Simplify manufacturing with injection-molded parts
Access our leading portfolio of composite and plastic injection molding materials, end-to-end mold design support, and state-of-the-art prototyping and testing technologies.
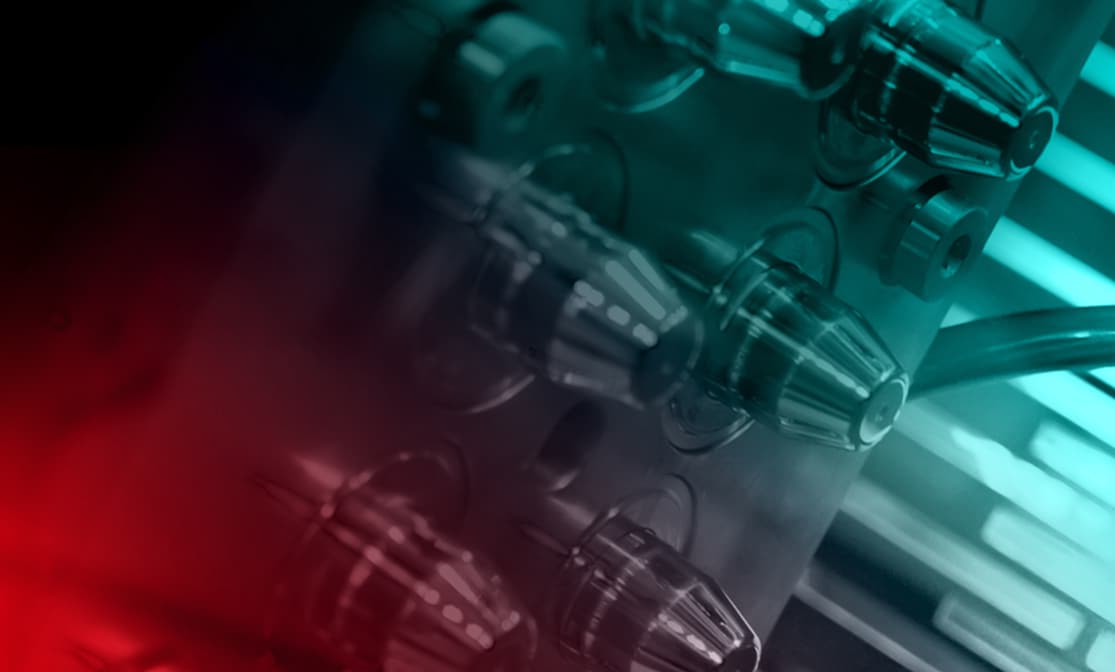
From automotive to medical to electronics applications, the Advanced Materials division of Mitsubishi Chemical Group designs, tests, and produces injection-molded components for use in function-critical systems.
Injection molded components interface with the rest of the end-product in complex ways. Not only must they fulfill high performance and functionality standards, but they also have a strong influence on user perception.
Since the inception of our injection molding program in 1933, the Mitsubishi Chemical Group has continuously developed our technologies, knowledge, and capabilities in this field to produce injection-molded parts that deliver unmatched performance and cost-savings to customers.
Our injection molding services revolve around:
- Our extensive portfolio of injection molding materials
- Mold expertise and design support
- State-of-the-art prototyping and testing
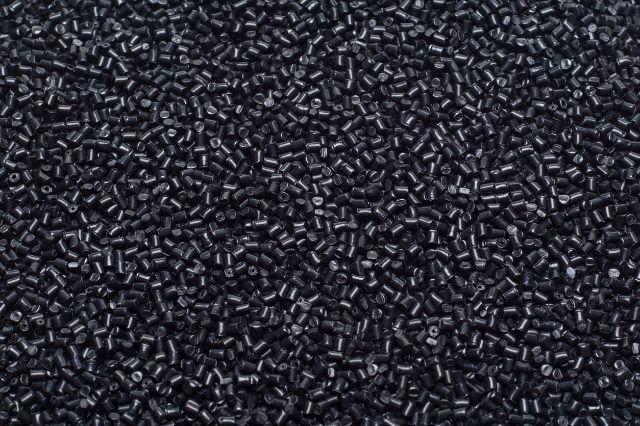
Injection-moldable materials
Our technical services teams work closely with customers to develop an insider understanding of their part performance and budget specifications, helping them to choose the optimal injection-moldable plastic or composite from our comprehensive portfolio.
