Highlights
Semitron™ MPR1000 Case Study
We helped our customer overcome premature erosion of polyimide (PI) parts used in their etch tool vacuum chambers.
To our customer’s advantage, our industry knowledge and future-focused approach meant we were already developing an enhanced PAI material suitable for the demanding requirements of semiconductor etch processing.
Working together, we were able to refine the new material to meet their specifications while actively beta testing its performance in real-world applications. The result – our unique Semitron™ MPR1000, an enhanced polyamide-imide, provided much longer-lasting protection against oxygen cleaning erosion than typical polyimides (PI).
Industry: Semiconductor & Electronics, chip manufacturing
Solution: Development of a new advanced material to create more reliable parts using a high-strength, high-purity formulation
Products: Semitron™ MPR1000, an enhanced polyamide-imide (PAI)
Results: Stronger, more oxygen cleaning resistant parts resulted in less downtime and longer time between planned maintenance cycles
Improving part integrity to ensure continuous production
A large manufacturer of semiconductor processing equipment was experiencing rapid oxygen cleaning erosion and failure of the polyimide (PI) parts used in their vacuum etch chambers. The deterioration of the existing materials led to contamination issues and pre-mature costly planned maintenance shutdowns in production.
We needed to produce parts that would meet the strength and purity standards required and also withstand the intense oxygen cleaning processes needed to optimize tool uptime.
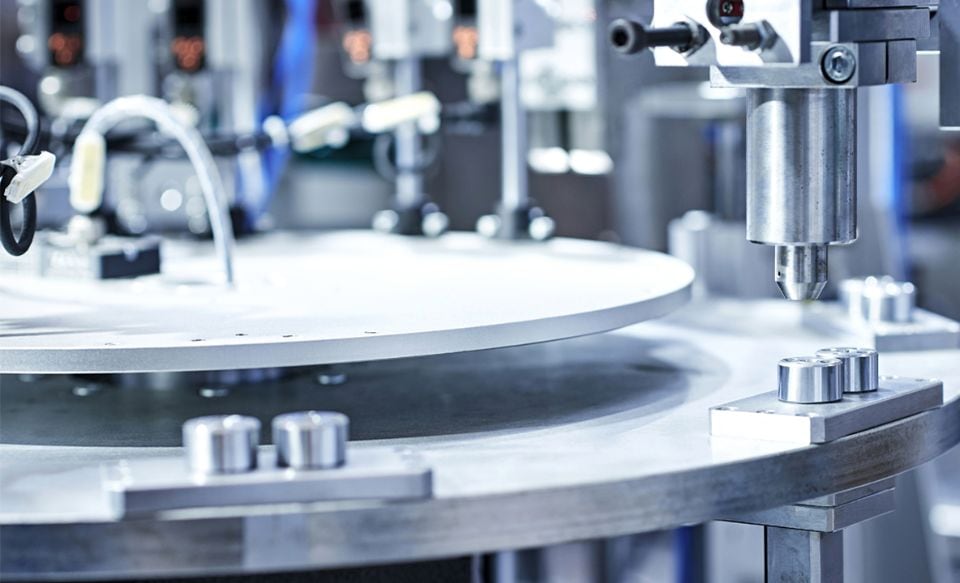
A proactive approach to advanced material development
Thanks to our industry knowledge and future-focused approach, we were already working on developing an innovative new polyamide-imide material that could survive both the etch tool process and the cleaning protocols, optimizing tool uptime with longer periods between required planned maintenance.
Working in partnership with the OEM's engineering group, we refined the material to their specifications while actively beta testing its performance in real world applications.
The result – our unique Semitron™ MPR1000, is an enhanced polyamide-imide, which ‘armorizes’ the parts and provides much longer-lasting protection against typical oxygen cleaning erosion than typical polyamides.
