POM plastics: copolymer and homopolymer acetals
POM (polyoxymethylene), also known as acetal, is an engineering plastic that is often used in wet engineering environments. Known for its near-zero level of moisture absorption and excellent dimensional stability, acetal retains good mechanical performance even in applications requiring extensive machining, close tolerances, and/or high resistance to creep and deformation.
Where other materials may prematurely degrade or deform due to hydrolysis, chemical corrosion, or stress from machining, acetals maintain their performance and their form. As highly resilient materials with a tendency to "bounce back" to their original shape, copolymer and homopolymer acetals are indispensible to precision engineering applications where tolerance is key.
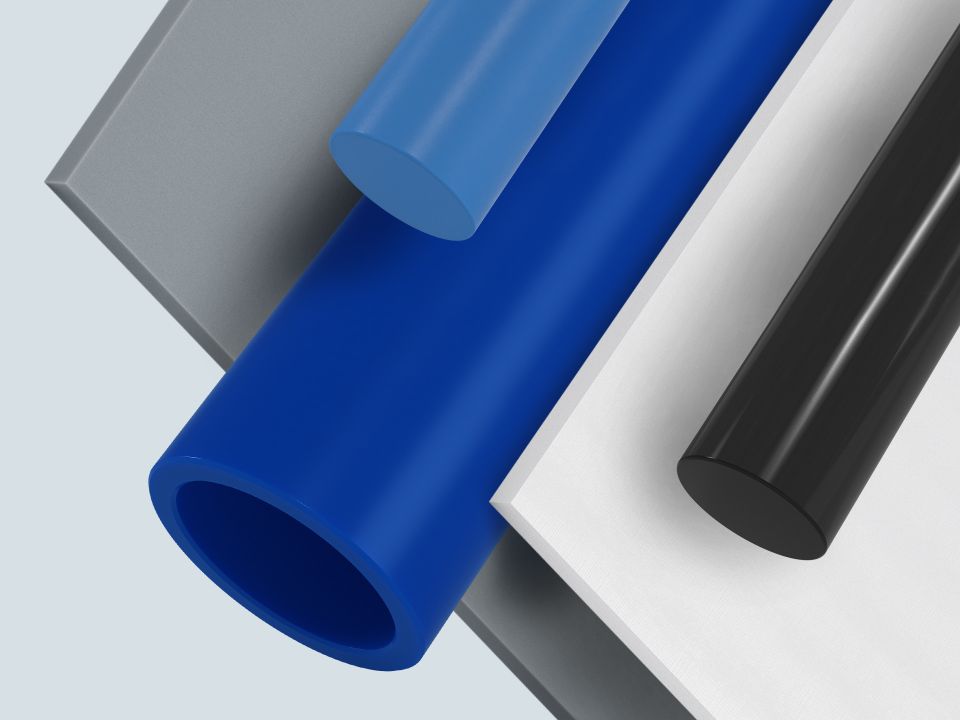
-
What is the difference between copolymer acetal (POM-C) and homopolymer acetal (POM-H)?
The key difference between copolymer and homopolymer acetal lies in the molecular structure that results from the polymerization method.
Homopolymer acetal is produced via the polymerization of a single monomer, resulting in a regular crystalline molecular structure. Copolymer acetal is produced by polymerizing two different monomers, resulting in a more amorphous structure.
Copolymer and and homopolymer acetals are both semi-crystalline plastics, but POM-H has a higher degree of crystallinity than POM-C.
How do the performance properties of POM-C and POM-H differ?
Generally speaking, POM-H exhibits better mechanical performance while POM-C exhibits better chemical resistance.
Homopolymer acetal outperforms copolymer acetal by about 15% in terms of hardness, stiffness, tensile strength, and compressive strength. Furthermore, it can bear about 10% higher loads before exhibiting creep.
While copolymer acetal may be less stiff and more ductile than hopolymer acetal, it has a significantly reduced degree of centerline porosity. Because of this, POM-C exhibits less outgassing and greater resistance to a broader range of chemicals compared to POM-H (pH 4-13 vs. pH 4-9). POM-C also displays hydrolysis resistance at higher temperatures (85°C vs. 60°C) and can withstand higher continuous operating temperatures in air (100°C vs. 90°C).
-
The following thermal properties of acetals are based on tests performed on our standard, unfilled Acetron™ / Ertacetal™ H POM-H and Acetron™ GP / Ertacetal™ C POM-C grade acetal shapes.
