Leitfaden für die Bearbeitung von Kunststoffteilen
Wie werden Kunststoffe bearbeitet und was ist dabei für Hochleistungs-Thermoplaste zu beachten? Dieser Leitfaden behandelt die gängigsten Bearbeitungsmethoden und enthält nützliche Tipps und Daten für die Arbeit mit technischen Polymeren der Mitsubishi Chemical Group.
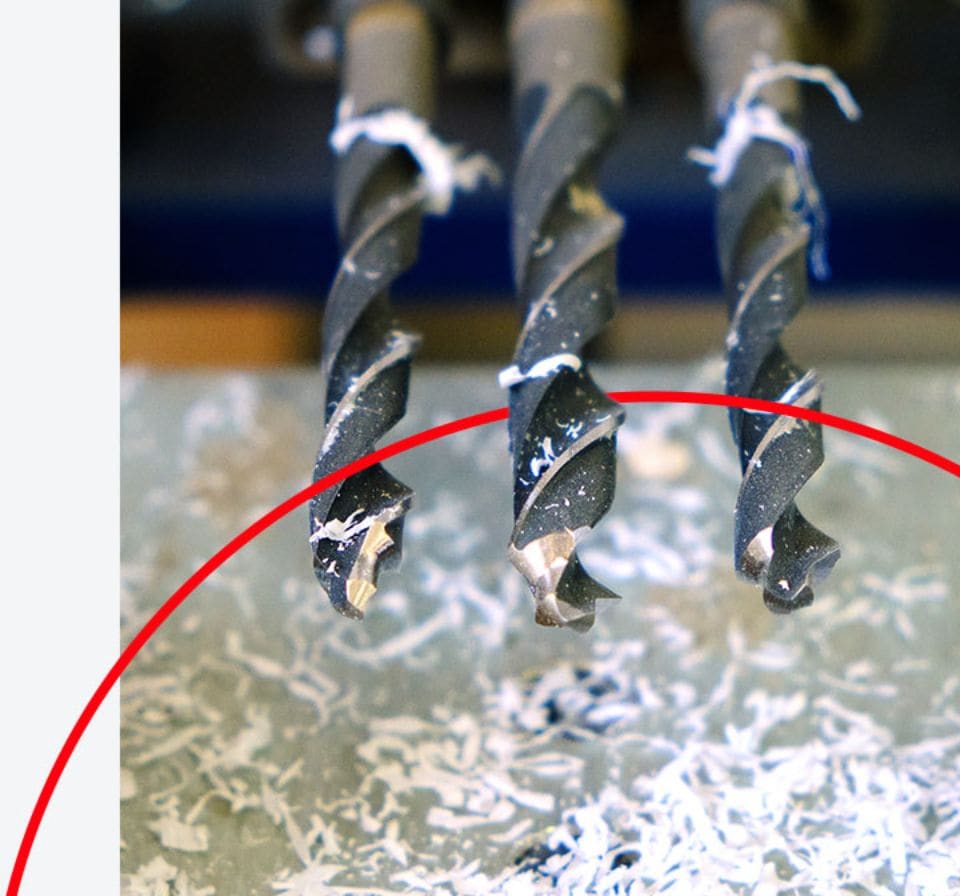
Aufgrund ihres Gewichtes, ihrer mechanischen und ihrer chemischen Eigenschaften ersetzen Kunststoffe zunehmend Metalle in vielen technischen Anwendungen. Viele der maschinellen Bearbeitungsmethoden, die für die Herstellung von Metallteilen verwendet werden, kommen auch bei Kunststoffen zum Einsatz. Die bewährten Verfahren für die Bearbeitung von Kunststoffen unterscheiden sich jedoch erheblich.
Kunststoffe weisen eine Reihe von Eigenschaften auf, die sich auf die maschinellen Bearbeitungsprozesse auswirken. Hierzu gehören:
- Die Wärmeausdehnung von Kunststoffen ist bis zu 10 Mal größer als die von Metallen.
- Kunststoffe verlieren Wärme langsamer als Metalle, wodurch das Risiko einer lokalen Überhitzung erhöht wird.
- Die Erweichungs- und Schmelztemperaturen von Kunststoffen sind viel niedriger als die von Metallen.
- Kunststoffe sind viel elastischer als Metalle.
