Semi-finished acetal, nylon, polycarbonate, PET, UHMW-PE products and beyond
Our engineering materials are good candidates to replace traditional materials ranging from bronze to rubber, helping to reduce weight and improve performance, reliability, and safety. They exhibit elevated properties for a broad range of applications and industries, including high mechanical strength, good machinability, electrical and chemical resistance, and consistence performance over a broad temperature range.
Many of these products are also physiologically inert, making them strong candidates for food contact applications, as per requirements of FDA and EU 10/2011 regulations.
Improve your application with engineering plastics and our end-to-end support. This portfolio is available in plastic stock shapes including tubes, rods, and sheets, along with custom machining.
(150°F - 250°F)
{{ productGroupName }} Family of Products
Standard Plastics
Versatile grades of polyethylene and polypropylene materials for applications up to 65°C.. These engineering polymers give you a range of high-performance properties, including greater impact strength, corrosion resistance, and superior malleability.
Advanced Engineering Plastics
High-performance PEI, PEEK, PSU, PTFE, and PPS products. Achieve predictable mechanical performance over a broad, elevated temperature change. Many of our Advanced Engineering Plastics also provide improved dimensional stability and creep resistance, electrical characteristics, and superior chemical resistance.
Extreme / Imidized Plastics
Explore our most advanced thermoplastics, including PI, PAI, and PBI engineering polymers. Properties like superior strength and thermal resistance help you overcome challenges with wear, friction, sealing, and more.
Looking for something specific? Get in touch with our specialist teams by filling in the contact form. We’re ready to meet your next challenge.
Contact us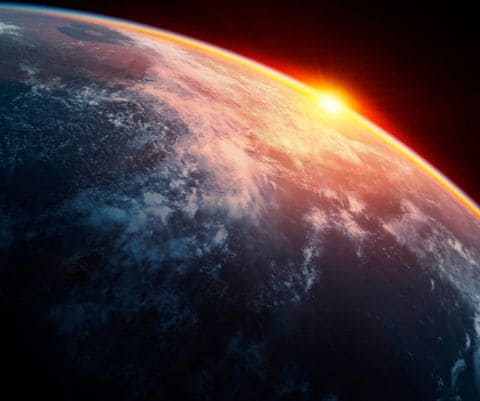