Heat deflection temperature of acetal
HDT test A 1.9 MPa (264 PSI)
POM-C POM-H ISO 75-1/-2 100°C 110°C ASTM D648 220°F 250°F Minimum and maxiumum service temperatures: Temperature range for acetals
POM-C POM-H Min. service temp. -50°C / -58°F -50°C / -58°F Continuous allowable service temp. in air (20,000 hrs) 100°C / 180°F 110°C / 190°F Melting point of acetal
Melting temperature (DSC, 10°C (50°F) / min)
POM-C POM-H ISO 11357-1/-3 165°C 180°C ASTM D3418 335°F 347°F POM thermal conductivity
Thermal conductivity is a measure of a plastic's capacity to transfer heat via conduction. Relative to most other engineering plastics, POM-H exhibits a slighly higher thermal conductivity. This makes homopolymer acetal a great candidate for applications such as heat sinks or thermal management components in electronic devices, where efficient thermal transfer and dissipation are important for maintaining the right operating temperature.
Thermal conductivity at 23°C (73°F)
POM-C POM-H W/(K.m) 0.31 0.31 BTU in./(hr.ft².°F) 1.6 2.5 Acetal coefficient of linear thermal expansion
The coefficient of linear thermal expansion (CLTE) is used to determine the rate at which a material expands as a function of temperature. Homopolymer acetals typically exhibit a lower CLTE than copolymer acetals, making POM-H the better choice over POM-C for dry, high temperature applications requiring dimensional stability.
ASTM E-831 TMA - µin./in./°F
POM-C POM-H -40 to 150 °C / -40 to 300°F 54 47 ISO µm/(m.K)
POM-C POM-H 23 to 60°C / 73 to 140°F 110 95 23 to 100°C / 73 to 210°F 125 110 -
The following acetal mechanical properties are based on tests performed on our standard, unfilled Acetron™ / Ertacetal™ H POM-H and Acetron™ GP / Ertacetal™ C POM-C grade acetal shapes.
Density of acetal
ISO 1183-1
POM-C POM-H Density 1.41g/cm³ 1.43g/cm³ Acetal coefficient of friction and wear rate
In dry environments, acetals are generally not as resistant to wear and friction as other similarly priced engineering plastics such as nylons. However, in wet environments, acetals (copolymer acetals, in particular) outperform many engineering plastics in terms of their wear behavior.
Tribological testing
Method POM-C & POM-H Wear rate ISO 7148-2 45µm/km Wear rate QTM 55010 200 In³.min/ft.lbs.hrX10-¹⁰ Dynamic coefficient of friction ISO 7148-2 0.3 - 0.45 Dynamic coefficient of friction QTM 55007 0.25 Tensile strength of POM
Tensile strength is a measure of the stress a material can withstand before breaking. Homopolymer acetals display significantly higher tensile strength than copolymer acetals.
ISO 527-1/-2 tensile strength testing
POM-C POM-H Tensile strength 66 MPa 78 MPa Tensile strain (elongation) at yield 15% - Tensile strain (elongation) at break 40% 24% Tensile modulus of elasticity 3,000 MPa 3,7000 MPa ASTM D638 tensile strength testing
POM-C POM-H Tensile strength 9,500 PSI 11,000 PSI Tensile strain (elongation) at yield 11% - Tensile strain (elongation) at break 40% 30% Tensile modulus of elasticity 400 KSI 9,000 KSI Acetal hardness and impact strength
Hardness & impact strength testing
Method POM-C POM-H Rockwell M hardness ISO 2039-2 84 88 Rockwell M hardness ASTM D785 88 89 Charpy impact unnotched ISO 179-1/1eU no break no break Charpy impact notched ISO 179-1/1eA 8 kJ/m² 10 kJ/m² Izod impact notched ASTM D256 1 ft.lb./in 1 ft.lb./in POM flexural modulus and strength
Flexural testing
Method POM-C POM-H Flexural strength ISO 178 91 MPa 106 MPa Flexural strength ASTM D790 12,000 PSI 13,000 PSI Flexural modulus of elasticity ISO 178 2,660 MPa 3,450 MPa Flexural modulus of elasticity ASTM D790 400 KSI 450 KSI -
Thanks to its low moisture absorption rate and a low centerline porosity, copolymer acetal exhibits good resistance against chemicals in the pH range of 4 to 13.
Copolymer acetal exhibits good resistance to many common solvents, lubricants, hot water and steam, ketones, esters, and aqueous solutions of acids and alkalis.
Copolymer acetal has poor compatibility with chemicals such as strong acids and alkalis, phenols, cresols, and halogens.
Due to greater centerline porosity, homopolymer acetal exhibits reduced resistance to all of these chemicals compared with copolymer acetal. POM-H is only recommended for applications involving chemicals in the pH range of 4 to 9.
