Product data sheets
Access PDF data sheets with extensive technical data about our polymer materials, including thermal, electrical, and mechanical property values.
Regulatory information
Find up-to-date compliance information for our materials and support with regulatory frameworks around the globe.
Certifications & ordinances
Learn about top-tier quality assurance and state-of-the-art in-house testing capabilities, and download our ISO customer quality certifications.
Safety data sheets
Access up-to-date information about material composition, as well as the safe handling, storage, and disposal of our products.
Reference manuals
Want to learn more about working with engineering materials? Explore our library of helpful guides about material selection, machining, component design, and more.
Industry information & brochures
Your industry presents unique engineering challenges. Explore solutions developed for applications in specific industries from food processing to semicon manufacturing and beyond.
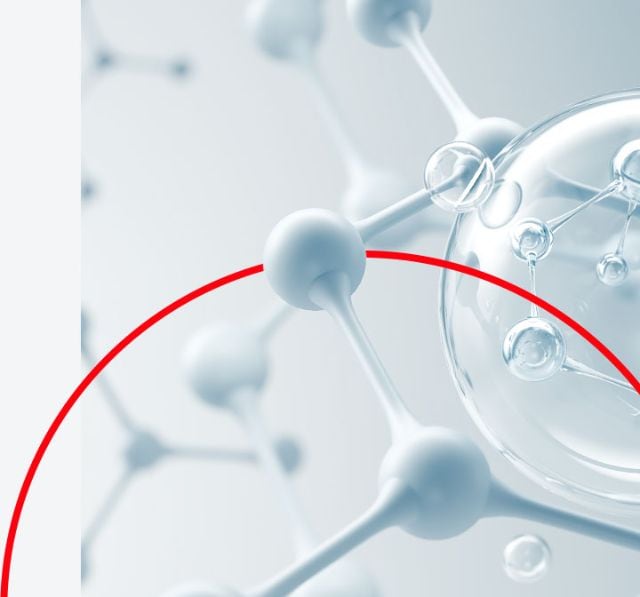
MatFind
Quickly find the optimal engineering plastic for your application. Simply input the performance properties you require, and MatFind will help you filter and compare materials.
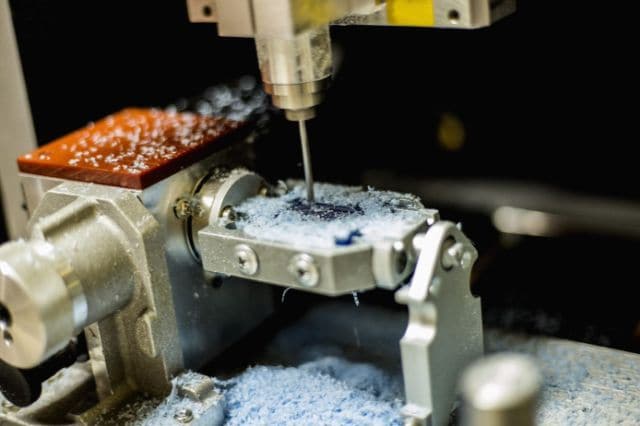
Machining information
Achieve the best results with your finished components by applying these guidelines for machining plastic shapes.
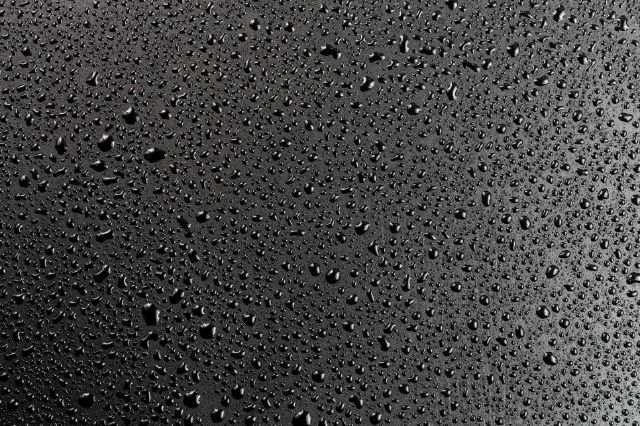
Chemical resistance database
Not sure which materials can withstand the chemicals present in your operation? Assess the chemical compatibility ratings of engineering plastics with this handy tool.
See all your order information, lead times, and pricing in one place. MCAM Connect gives you access to the tooling you need!
Are you already a customer of Mitsubishi Chemical Group and would like to start using Connect? Contact your account manager to get started.