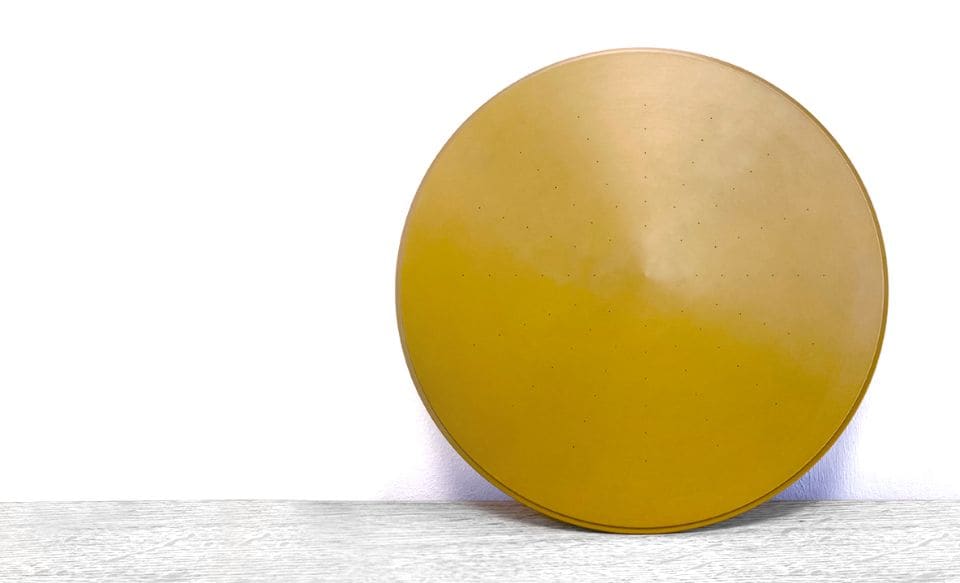
Fewer production delays, lower costs
Our new material, developed in partnership with the OEM, allowed for a new approach in formulating advanced polyamide-imides (PAI) and solved our customer’s production downtime issues.
In testing, Semitron™ MPR1000 proved to have a lower ionic erosion content and lower outgassing compared to typical polyimide materials on the market, generating less contamination, even after hours of cycling in standard etch vacuum tool environments. In addition, parts made of Semitron™ MPR1000 were shown to have about 10 to 15 times longer life spans, allowing for desired longer tool uptimes before required planned maintenance.
Using Semitron™ MPR1000 in their parts, not only helped OEMs run their equipment to their committed specifications, but also improved downtime by 90%, drastically increasing wafer processing capacity.
- Longer life in etch oxygen cleaning erosion environment
- Lower maintenance costs
- Increased production uptime between planned maintenance cycles
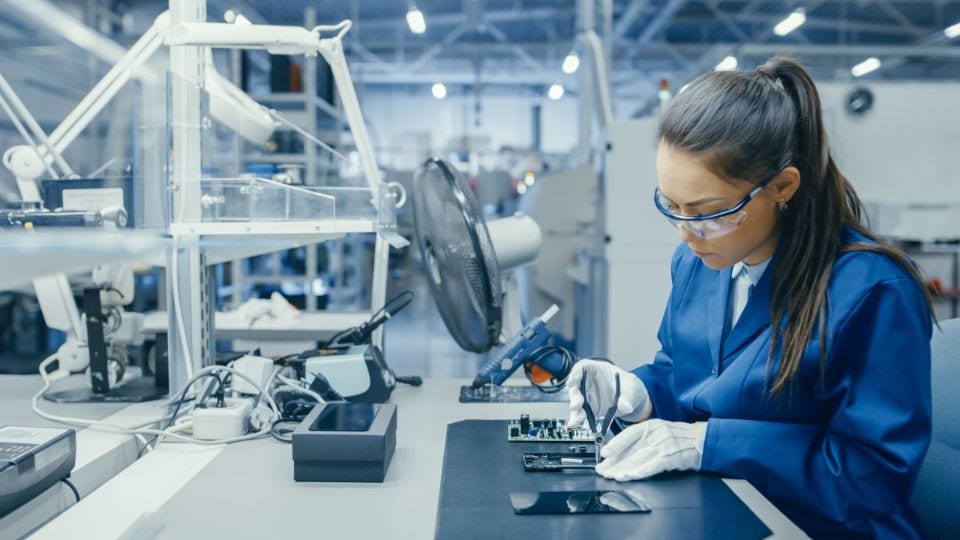
Our range of advanced high-performance materials and strong application expertise offer customers the precise solutions they need to eliminate processing variability, reduce risk and lower costs across a wide range of electronic and semiconductor applications.
Looking for something specific? Get in touch with our specialist teams by filling in the contact form. We’re ready to meet your next challenge.
Contact us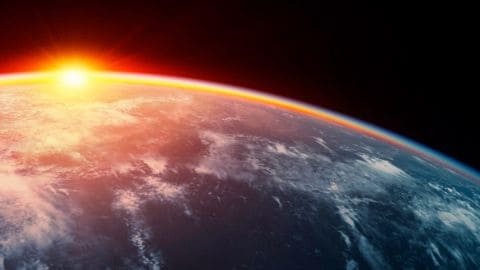