Von der Materialwahl bis zum richtigen Werkzeug, von Maschinenparametern bis zu Befestigungsstechniken müssen Teilehersteller eine Reihe von Faktoren beachten, um gute Ergebnisse bei der Bearbeitung von Kunststoffen zu erzielen. Die folgenden Richtlinien behandeln die gängigsten Methoden der Kunststoffbearbeitung und bieten nützliche Tipps und Daten für die Arbeit mit technischen Polymeren der Mitsubishi Chemical Group.
Lesen Sie die nachstehende Übersicht oder laden Sie unser E-Book „Toolkit für Maschinenbediener“ herunter, einen vollständigen Fertigungsleitfaden mit empfohlenen Drehzahlen und Werkzeugen für eine Reihe von Werkstoffen der Mitsubishi Chemical Group.
Gängige Verfahren für die Kunststoffbearbeitung
-
Dieser Abschnitt behandelt die gängigsten Verfahren zur Bearbeitung von Kunststoffbauteilen und bietet Tipps und Richtlinien für bestmögliche Ergebnisse.
Die richtige Bearbeitung ist entscheidend für Qualität und Maßhaltigkeit. Eine nicht ordnungsgemäße Bearbeitung kann zu Spannungen im fertigen Teil führen, die sich negativ auf die mechanischen Eigenschaften auswirken und ein vorzeitiges Versagen des Teils zur Folge haben können.
Häufige Ursachen für maschinell erzeugte Spannungen sind:
• Verwendung stumpfer oder ungeeigneter Werkzeuge
• Übermäßige Wärmeentwicklung durch ungeeignete Drehzahlen und Vorschub-Geschwindigkeiten
• Abtragen großer Materialmengen, in der Regel von einer Seite des Halbzeugs -
Was ist Gewindeschneiden? Was ist Gewindebohren?
Gewindeschneiden und -bohren sind zwei Möglichkeiten für die Herstellung von Gewinden. Beim Gewindeschneiden wird ein Gewindeschneider verwendet, um ein Außengewinde zu schneiden, während beim Gewindebohren ein Gewindebohrer verwendet wird, um ein Gewinde im Inneren einer Bohrung zu erzeugen.
Gewindeschneiden und Gewindebohren mit Kunststoff vs. Metall
Beim Gewindeschneiden und Gewindebohren von Kunststoffen ist vor allem zu beachten, dass Kunststoffe kerbempfindlicher als Metalle sind. Einige polymere Materialien können während des Gewindeschneidens reißen, insbesondere bei Verfahren mit geringer Gewindesteigung.
Tipps zum Schneiden von Kunststoffgewinden
Das Gewindeschneiden von Kunststoff sollte mit einem Hartmetalleinsatz in einem einzigen Durchgang erfolgen, wobei am Ende vier bis fünf Durchgänge von 0,03 mm erforderlich sind. Die Verwendung von Kühlmittel wird empfohlen.
Tipps zum Bohren von Kunststoffgewinden
Verwenden Sie beim Gewindebohren von Kunststoffen den angegebenen Bohraufsatz mit einem zweischneidigen Gewindebohrer. Halten Sie den Gewindeschneider frei von Ablagerungen. Die Verwendung eines Kühlmittels während des Gewindebohrens wird ebenfalls empfohlen.
-
Was ist Fräsen?
Fräsen ist ein Verfahren, bei dem ein Schneidwerkzeug in Hochgeschwindigkeits eine fixierte Kunststoffform spanend bearbeitet. Der rotierende Fräser bewegt sich auf einer Achse, um von dem Halbzeug gleichmäßig Material in verschiedene Richtungen abzutragen. Das CNC-Fräsen (Computerized Numerical Control) verbessert die Genauigkeit und Effizienz des Kunststofffräsens.
Fräsen von Kunststoff vs. Metall
Beim Kunststofffräsen ist es entscheidend, das Bauteil richtig auf dem Werktisch zu fixieren und Vibrationen des rotierenden Schneidwerkzeugs zu minimieren. Diese können ansonsten zu Rattermarken und Ungenauigkeit durch Formabweichungen führen.
Tipps zum Kunststofffräsen
- Das Gleichlauffräsen, auch Abwärtsfräsen genannt, ist dem konventionellen Fräsen vorzuziehen.
- Ausreichende Spannvorrichtungen am Fräsbett ermöglichen schnelle Tischbewegungen und hohe Spindeldrehzahlen.
- Die Form sollte jedoch nicht zu fest fixiert werden, da sie sich sonst verformen oder federn kann.
- Verwenden Sie beim Planfräsen Fräskörper mit positiver Geometrie.
-
Was ist Sägen?
