Duratron™ PAI case study summary
We worked alongside a major Aerospace manufacturer to help reduce friction and wear within their aircraft wings. A simplified, self-lubricating plastic solution replaced the need for complex, labor-intensive parts. This resulted in a lighter plane, with a lower risk of failure, reduced maintenance requirements, and a more sustainable carbon footprint.
Our unique self-lubricating PAI solution has been adopted by other manufacturers, further improving sustainability across the entire Aerospace industry.
Industry: Aerospace, Commercial Aviation
Solution: Development of integral, self-lubricating wear strips for wing flaps
Product: Duratron™ T4301 PAI
Results: A lighter plane with a lower risk of failure and reduced maintenance requirements
Maintaining structural integrity while increasing material flexibility
While developing a new aircraft with the goal of reducing fuel consumption and CO₂ emissions, a major Aerospace manufacturer selected flexible and lightweight composite materials with an aluminum structure for the wings.
However, ensuring continual wing flexibility, structural integrity and passenger safety meant these parts would require regular monitoring, lubrication, and maintenance.
The proposed solution required a highly complex control mechanism to ensure all roller bearings continued to function properly, even across the wide range of temperatures associated with changing altitudes, and extended exposure to various chemicals used around wing structures.
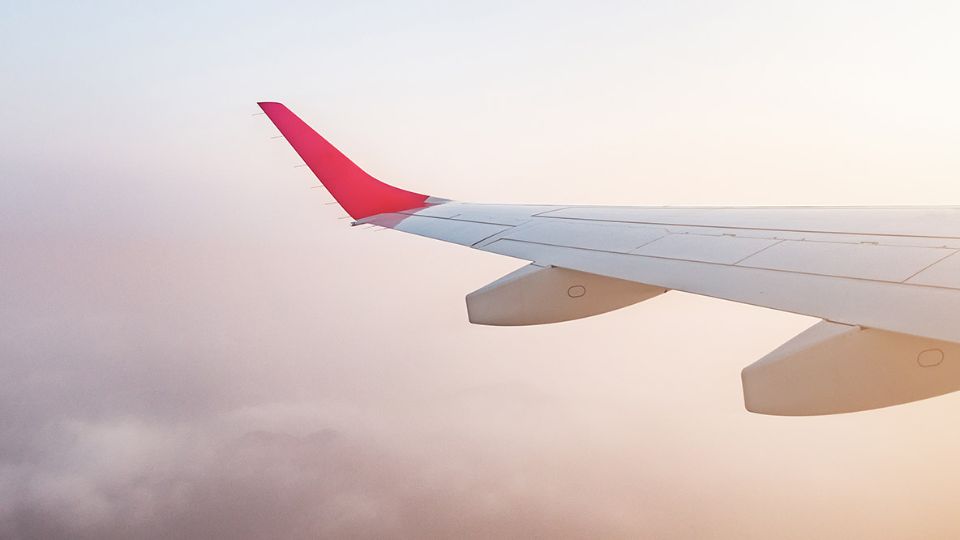
Removing friction and complexity
Instead of simply finding suitable engineering materials for a complex roller-based mechanism, we explored the possibilities and developed an alternative integral solution.
We recommended integrating a single self-lubricating plastic wear strip between between mating surfaces in the wing flaps, which would not only prevent friction, but also simplify the part and reduce maintenance requirements.
Working in conjunction with fabrication partners and the manufacturer’s engineers, we ran extensive tests to ensure the self-lubricating plastic material (Duratron™ T4301 PAI) met every client and industry requirement and was authorized for use in aircraft.
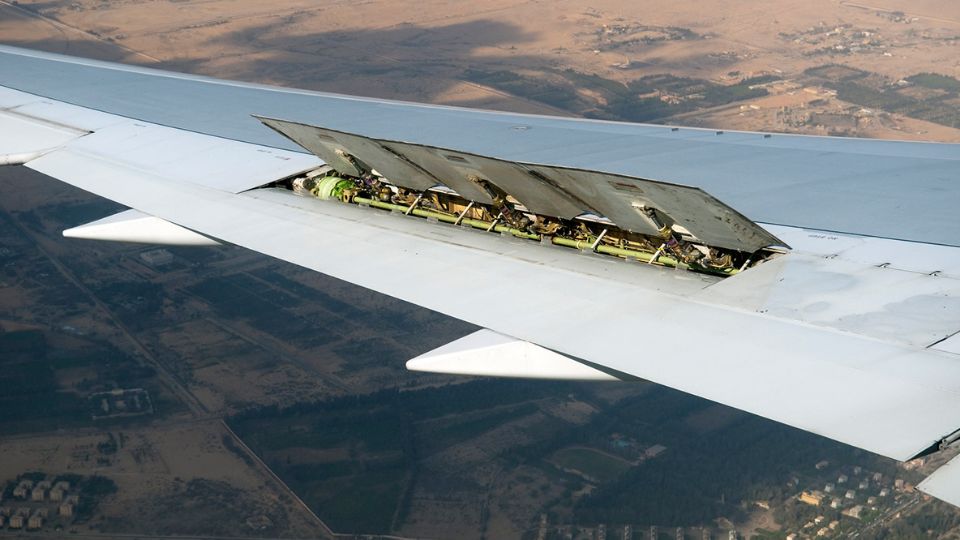
Integrated solutions for safe and sustainable aircraft
Thanks to its simplified design, the single self-lubricating plastic wear strip not only delivered to our customer’s needs but also resulted in a lighter plane with a lower risk of failure and reduced maintenance requirements. Additionally, it delivered better fuel efficiency and reduced CO₂ emissions, creating a more sustainable aircraft.