Where many engineering plastics on the market are only available in stock shapes, our extensive product offering enables injection molding for the majority of our portfolio of engineering materials. These include our general engineering plastics (PA, PP, POM) as well as our Ertalyte™ PET-P and Techtron™ PPS materials. For especially demanding applications requiring extreme mechanical strength, this offering extends to our suite of advanced composites and thermoplastics, including KyronMAX™ carbon fiber composites, Duratron™ PAI and PEI, and Ketron™ PEEK.
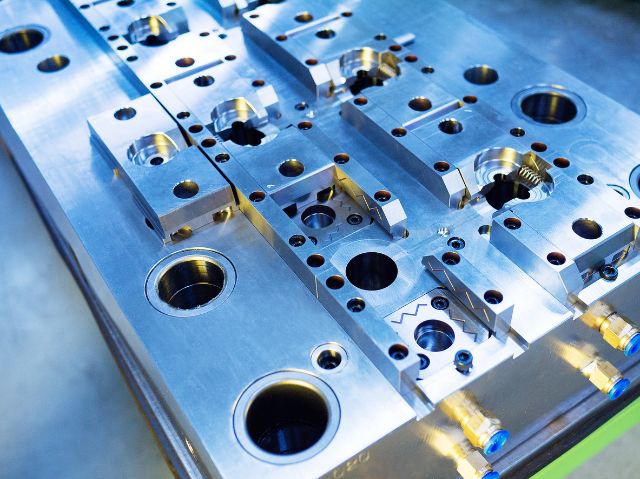
Design support from part to mold
We are an end-to-end partner in the production of injection-molded plastic components, providing expert support part design and mold design. Our design support services leverage a number of specialized technologies, including design for manufacturing (DFM), design for assembly (DFA), design for disassembly (DFD), as well as a range of computer-aided design tools.
The productivity and service-life of a molded part has a direct correlation to the quality of the tools employed. Our high-quality, in-house mold-making capabilities boost production efficiency and ensure a seamless translation of design specs into molded parts. Our skilled engineers employ state-of-the-art mold making equipment to develop a range of high-quality tools, including multi-cavity molds, hot-runners, insert- and overmolding systems, improving part longevity while also reducing time-to-market.
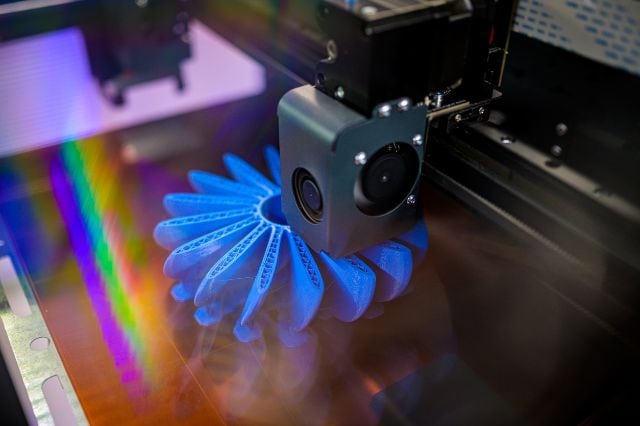
Smart tooling & prototyping solutions
Our flexible SPRINT (Soluble Printed Injection Tooling) solutions allow us to develop functional injection-molded prototypes in a matter of days. These SPRINT prototypes exhibit high precision and quality, simplifying testing and reducing both the cost and lead time of mold-making. Additionally, Mitsubishi Chemical Group is the purveyor of a range of master tools in which the forming inserts can be replaced. This enables us to prototype different parts in the same mold housing, significantly reducing tooling costs and lead times, and even making it possible to cost-effectively produce small series injection-molded parts.