Das Sägen ist eine Bearbeitungsmethode, bei der ein Material mit einer Bandsäge, einer Tischsäge oder einer anderen Spezialausrüstung in mehrere Stücke geschnitten wird.
Sägen von Kunststoff vs. Metall
Der Hauptunterschied zwischen dem Sägen von Kunststoff und Metall besteht darin, dass sich die vom Sägeblatt erzeugte Hitze aufgrund der niedrigeren Erweichungs- und Schmelztemperaturen negativ auf die Kunststoffteile auswirken kann. Beim Sägen von Kunststoffen müssen die Geschwindigkeit des Sägeblatts, die thermischen Eigenschaften des Materials und die Dicke der Form berücksichtigt werden.
Tipps zur Auswahl eines Sägewerkzeugs
- Bandsägen sind vielseitig und eignen sich gut für gerade, kontinuierliche Kurven und unregelmäßige Schnitte.
- Tischsägen eignen sich für gerade Schnitte und können zum Schneiden mehrerer Dicken und dickerer Querschnitte verwendet werden – bei entsprechender Leistung bis zu 101,6 mm.
Tipps für die Auswahl eines Sägeblatts
- Für allgemeine Sägearbeiten eignen sich am besten Spalt- und Kombinationsblätter mit einer Zahnteilung von 0° und einer Schränkung von 3° bis 10°, um die Reibungswärme zu reduzieren.
- Hohlgeschliffene Kreissägeblätter ohne Schränkung ermöglichen glatte Schnitte bis zu einer Stärke von 19,05 mm.
- Sägeblätter aus Wolframkarbid sind verschleißfest und bieten eine optimale Oberflächengüte.
-
Was ist Bohren? Was ist Aufbohren?
Bohren ist ein Bearbeitungsverfahren, bei dem zylindrische Löcher und Durchgangslöcher mit Hilfe eines spitzen, schraubenförmigen Werkzeugs hergestellt werden. Aufbohren ist ein sekundäres Verfahren zur Vergrößerung oder Fertigstellung von Bohrlöchern.
Bohren und Ausbohren von Kunststoff vs. Metall
Die wärmeisolierenden Eigenschaften von Kunststoffen müssen beim Bohren berücksichtigt werden, insbesondere wenn die Tiefe des Lochs mehr als das Doppelte seines Durchmessers beträgt. Eine übermäßige Wärmeentwicklung kann zu Abplatzungen, rauen Oberflächen und unzureichenden Toleranzen führen.
Bohrtipps für KunststoffFür Löcher mit kleinem Durchmesser (0,794 mm bis 25,4 mm)
- Spiralbohrer aus Hochgeschwindigkeitsstahl sind im Allgemeinen ausreichend.
- Häufiges Herausziehen (Tieflochbohren) wird empfohlen, um die Späneabfuhr zu verbessern.
- Ein Bohrer mit langsamer Spirale (niedrige Helix) ermöglicht eine bessere Späneabfuhr.
Für Löcher mit großem Durchmesser (254 mm und größer)
- Empfohlen wird ein langsamer Spiralbohrer (niedrige Spirale) oder ein Universalbohrer mit einem Spitzenwinkel von 118° und einem Lippenspiel von 9° bis 15°. Die Lippenschränkung sollte abgeschliffen (überspielt) und der Steg verschmälert werden.
- Vermeiden Sie Handvorschub – das Greifen des Bohrers kann zu Mikrorissen führen.
- Im Allgemeinen ist es am besten ein Pilotloch (maximal 127 mm Durchmesser) mit 600 bis 1.000 U/min und einem positiven Vorschub von 0127 mm bis 04 mm pro Umdrehung zu bohren.
- Das Nachbohren bei 400 bis 500 U/min mit 0025 mm bis 05 mm pro Umdrehung ist erforderlich um das Loch auf größere Durchmesser zu erweitern.
Für besonders kerbempfindliche Materialien (wie Ertalyte® PET-P und glasfaserverstärkte Materialien)
- Ein zweistufiger Prozess der sowohl das Bohren als auch das Aufbohren umfasst minimiert den Hitzestau und verringert das Risiko von Rissen.
- Bohren Sie zunächst ein Loch mit einem Durchmesser von 25 4 mm mit einem Einsatzbohrer bei 500 bis 800 U/min und einem Vorschub von 0 127 mm bis 0 4 mm pro Umdrehung.
