Dimensional stability is a measure of a material’s ability to retain its fit, form, and functional properties throughout its lifecycle.
Engineering plastics are subject to a myriad of extreme conditions – from machining of parts to intense operating environments – that can impact how well both the material and the overall part function throughout their lifecycles. The material property that is most often affected by a lack of dimensional stability are the dimensions of the finished part, as excessive moisture or extreme temperature environments can cause materials to expand or contract.
Even if a part will not be exposed to particularly demanding operating conditions, it is still important to consider the dimensional stability of a material when machining the part to close tolerances – a process that subjects a material to high levels of mechanical stress.
In order to ensure performance and safe operation throughout a part’s lifetime, a plastic material’s dimensional stability is one of the key performance properties that must be taken into consideration during both material selection and part design. Mitsubishi Chemical group offers a comprehensive portfolio of engineering polymers covering an array of dimensional stability needs.
There are many engineering applications in which the dimensional stability of the materials involved must be considered. Sealing components are an example of parts requiring dimensionally stable materials, as changes to the dimensions of the seal could result in leakage. Dimensional stability should also be a consideration in choosing a material for parts that will be subject to regular cleaning with steam, chemicals, or hot liquid.
Beyond the final application of the part, the dimensional stability of a material impacts machining and the final tolerances that can be acheived. With less dimensionally stable polymers, the build-up of heat during machining and internal stress in the underlying shape may make it difficult to consistently machine parts involving precise dimensions with tight tolerances. Sophisticated processing and state-of-the-art machining technology, along with polymers exhibiting superior dimensional stability, make it possible to machine intricate parts with small scales and tight tolerances, such as electrical connectors and test sockets.
Although metals are generally more dimensionally stable than plastics, many engineering plastics also exhibit excellent dimensional stability – as well as several clear advantages that make them preferrable to metals in many applications.
Our dimensionally stable thermoplastics can perform comparably, while also providing other key benefits that would be unattainable with metal parts. These advantages include:
- Lower raw material costs
- Lighter weight finished parts
- Specific electrical properties
- Resistance to chemical corrosion
- Improved friction and mating behavior
For applications requiring additional dimensional stability, thermoplastics can be reinforced with glass fibers or other fillers. Reinforced polymer grades typically exhibit greater thermal dimensional stability compared to unfilled grades, as well as other improvements in mechanical, chemical, and dielectric properties.
High-pressure microfluidizer seal from Fluorosint ™ 207 PTFE
The challenge: A mircofluidizer is a piece of medical equipment in which pharmaceutical liquids are subjected to 4,000-10,000 psi and high shear forces as a means of reducing their particle size. After each use, the machine is steam sterilized in an autoclaving cycle of at least 20 minutes. With the existing UHMW-PE seal, this sterilization process caused the intensifier pump to swell and shrink, leading to leakages and loss of pressure in the unit.
The solution: Our Fluorosint ™ 207 PTFE material was chosen to replace the UHMW-PE component because of its exceptionally low moisture absorption, excellent dimensional stability, and unmatched non-permeability in steam.
The results: With improved resistance to creep and steam, Fluorosint ™ 207 PTFE significantly extended the service life of the microfluidizer seal. The new part was able to withstand repeated autoclaving cycles and retained its mechanical strength far longer than conventional PTFE and PE materials.
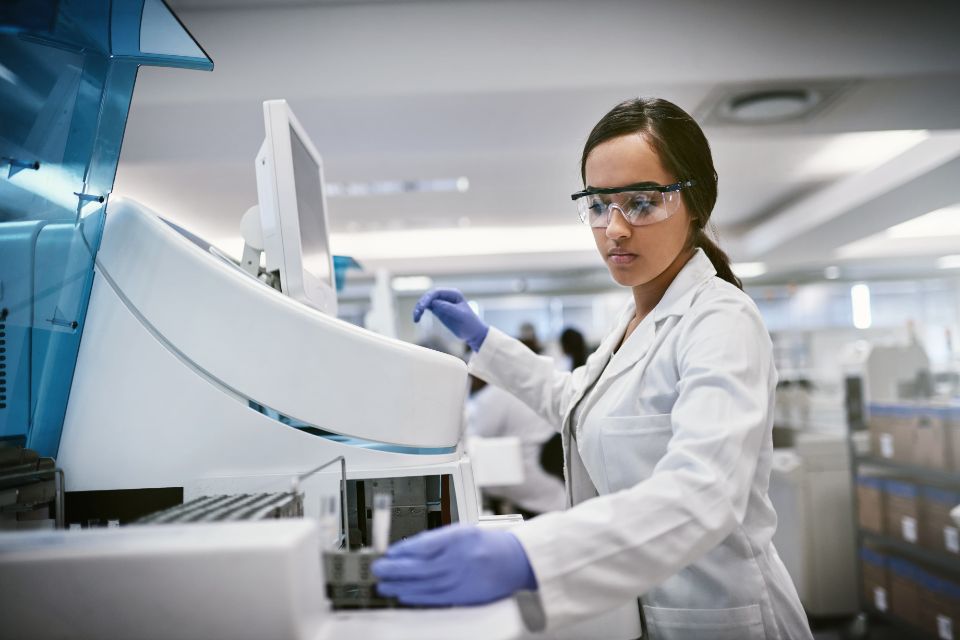
Pistons and valve spools in liquid filling equipment from Ertalyte™ PET-P
The challenge: Valve spool and piston components in liquid filling machines were historically made from stainless steel. Such parts are costly and require constant lubrication, prompting the OEM to look for FDA-compliant plastic materials to replace them. The polymer would need to have exceptionally low moisture absorption and withstand constant contact with liquids ranging from sauces and food to cleaning agents. Additionally, the parts would need to be machined to tight tolerances to perform as needed.