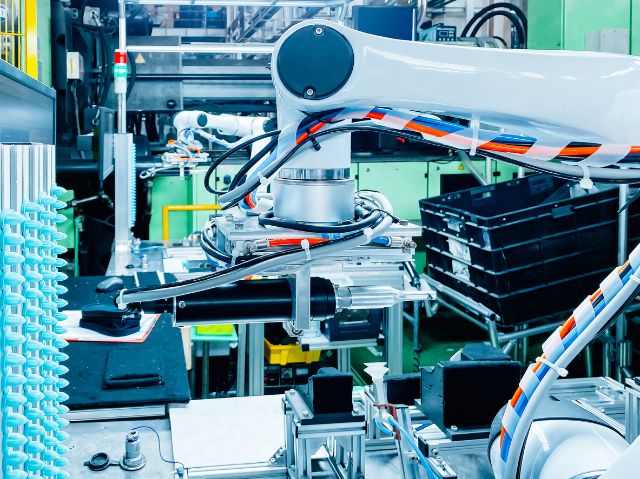
Automated injection molding
To enable cost-efficiency and the highest quality for our customers, Mitsubishi Chemical Group integrates a high level of automation into our injection molding processes. This automation, implemented primarily in assembly, quality assurance, and packaging, eliminates human errors and enables consistency that leads to “zero defects.” Upstream, automation is also applied to resin material handling and other post-molding operations like packaging and transporting final goods.
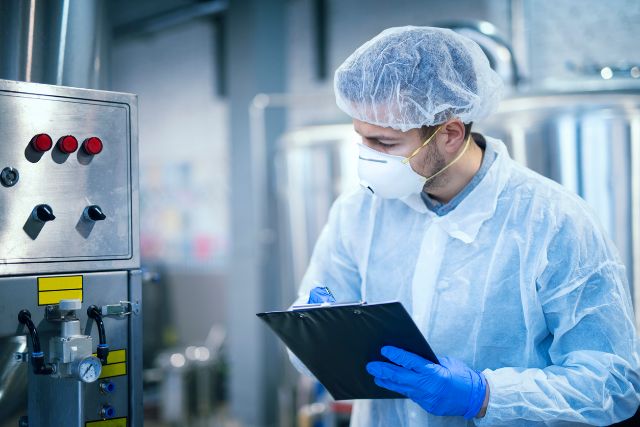
Clean room injection molding
As part of our state-of-the-art manufacturing facilities, Mitsubishi Chemical Group operates a 600m2 certified Class 100,000 (ISO 8) cleanroom. This enables the company to comply with the highest industrial standards current in medical technology and other industries where compliance stringent hygiene requirements is essential.
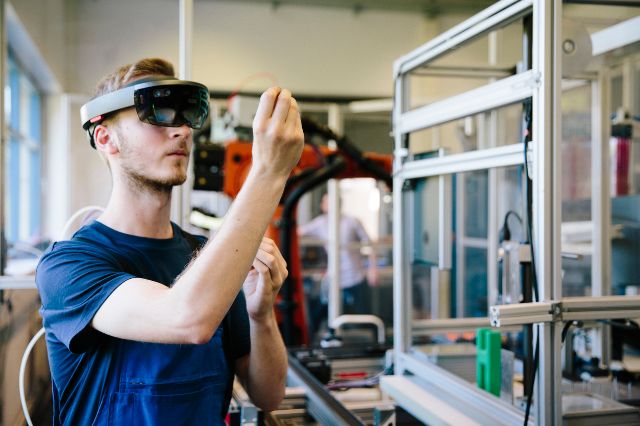
2K and 3K molding
Our manufacturing process consists of the latest injection molding technologies. Techniques include multi-component molding, bi-injection, and retractable and transfer molding for integral or split moldings, which helps reduce the time and cost of product assembly. We have dedicated two- and three-K (component) molding capabilities at our sites in both Tielt (Belgium) and Budapest (Hungary).