- Als Nächstes bohren Sie das Loch mit einem Bohrstab mit Hartmetalleinsatz mit einem Radius von 0 4 mm bis 0 8 mm bei 500 bis 1.000 Umdrehungen pro Minute und einem Vorschub von 0 127 mm bis 0 5 mm pro Umdrehung auf die endgültigen Abmessungen.
-
Was ist Drehen?
Drehen ist ein Bearbeitungsverfahren, bei dem eine plastische Form um eine feststehende Drehbank gedreht wird. Das Drehen eignet sich besonders für die Bearbeitung von Teilen, die entlang einer gemeinsamen Rotationsachse symmetrisch sind.
Drehen von Kunststoff vs. Metall
Wie bei anderen Kunststoffbearbeitungsverfahren entsteht auch beim Drehen Wärme. Um die Beschädigung eines Kunststoffteils zu vermeiden, sollten die Drehzahl, die Auswahl des Werkzeugs und der Kühlmittel sowie die thermischen Eigenschaften des Materials sorgfältig berücksichtigt werden.
Tipps zum Drehen von Kunststoffen
- Drehbearbeitungen erfordern Wendeplatten mit positiven Geometrien und geschliffenen Peripherien.
- Geschliffene Ränder und polierte Oberseiten verringern im Allgemeinen die Materialanhäufung auf der Wendeschneidplatte und verbessern die erreichbare Oberflächengüte.
- Ein feinkörniges C-2-Hartmetall wird häufig für Kunststoffdreharbeiten empfohlen.
Zusätzliche Behandlungen bei der Bearbeitung
-
Je nach Anforderungen an das Werkstück und den Bearbeitungsprozess können Kühlmittel und/oder Tempern das Endergebnis verbessern. Dieser Abschnitt befasst sich mit der Verwendung von Kühlmitteln und dem Tempern, wie sie bei der Bearbeitung von Kunststoffteilen eingesetzt werden.
-
Was sind Kühlmittel?
Kühlmittel reduzieren die Entstehung von lokaler Reibungswärme, verbessern so die Bearbeitungsergebnisse und verlängern die Lebensdauer des Werkzeugs. Bei der Bearbeitung von technischen Kunststoffen kommen in der Regel verschiedene Arten von Kühlmitteln zum Einsatz, wie beispielsweise Druckluft, Trockeneis, Sprühnebel und speziell entwickelte Kühlmittel.
Wann werden Kühlmittel empfohlen?Für die meisten Bearbeitungsverfahren von technischen Kunststoffen sind Kühlmittel nicht erforderlich. Wir empfehlen jedoch Kühlmittel in den folgenden Fällen:
- Beim Bohren oder Trennen von Kunststoffen – zwei Prozesse, die hohe Reibungswärme erzeugen.
- Bei der Bearbeitung von besonders kerbempfindlichen Werkstoffen, wie Ertalyte™ PET-P, Duratron™ PAI, Duratron™ PBI und glas- oder kohlefaserverstärkten Produkten.
- Wenn es darum geht, optimale Oberflächengüten und enge Toleranzen zu erreichen.
Tipps zur Auswahl eines Kühlmittels
- Sprühnebel und Druckluft sind sehr wirksame Mittel zur Kühlung der Schnittfläche.
- Allzweck-Schneidflüssigkeiten auf Erdölbasis sind zwar für viele Metalle und Kunststoffe geeignet, können aber bei amorphen Kunststoffen wie Altron™ PC, Sultron™ PSU, Sultron™ PPSU und Duratron™ U1000 PEI zu Spannungsrissen führen.
- Zwei für die meisten Kunststoffe geeignete Kühlmittelspülungen sind Trim E190 und Tim Sol LC SF.
-
Was ist Tempern?
Das Tempern ist ein Wärmebehandlungsverfahren, das die physikalischen Eigenschaften eines Kunststoffs verbessert, indem es zur leichteren Formbearbeitbarkeit seine Dehnbarkeit erhöht und seine Härte verringert. Durch das Tempern werden innere Spannungen im Kunststoff abgebaut, wodurch das bearbeitete Teil eine höhere Formbeständigkeit erhält. Beim Tempern wird ein Kunststoffteil über einen bestimmten Zeitraum auf die Hälfte seiner Schmelztemperatur erwärmt und dann mit einer bestimmten Geschwindigkeit abgekühlt.
Tempern vor der Bearbeitung
Viele Kunststoffhalbzeuge der Mitsubishi Chemical Group Advanced Materials Division werden in einem speziellen Spannungsabbauprogramm getempert. Dadurch werden die prozessbedingt entstandenen inneren Spannungen minimiert. Dadurch wird sichergestellt, dass das Material während und nach der Bearbeitung formstabil bleibt.