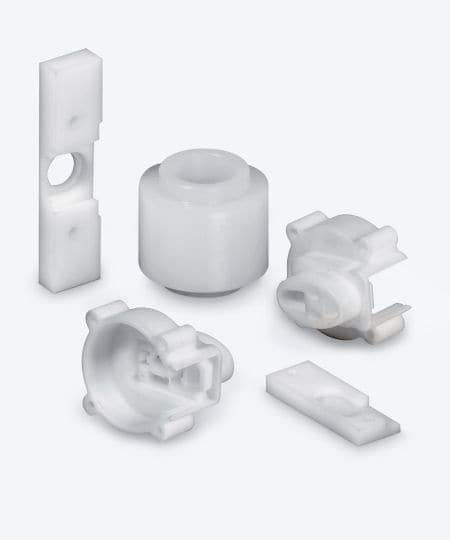
- Fluid management - With good chemical resistance and low moisture absorption, POM-C is an excellent material for components in wet, potentially corrosive environments, such as valves and seals.
- Electronics & semiconductors - Thanks to their high electrical strength and low porosity, copolymer acetals are commonly used in applications involving high levels of electrostatic.
- Complex, low weight parts - Acetals are often chosen to replace metals in applications where component weight is a determining factor. With great dimensional stability, easy machining, and good mechanical performance, POM-H can reduce component weight with no loss of functionality.
- Food processing & packaging - Especially in wet environments, food grade acetals offer excellent wear and impact resistance for food processing applications. They are also resistant to common cleaning agents.
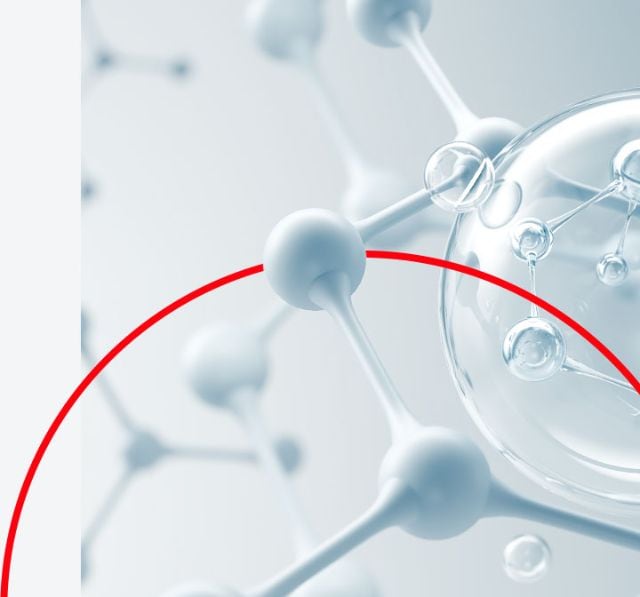
MatFind
Quickly find the optimal engineering plastic for your application. Simply input the performance properties you require, and MatFind will help you filter and compare materials.
Semitron™ Product Family
Developed to optimize the performance of semiconductor and electronics device manufacturing equipment, the Semitron™ family spans polyolefins to imidized materials, including semiconductor-grade POM.
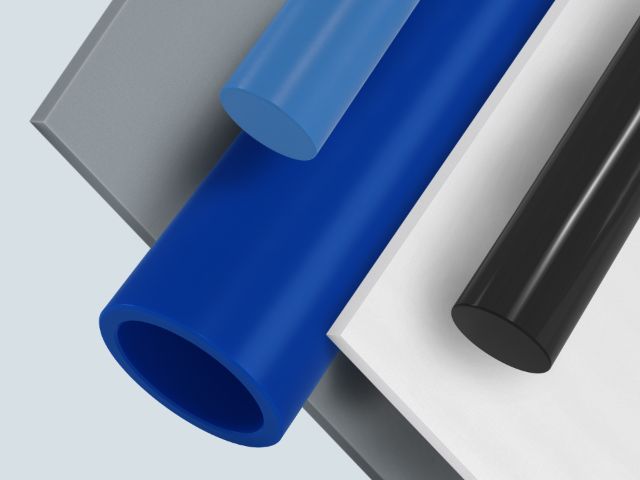
Acetron™ / Ertacetal™ Family of Products
Mitsubishi Chemical Group offers both homopolymer and copolymer grades of POM. Special formulations include an enhanced bearing grade material, a metal- and x-ray-detectable acetal, food-contact compliant acetals, and a range of colors.
Looking for something specific? Get in touch with our specialist teams by filling in the contact form. We’re ready to meet your next challenge.
Contact us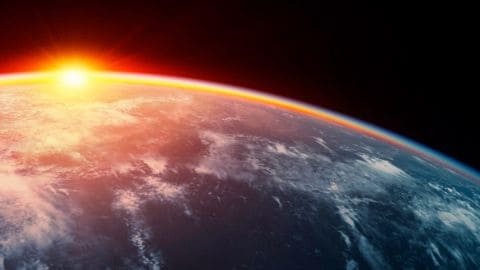