Injection-molded parts across industries
Medical
Production of plastic instruments and devices for hospitals, physicians, medical labs, and research facilities around the globe must follow stringent quality and hygienic requirements. To meet these, our product development relies on our technical expertise, state-of-the-art manufacturing facilities, detailed regulatory knowledge, and a high degree of automation. Medical components we manufacture include injection-molded optical parts, disposable products, home diagnostics, general health-care products, and more. Clean room injection molding is also available.
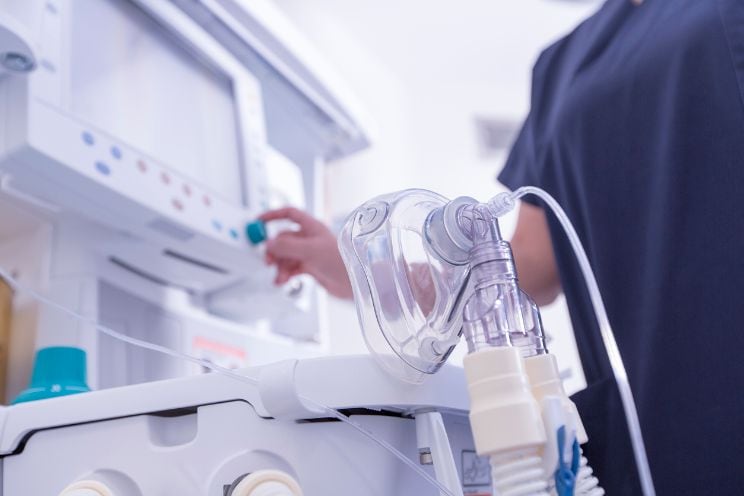
Automotive
Mitsubishi Chemical Group develops components for several leading international suppliers in the automotive industry, with product development, production, and assembly aligned in a single, vertically-integrated source. Our high-precision, injection-molded parts ensure safety for electrical, under-the-bonnet, and interior applications.
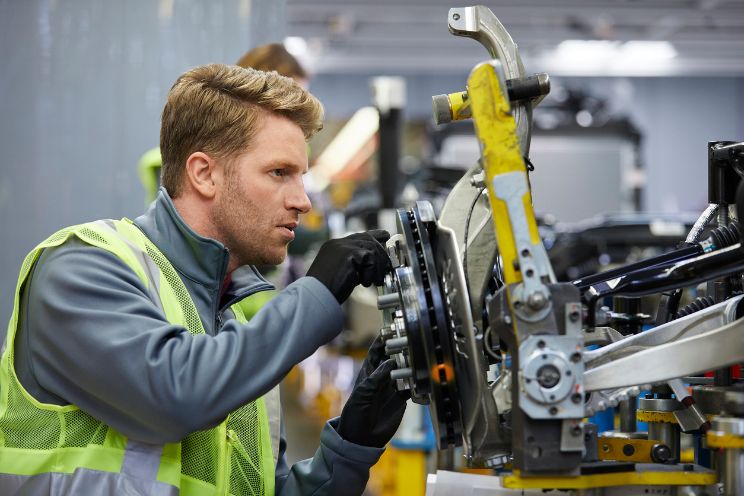
Electrical & electronics
Our expertise for simultaneously developing the product and the mold makes us an ideal partner for the design and manufacture of plastic components and systems for the electronics market, which continuously demands increased exterior aesthetics alongside increased internal sophistication. Our focus in these applications includes technical housings, frames and supports, and electromagnetic components.