Tempern nach der Bearbeitung
Einige bearbeitete Kunststoffteile müssen nach der Bearbeitung getempert werden, um die Maß- oder Qualitätsanforderungen zu erfüllen. Das Nachtempern hat jedoch mehrere Vorteile:
- Verbesserte chemische Beständigkeit – PC-, PSU- und PEI-Materialien können durch Nachtempern unempfindlicher gegenüber Spannungsrissbildung werden.
- Bessere Ebenheit, engere Toleranzen– Teile mit extrem engen Toleranzen, die eine präzise Ebenheit und unsymmetrische Konturen erfordern, müssen manchmal zwischen den Bearbeitungsvorgängen getempert werden.
- PAI mit hoher Druckgeschwindigkeit und geringem Verschleiß– Extrudierte oder spritzgegossene-Duratron™ PAI-Teile, die hohe Druckgeschwindigkeiten oder einen möglichst geringen Verschleißfaktor erfordern, profitieren von einer zusätzlichen Aushärtung nach der Bearbeitung. Dieser Aushärtungsprozess optimiert die Verschleißeigenschaften. Nur PAI profitiert von einem solchen Zyklus.
Tipps zum Tempern von Kunststoffen- Eine bessere Ebenheit kann durch Schruppen, Tempern und Fertigbearbeitung mit einem sehr leichten Schnitt erreicht werden.
- Um das Potenzial für eingearbeitete Spannungen zu verringern, sollten Sie die Fertigungsrichtlinien für das jeweilige Material beachten. Wichtig: Die Richtlinien variieren je nach Materialtyp.
- Stellen Sie sicher, dass die Teile in der erforderlichen Form oder Ebenheit fixiert sind, um Verformungen zu vermeiden. Heben Sie die Fixierung erst auf, wenn die Teile den gesamten Zyklus durchlaufen haben und sich kühl anfühlen.
- Die Fertigbearbeitung auf engtolerierte Endmaße sollte nach dem Tempern erfolgen.
- Bei dünnen Querschnitten sind Änderungen der Aufheiz- und Haltezeit möglich.
Richtlinien zur Fehlerbehebung bei technischen Kunststoffen
-
- Gewindebohrung
- Nicht ordnungsgemäß geschärfter Bohrer
- Zu geringer Abstand
- Vorschub zu stark
- Verbrannte oder geschmolzene Oberfläche
- Falscher Bohrertyp
- Nicht ordnungsgemäß geschärfter Bohrer
- Vorschub zu gering
- Stumpfer Bohrer
- Steg zu dick
- Absplitternde Oberfläche
- Vorschub zu stark
- Zu großer Abstand
- Zu viel Schränkung (dünner Steg, wie beschrieben)
- Rattern
- Zu großer Abstand
- Vorschub zu gering
- Bohrerüberstand zu groß
- Zu viel Schränkung (dünner Steg, wie beschrieben)
- Vorschubspuren oder spiralförmige Linien am Innendurchmesser
- Vorschub zu stark
- Bohrer nicht zentriert
- Bohrergrund nicht zentriert
- Überdimensionierte Löcher
- Bohrergrund nicht zentriert
- Steg zu dick
- Zu geringer Abstand
- Vorschubgeschwindigkeit zu hoch
- Spitzenwinkel zu groß
- Unterdimensionierte Löcher
- Stumpfer Bohrer
- Zu großer Abstand
- Spitzenwinkel zu klein
- Löcher nicht konzentrisch
- Vorschub zu stark
- Spindeldrehzahl zu niedrig
- Bohrer dringt zu weit in das nächste Stück ein
- Abstechwerkzeug verlässt die Feder und lenkt den Bohrer ab
- Steg zu dick
- Drehzahl des Bohrers am Anfang zu hoch
- Bohrer nicht in der Mitte montiert
- Bohrer nicht richtig geschärft
- Grat an der Trennstelle
- Stumpfes Abstechwerkzeug
- Der Bohrer geht nicht vollständig durch das Werkstück
- Schnelles Abstumpfen des Bohrers
- Vorschub zu gering
- Spindeldrehzahl zu hoch
- Unzureichende Schmierung durch das Kühlmittel
- Gewindebohrung
-
- Geschmolzene Oberfläche
- Stumpfe oder reibende Kante
- Zu geringer Seitenabstand
- Vorschubgeschwindigkeit zu niedrig
- Spindeldrehzahl zu hoch
- Raue Oberfläche