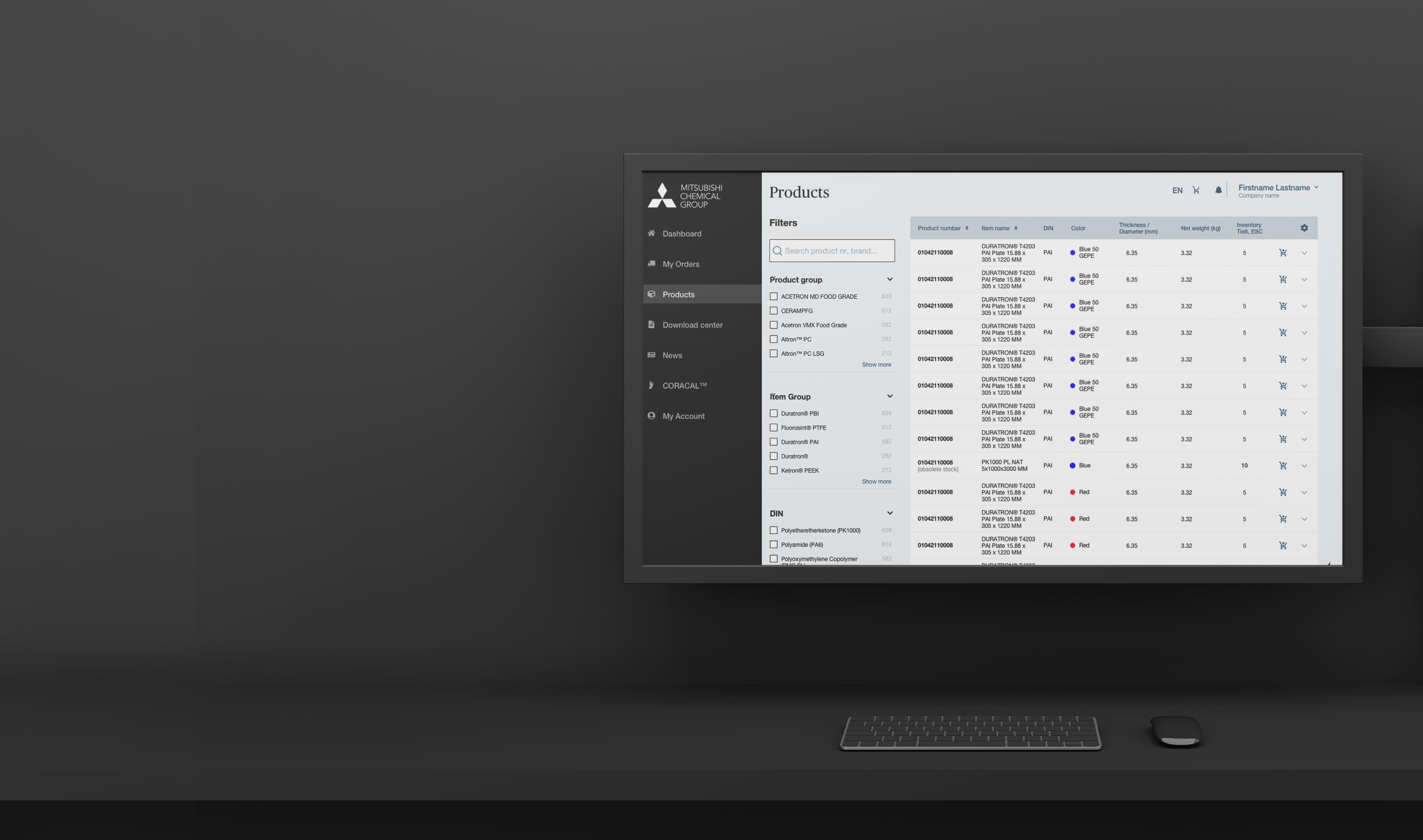
Terms & conditions
Access detailed information regarding our legal terms and usage for our partners in the Americas and Canada; Europe, the Middle East, and Africa; and Asia.
Terms of use
Details on our copyright policy, trademarks, patents, and more, including usage of information available on our website.
Privacy
Our policies on data security, data collection, and personal data usage.
Get in touch with our specialist teams by filling in the contact form. We’re ready to meet your next challenge.