The solution: Not all polymers met the requirements – UHMW-PE could not withstand the pressure of the application, acetals wore too quickly, and nylons absorbed too much moisture. Ertalyte™ PET-P was chosen for its excellent wear performance, minimal moisture absorption, and low thermal expansion, making it ideal for this application.
The results: The Ertalyte™ PET-P rods delivered cost savings and performance advantages without sacrificing the accuracy of the filling systems. The machined PET-P parts hold +/- 0.0007- inch tolerances on the diameter of the piston and valves. Thick wall sections, very tight tolerances, and limited production volumes made machining the best manufacturing choice for the parts.
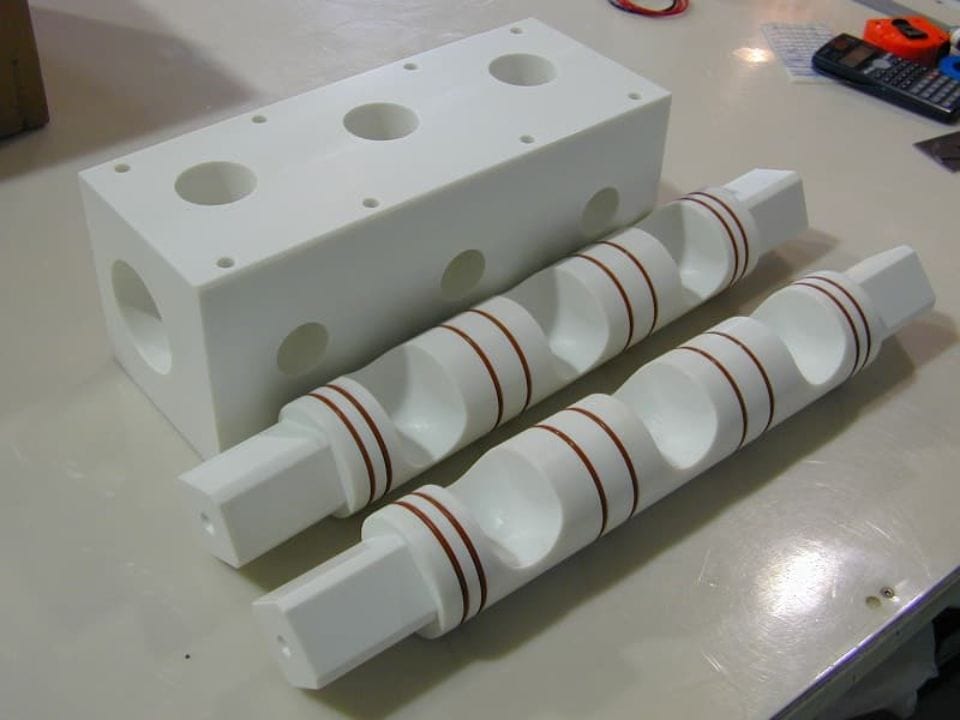
-
The coefficient of linear thermal expansion (CLTE) is used to determine the rate at which a material expands as a function of temperature.
For each of our materials, Mitsubishi Chemical Group performs the ASTM E- 831 / ISO 11359 to calculate the rate of thermal expansion in three different temperature ranges: 73°F to 210°F (23°C to 100°C), 73°F to 300°F (23°C to 150°C), and over 300°F (150°C).
For each test, a material specimen is placed in a furnace. The temperature in the furnace is raised at a specified, controlled rate over the testing temperature range until the material fails at a maximum temperature. The changing dimensions of the specimen are recorded in detail.
-
In order to predict the rate at which a material will deform under constant mechanical stress in a given temperature range, we implement creep behavior testing across our portfolio.
We perform dynamic mechanical analysis (DMA) to understand the degree to which the dimensions of a plastic component will undergo creep when subject to varying degrees of compressive strain for elapsed periods of time.
The variables involved in DMA testing are temperature, time, and stress. In the following charts, the creep behavior of a selection of our materials was observed for 100,000 hours at room temperature (23°C) at the boiling point of water (100°C). During this time, specimens were subject to mechanical stress. As can be seen in the graphs, at lower temperatures, the load a material can withstand before deforming by 1% is significantly higher than at more extreme temperatures, and as time progresses.
-
Water absorption testing helps to evaluate how quickly a material will assimilate water when exposed to moisture, thus potentially altering its size, weight, and mechanical and electrical properties.
To calculate moisture absorption behavior, we perform the tests ISO 62 and ASTM D570, depending on the material specimens available.
These water absorption test methods involve submerging a thermoplastic specimen in water at room temperature – the standard temperature control for each of our products. After 24 hours submerged, we measure the percent weight gain of the plastic. Additionally, we also record the percent weight gain of the plastic at complete saturation when it cannot absorb any more water, regardless of time elapsed.
Get in touch with our specialist teams by filling in the contact form. We’re ready to meet your next challenge.
Contact us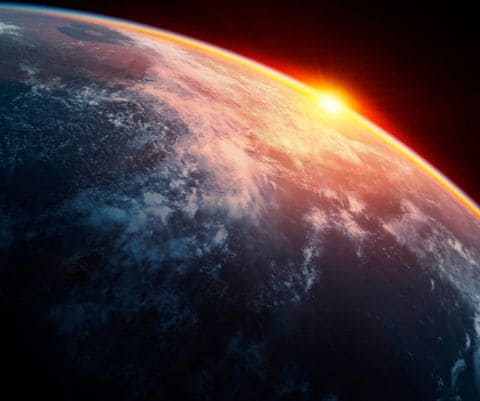