- Vorschub zu stark
- Falsche Freiwinkel
- Scharfe Spitze am Werkzeug (leichter Nasenradius erforderlich)
- Werkzeug nicht in der Mitte montiert
- Grate an den Schnittkanten
- Keine Schräge an scharfen Ecken zugelassen
- Stumpfes Werkzeug
- Zu geringer Seitenabstand
- Der Anschnittwinkel ist am Werkzeug nicht vorgesehen (das Werkzeug sollte sich allmählich aus dem Schnitt lösen, nicht plötzlich)
- Risse oder Absplitterungen an den Ecken
- Zu viel positive Schränkung am Werkzeug
- Werkzeug wird nicht in den Schnitt geführt (schlägt plötzlich auf das Werkstück)
- Stumpfes Werkzeug
- Werkzeug unter der Mitte montiert
- Scharfe Spitze am Werkzeug (leichter Nasenradius erforderlich)
- Rattern
- Zu großer Spitzenradius am Werkzeug
- Werkzeug nicht fest montiert
- Material nicht richtig gestützt
- Schnittbreite zu groß (zwei Schnitte verwenden)
- Geschmolzene Oberfläche
-
- Geschmolzene Oberfläche
- Stumpfes Werkzeug
- Zu geringer Seitenabstand
- Unzureichende Kühlmittelzufuhr
- Raue Oberfläche
- Vorschub zu stark
- Werkzeug unsachgemäß geschärft
- Schneide nicht geschliffen
- Spiralförmige Markierungen
- Werkzeug reibt beim Rückzug
- Grat an der Spitze des Werkzeugs
- Konkave oder konvexe Oberflächen
- Spitzenwinkel zu groß
- Werkzeug nicht rechtwinklig zur Spindel
- Werkzeugablenkung
- Vorschub zu stark
- Werkzeug von oben oder unten mittig montiert
- Federn oder Grate an der Trennstelle
- Spitzenwinkel nicht groß genug
- Stumpfes Werkzeug
- Vorschub zu stark
- Grate am Außendurchmesser
- Keine Kammer vor Abstichdurchmesser
- Stumpfes Werkzeug
- Geschmolzene Oberfläche
Laden Sie das komplette Toolkit für Maschinenbediener herunter
-
Empfohlene Drehzahlen, Werkzeuge und vieles mehr
Weitere Informationen über unsere thermoplastischen Produkte Laden Sie unser „Toolkit für Maschinenbediener“ herunter, ein vollständiger Fertigungsleitfaden mit empfohlenen Drehzahlen und Werkzeugen für eine Reihe von Werkstoffen der Mitsubishi Chemical Group.
-
Gängige Verfahren für die Kunststoffbearbeitung
-
Dieser Abschnitt behandelt die gängigsten Verfahren zur Bearbeitung von Kunststoffbauteilen und bietet Tipps und Richtlinien für bestmögliche Ergebnisse.
Die richtige Bearbeitung ist entscheidend für Qualität und Maßhaltigkeit. Eine nicht ordnungsgemäße Bearbeitung kann zu Spannungen im fertigen Teil führen, die sich negativ auf die mechanischen Eigenschaften auswirken und ein vorzeitiges Versagen des Teils zur Folge haben können.
Häufige Ursachen für maschinell erzeugte Spannungen sind:
• Verwendung stumpfer oder ungeeigneter Werkzeuge
• Übermäßige Wärmeentwicklung durch ungeeignete Drehzahlen und Vorschub-Geschwindigkeiten
• Abtragen großer Materialmengen, in der Regel von einer Seite des Halbzeugs -
Was ist Gewindeschneiden? Was ist Gewindebohren?
Gewindeschneiden und -bohren sind zwei Möglichkeiten für die Herstellung von Gewinden. Beim Gewindeschneiden wird ein Gewindeschneider verwendet, um ein Außengewinde zu schneiden, während beim Gewindebohren ein Gewindebohrer verwendet wird, um ein Gewinde im Inneren einer Bohrung zu erzeugen.
Gewindeschneiden und Gewindebohren mit Kunststoff vs. Metall
Beim Gewindeschneiden und Gewindebohren von Kunststoffen ist vor allem zu beachten, dass Kunststoffe kerbempfindlicher als Metalle sind. Einige polymere Materialien können während des Gewindeschneidens reißen, insbesondere bei Verfahren mit geringer Gewindesteigung.
