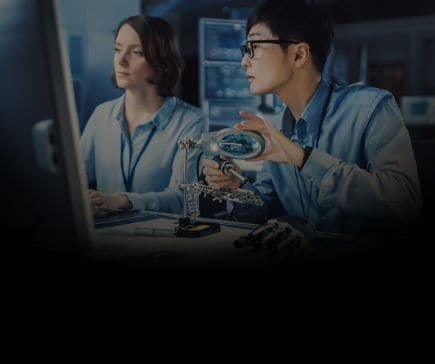
Innovative services and technologies
Our bespoke technologies and engineering platforms support the development of every project from idea to prototype and onto global manufacturing, helping our customers get their products to market faster.
Our bespoke technologies and engineering platforms support the development of every project from idea to prototype and onto global manufacturing, helping our customers get their products to market faster.
With quick access to a comprehensive portfolio of specialist polymer solutions, thermoplastics and composites, our intuitive systems and technologies make finding the right materials easier.
By balancing our commitment to the circular economy with new possibilities in materials recycling, our KAITEKI philosophy allows our customers to deliver on their global sustainability commitments.
Our network of materials and industry experts across 46 global sites provides proactive support, insights and inspiration to help customers in industries from aeronautics to bio-science make their ideas possible.
Our experts produced a self-lubricating plastic solution that not only delivered to our customer’s needs, but also resulted in a lighter plane with a lower risk of failure and reduced maintenance requirements. This in turn led to better fuel efficiency and reduced CO₂ emissions, which helped create a more sustainable aircraft.
Developing a plastic oil ring that is durable and easy to manufacture
Our experts partnered with our customer to develop an alternative to bronze oil distribution rings in gear boxes for use in wind turbines. The larger part size needs to withstand stress, be easy to manipulate, and reasonable to manufacture. Our alternative meets these requirements, while reducing machining time and cost.
Seeing beyond typical material applications, led to an innovative solution.
Working quickly, under huge time pressure, we used our broad portfolio of high-performance thermoplastic materials and rapid prototyping capabilities to help a manufacturer of equipment for the beverage bottling industry find a replacement part solution that improved overall throughput.
Our predictive mapping technologies and rigorous testing processes informed the final re-design of commercial vehicle brackets with carbon fiber composites in place of steel. Our KyronMAX™ materials’ unique mechanical properties and new mold filling design created a more sustainable, reliable, lightweight alternative.
Developing new materials suitable for high-tech, high-spec applications
Working in partnership with the OEM, we refined a material already in development, to meet their specifications while actively beta testing its performance in real world applications. Our enhanced polyamide-imide provides longer-lasting protection against oxygen cleaning erosion than typical polyimides (PI).
A new lining solution with minimal assembly required
Our customer was facing prohibitively expensive installation costs for silo liners. We developed a new type of liner assembled via interlocking segments and pre-inserted fastening elements, helping the customer overcome this challenge and stay competitive.
Looking for something specific? Get in touch with our specialist teams by filling in the contact form. We’re ready to meet your next challenge.
Contact us