Resistance ratings key
- A: Resistant. Little or no change in weight. Small effect on mechanical properties. Generally suitable for practical use.
- B: Partially resistant. Over time, there is a distinct deterioration in mechanical properties and a change in weight. In many cases, a short exposure may be considered allowable.
- C: Non-resistant. After a short time, the material is seriously affected (considerable reduction of the mechanical strength and changes in weight). Using the material under these conditions is not recommended.
- O: The material dissolves in the chemical.
The resistance ratings given for Ertalon™/Nylatron™ and Ketron™ PEEK are in the first instance valid for the unreinforced grades. For glass fiber reinforced grades (Ertalon™ 66-GF30 PA66 and Ketron™ PEEK GF-30 PEEK), note that they are more affected by hot aqueous solutions than the unreinforced grades. Therefore, preliminary testing under actual service conditions is strongly recommended.
Concentration (%)
A number, e.g. 20, indicates “20 g of solute per 100 g of aqueous solution” (20% by weight)
- UD: Undiluted (technically pure chemical)
- SS: Saturated aqueous solution (at 23°C)
- CA: As commercially available
Temperature (°C)
- RT: Room temperature (15 - 25 °C)
Chemical resistance describes the ability of a material to withstand a chemical attack for a specific period without significant deterioration of its performance properties. Materials with high chemical resistance are also likely to be resistant to material breakdown due to a chemical attack.
Chemical resistance can be a significant advantage of engineering plastics over metals, allowing end products to withstand harsh environmental conditions, disinfection, and cleaning. If a material has insufficient chemical compatibility for the application, the consequence could be cracking, swelling, softening, and shortened service life.
When selecting the appropriate chemically resistant plastic, engineers should consider the specific influencing factors in their application, such as operating temperature, mechanical load, or fire performance requirements. At Mitsubishi Chemical Group, we offer a portfolio of chemically resistant engineering plastics that offer high reliability and operational safety.
When it comes to chemical resistance, engineering plastics offer many advantages over metals.
Additional coatings may help metal resist chemicals, but this extra layer can add lead time and costs. A plastic with the right chemical compatibility, on the other hand, will require no secondary finishes, resulting in a faster tooling process and a more lightweight part for improved performance.
A chemical attack occurs when plastic and a chemical are not compatible. The chemical causes the polymer structure to weaken or break down, leading to a loss of performance properties which can in turn cause part failure. A chemical attack can also lead to ESC (environmental stress cracking) which is a thin, spiderweb-like cracking that could seriously affect a part's performance.
In your application, you may be experiencing part failure due to a chemical attack, but what may have caused this? Common sources of chemical exposure in operating environments include:
Washdowns: Cleaning processes used to sterilize, disinfect, and sanitize conveyors, mixing equipment, and other machines that could harbor harmful bacteria, viruses, and other contaminants. This process is usually seen in the Food and Beverage and Pharmaceutical industries. Making sure you are using a plastic that is both food contact compliant and can withstand chemical exposure at high temperatures is crucial in these cases.
Lubricants: Does your application require lubricants to be successful? Some lubricants (mineral or synthetic-based) can cause plastics to crack and swell over time. Engineers and designers should consider if the material will encounter lubricants, oils, or grease within the application. It may take prolonged exposure to the lubricant or grease for the damage to appear.
When selecting a material with the correct chemical resistance for your application, you must also consider what physical conditions your part will be exposed to:
Fire performance:
Does your application need to include specific fire performance requirements, along with being chemically resistant? Keep in mind that flame retardants can affect the chemical resistance of your material.
Electrical performance:
This is important to consider when storing media with a low flash point, such as lubrication and heating oils and petrol.
Weather exposure:
When certain materials are exposed to severe weather or UV radiation for an extended time, they can be physio-chemically influenced by atmospheric oxygen. Loss of mechanical properties, discoloration, and brittleness may occur.
Looking for something specific? Get in touch with our specialist teams by filling in the contact form. We’re ready to meet your next challenge.
Contact us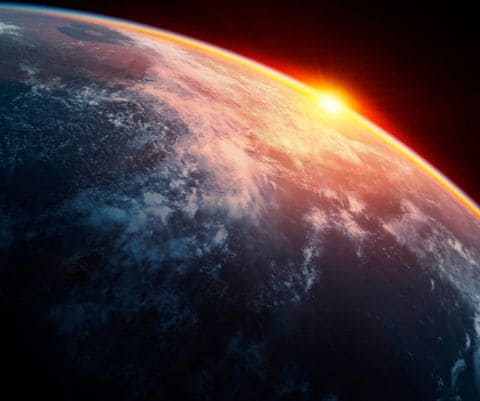