Tipps zum Schneiden von Kunststoffgewinden
Das Gewindeschneiden von Kunststoff sollte mit einem Hartmetalleinsatz in einem einzigen Durchgang erfolgen, wobei am Ende vier bis fünf Durchgänge von 0,03 mm erforderlich sind. Die Verwendung von Kühlmittel wird empfohlen.
Tipps zum Bohren von Kunststoffgewinden
Verwenden Sie beim Gewindebohren von Kunststoffen den angegebenen Bohraufsatz mit einem zweischneidigen Gewindebohrer. Halten Sie den Gewindeschneider frei von Ablagerungen. Die Verwendung eines Kühlmittels während des Gewindebohrens wird ebenfalls empfohlen.
-
Was ist Fräsen?
Fräsen ist ein Verfahren, bei dem ein Schneidwerkzeug in Hochgeschwindigkeits eine fixierte Kunststoffform spanend bearbeitet. Der rotierende Fräser bewegt sich auf einer Achse, um von dem Halbzeug gleichmäßig Material in verschiedene Richtungen abzutragen. Das CNC-Fräsen (Computerized Numerical Control) verbessert die Genauigkeit und Effizienz des Kunststofffräsens.
Fräsen von Kunststoff vs. Metall
Beim Kunststofffräsen ist es entscheidend, das Bauteil richtig auf dem Werktisch zu fixieren und Vibrationen des rotierenden Schneidwerkzeugs zu minimieren. Diese können ansonsten zu Rattermarken und Ungenauigkeit durch Formabweichungen führen.
Tipps zum Kunststofffräsen
- Das Gleichlauffräsen, auch Abwärtsfräsen genannt, ist dem konventionellen Fräsen vorzuziehen.
- Ausreichende Spannvorrichtungen am Fräsbett ermöglichen schnelle Tischbewegungen und hohe Spindeldrehzahlen.
- Die Form sollte jedoch nicht zu fest fixiert werden, da sie sich sonst verformen oder federn kann.
- Verwenden Sie beim Planfräsen Fräskörper mit positiver Geometrie.
-
Was ist Sägen?
Das Sägen ist eine Bearbeitungsmethode, bei der ein Material mit einer Bandsäge, einer Tischsäge oder einer anderen Spezialausrüstung in mehrere Stücke geschnitten wird.
Sägen von Kunststoff vs. Metall
Der Hauptunterschied zwischen dem Sägen von Kunststoff und Metall besteht darin, dass sich die vom Sägeblatt erzeugte Hitze aufgrund der niedrigeren Erweichungs- und Schmelztemperaturen negativ auf die Kunststoffteile auswirken kann. Beim Sägen von Kunststoffen müssen die Geschwindigkeit des Sägeblatts, die thermischen Eigenschaften des Materials und die Dicke der Form berücksichtigt werden.
Tipps zur Auswahl eines Sägewerkzeugs
- Bandsägen sind vielseitig und eignen sich gut für gerade, kontinuierliche Kurven und unregelmäßige Schnitte.
- Tischsägen eignen sich für gerade Schnitte und können zum Schneiden mehrerer Dicken und dickerer Querschnitte verwendet werden – bei entsprechender Leistung bis zu 101,6 mm.
Tipps für die Auswahl eines Sägeblatts
- Für allgemeine Sägearbeiten eignen sich am besten Spalt- und Kombinationsblätter mit einer Zahnteilung von 0° und einer Schränkung von 3° bis 10°, um die Reibungswärme zu reduzieren.
- Hohlgeschliffene Kreissägeblätter ohne Schränkung ermöglichen glatte Schnitte bis zu einer Stärke von 19,05 mm.
- Sägeblätter aus Wolframkarbid sind verschleißfest und bieten eine optimale Oberflächengüte.
-
Was ist Bohren? Was ist Aufbohren?
Bohren ist ein Bearbeitungsverfahren, bei dem zylindrische Löcher und Durchgangslöcher mit Hilfe eines spitzen, schraubenförmigen Werkzeugs hergestellt werden. Aufbohren ist ein sekundäres Verfahren zur Vergrößerung oder Fertigstellung von Bohrlöchern.
Bohren und Ausbohren von Kunststoff vs. Metall
Die wärmeisolierenden Eigenschaften von Kunststoffen müssen beim Bohren berücksichtigt werden, insbesondere wenn die Tiefe des Lochs mehr als das Doppelte seines Durchmessers beträgt. Eine übermäßige Wärmeentwicklung kann zu Abplatzungen, rauen Oberflächen und unzureichenden Toleranzen führen.