- Lighter aircraft
- Lower risk of failure
- Lower cost of maintenance
- Better fuel efficiency
- Reduced CO2 emissions
- More sustainable aircraft
Materials that enhance the aerospace industry
Since its installation and successful performance on our customers’ aircraft, our integrated self-lubricating plastic solution has been adopted by other OEMs. This has led to cost reductions and increased sustainability across the Aerospace industry.
- Cost reductions
- Increased sustainability
Increased part endurance, decreased maintenance costs
Re-imagining existing parts using more durable, self-lubricating plastic
Working with the OEM, we identified a fatigue-resistant material that became an Aerospace industry standard. An extensive material selection process included wear and mechanical testing, fluid susceptibility and temperature endurance; plus a number of qualification steps to ensure the new material met every requirement.
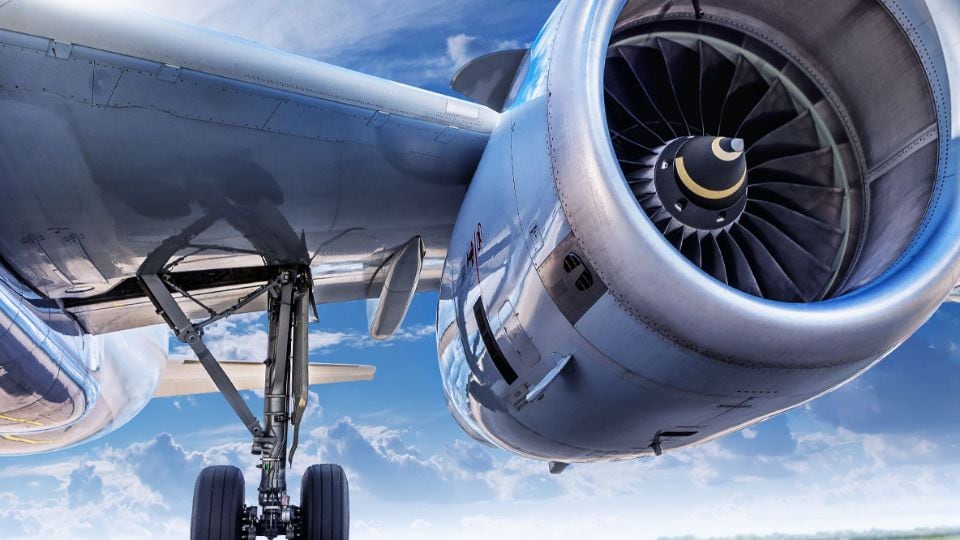
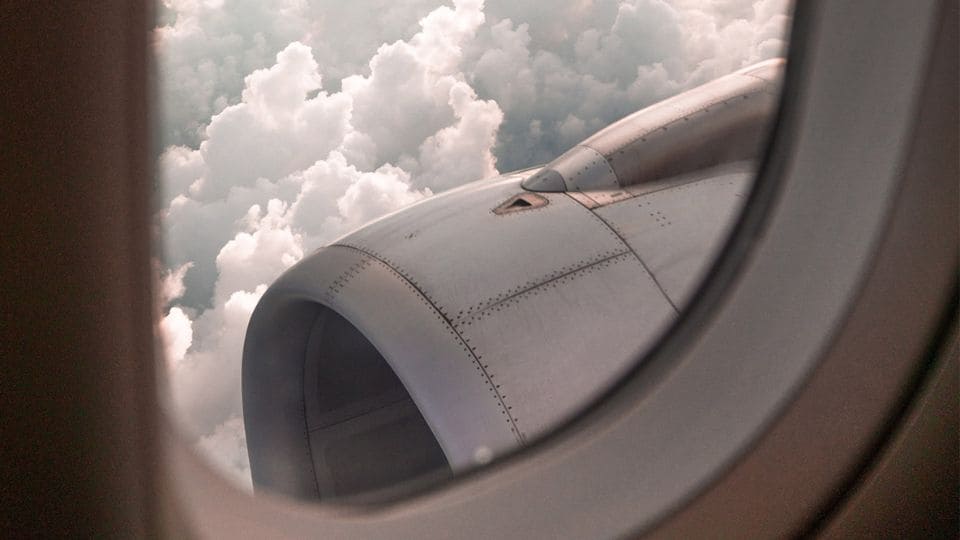
We’re dedicated to identifying and understanding the needs and trends that help drive innovation within Aerospace. Our portfolio of high-performance thermoplastics and carbon fiber technologies as well as our vertically integrated supply chain and global reach can help future-proof businesses.
We offer sustainable, scalable, and cost-effective solutions that can also help Aerospace customers meet their ever-changing safety and efficiency goals.
Looking for something specific? Get in touch with our specialist teams by filling in the contact form. We’re ready to meet your next challenge.
Contact us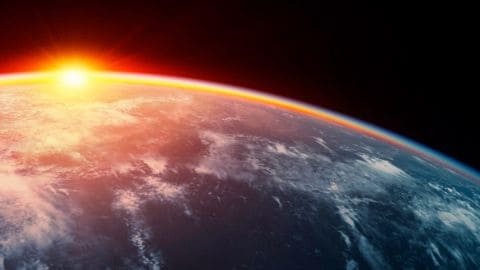