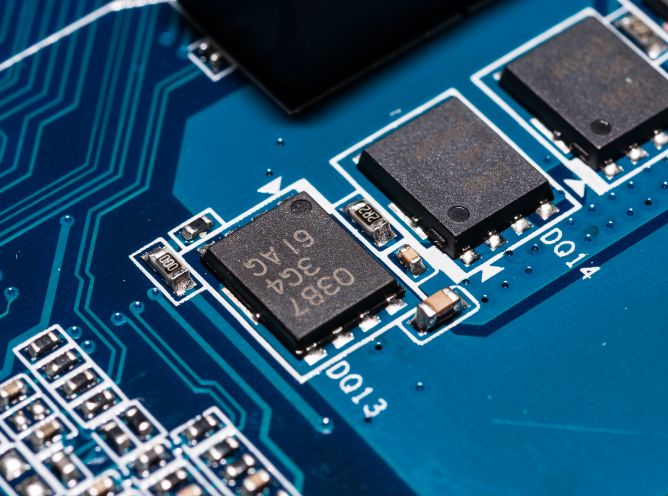
Industrial
Mitsubishi Chemical Group has extensive expertise in product design and years of experience developing our broad portfolio of engineering and high-performance plastics. In industrial applications, our advanced thermoplastic components meet the highest performance standards, with reliable load-bearing capacity, high temperature resistance, and other critical properties
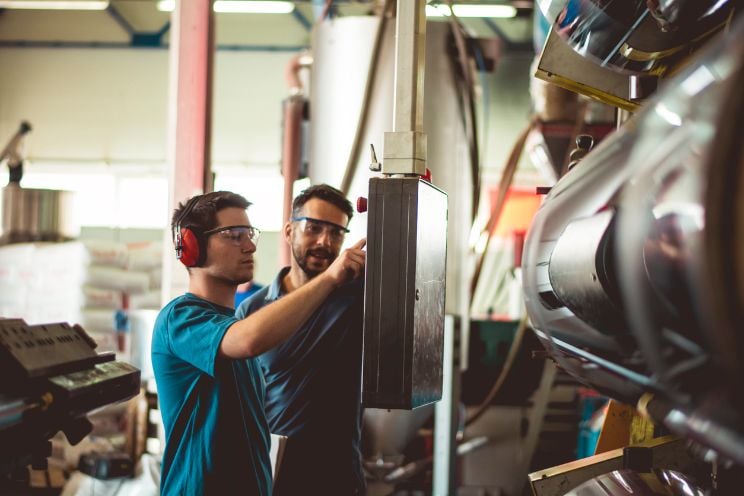
Functional packaging
Mitsubishi Chemical Group provides large engineering support activities for companies active in Beverage, Personal, and Home Care. We are a collaborative partner, not just responding to our customers’ immediate needs, but helping to develop innovative and tailored solutions across a product range, enabling long-term value.
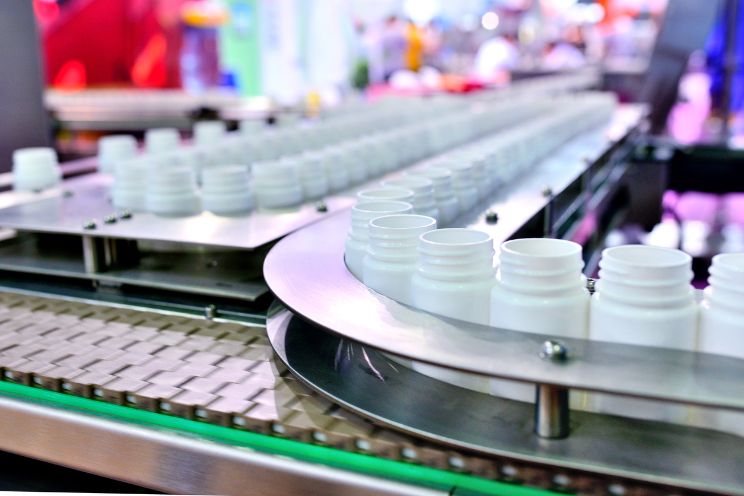
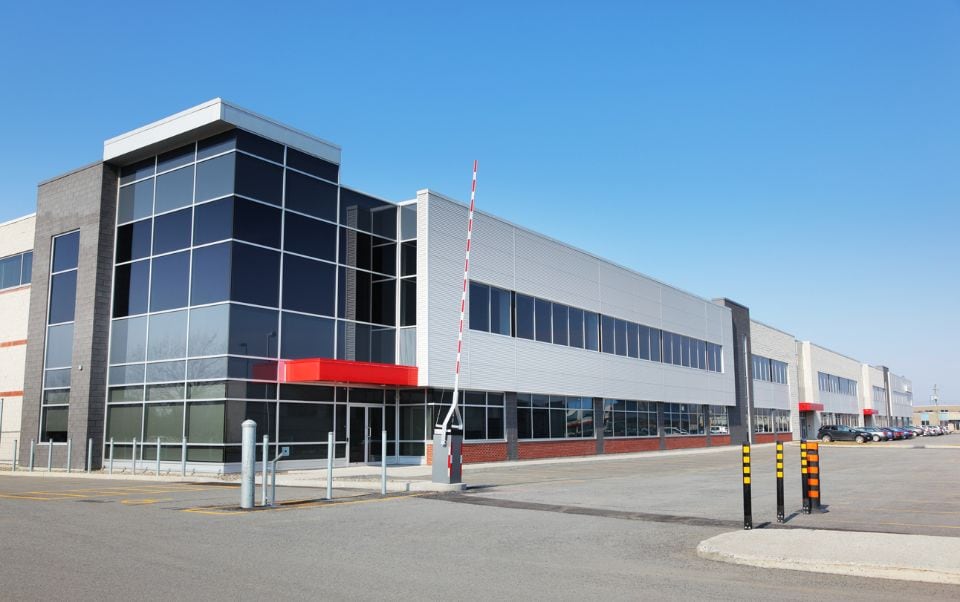
Mitsubishi Chemical Group operates across two primary locations for our injection molding services, both capable of fully automated assembly for maximum quality and consistency. Our state-of-the-art equipment includes injection molding machines with clamping forces ranging from 30 to 800 metric tons, including several 2- and 3-component molding machines. These facilities also offer fast repair, service, and modification of tools on-site, ensuring ongoing availability of molds for production.