Contact us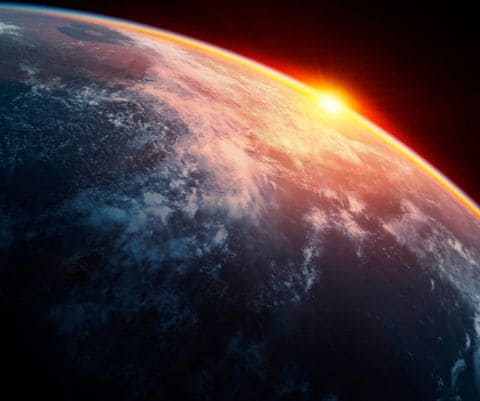
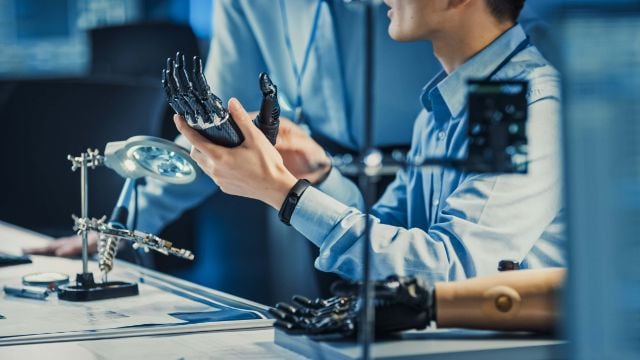
Applications
Whether you are replacing a troublesome metal part, designing an innovative new component, or looking to reduce the climate impact of a product – engineering thermoplastics and composites can make it possible.
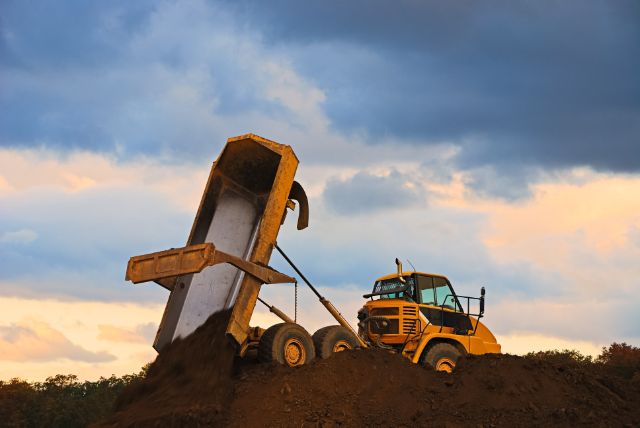
Industries
Your industry, our materials. Learn how advanced thermoplastics and composites are adding value to engineering applications in your field.
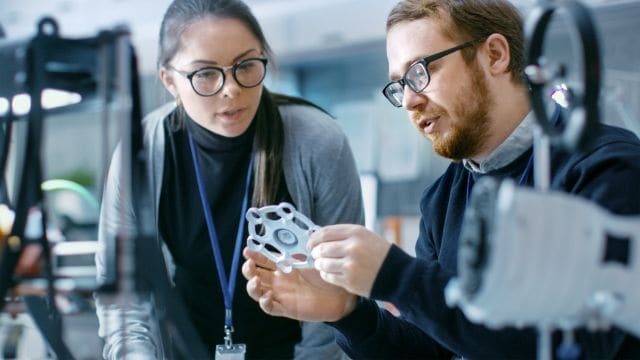
Services
We don't just sell high-performance materials – we work with you over the course of your project to support material selection, design, prototyping, production, recycling, and more.
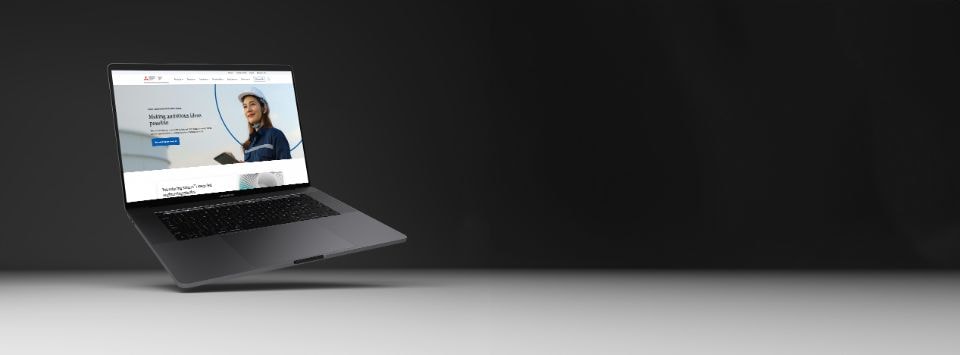