Tielt, Belgium (16,600 m2 - approx. 168,000 ft2)
This production facility specializes in CAD, mold-making, tool repair and maintenance, prototyping, injection-molding, testing, secondary operations (assembly, printing, painting and sterilizing), logistics, and shipping, as well as in-house tool development.
Szigetszentmiklós (Budapest), Hungary (6,600 m2 - approx. 71,000 ft2)
Services at this production facility encompass injection-molding, tool repair and maintenance, testing, secondary operations, conditioning, logistics, and shipping.
Injection-molded components are critical in nature, demanding close collaboration between the manufacturer and supplier. As an end-to-end, vertically integrated partner, Mitsubishi Chemical Group provides early integration of the development and production processes, including design support and material selection guidance. Our injection molding services deliver leading components across industries, including automotive, medical, and electrical & electronics applications.
Get in touch with our specialist teams by filling in the contact form. We’re ready to meet your next challenge.
Contact us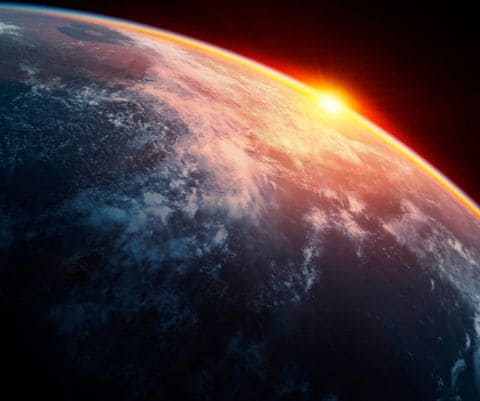