Bohrtipps für KunststoffFür Löcher mit kleinem Durchmesser (0,794 mm bis 25,4 mm)
- Spiralbohrer aus Hochgeschwindigkeitsstahl sind im Allgemeinen ausreichend.
- Häufiges Herausziehen (Tieflochbohren) wird empfohlen, um die Späneabfuhr zu verbessern.
- Ein Bohrer mit langsamer Spirale (niedrige Helix) ermöglicht eine bessere Späneabfuhr.
Für Löcher mit großem Durchmesser (254 mm und größer)
- Empfohlen wird ein langsamer Spiralbohrer (niedrige Spirale) oder ein Universalbohrer mit einem Spitzenwinkel von 118° und einem Lippenspiel von 9° bis 15°. Die Lippenschränkung sollte abgeschliffen (überspielt) und der Steg verschmälert werden.
- Vermeiden Sie Handvorschub – das Greifen des Bohrers kann zu Mikrorissen führen.
- Im Allgemeinen ist es am besten ein Pilotloch (maximal 127 mm Durchmesser) mit 600 bis 1.000 U/min und einem positiven Vorschub von 0127 mm bis 04 mm pro Umdrehung zu bohren.
- Das Nachbohren bei 400 bis 500 U/min mit 0025 mm bis 05 mm pro Umdrehung ist erforderlich um das Loch auf größere Durchmesser zu erweitern.
Für besonders kerbempfindliche Materialien (wie Ertalyte® PET-P und glasfaserverstärkte Materialien)
- Ein zweistufiger Prozess der sowohl das Bohren als auch das Aufbohren umfasst minimiert den Hitzestau und verringert das Risiko von Rissen.
- Bohren Sie zunächst ein Loch mit einem Durchmesser von 25 4 mm mit einem Einsatzbohrer bei 500 bis 800 U/min und einem Vorschub von 0 127 mm bis 0 4 mm pro Umdrehung.
- Als Nächstes bohren Sie das Loch mit einem Bohrstab mit Hartmetalleinsatz mit einem Radius von 0 4 mm bis 0 8 mm bei 500 bis 1.000 Umdrehungen pro Minute und einem Vorschub von 0 127 mm bis 0 5 mm pro Umdrehung auf die endgültigen Abmessungen.
-
Was ist Drehen?
Drehen ist ein Bearbeitungsverfahren, bei dem eine plastische Form um eine feststehende Drehbank gedreht wird. Das Drehen eignet sich besonders für die Bearbeitung von Teilen, die entlang einer gemeinsamen Rotationsachse symmetrisch sind.
Drehen von Kunststoff vs. Metall
Wie bei anderen Kunststoffbearbeitungsverfahren entsteht auch beim Drehen Wärme. Um die Beschädigung eines Kunststoffteils zu vermeiden, sollten die Drehzahl, die Auswahl des Werkzeugs und der Kühlmittel sowie die thermischen Eigenschaften des Materials sorgfältig berücksichtigt werden.
Tipps zum Drehen von Kunststoffen
- Drehbearbeitungen erfordern Wendeplatten mit positiven Geometrien und geschliffenen Peripherien.
- Geschliffene Ränder und polierte Oberseiten verringern im Allgemeinen die Materialanhäufung auf der Wendeschneidplatte und verbessern die erreichbare Oberflächengüte.
- Ein feinkörniges C-2-Hartmetall wird häufig für Kunststoffdreharbeiten empfohlen.
-
-
Zusätzliche Behandlungen bei der Bearbeitung
-
Je nach Anforderungen an das Werkstück und den Bearbeitungsprozess können Kühlmittel und/oder Tempern das Endergebnis verbessern. Dieser Abschnitt befasst sich mit der Verwendung von Kühlmitteln und dem Tempern, wie sie bei der Bearbeitung von Kunststoffteilen eingesetzt werden.
-
Was sind Kühlmittel?
Kühlmittel reduzieren die Entstehung von lokaler Reibungswärme, verbessern so die Bearbeitungsergebnisse und verlängern die Lebensdauer des Werkzeugs. Bei der Bearbeitung von technischen Kunststoffen kommen in der Regel verschiedene Arten von Kühlmitteln zum Einsatz, wie beispielsweise Druckluft, Trockeneis, Sprühnebel und speziell entwickelte Kühlmittel.
Wann werden Kühlmittel empfohlen?Für die meisten Bearbeitungsverfahren von technischen Kunststoffen sind Kühlmittel nicht erforderlich. Wir empfehlen jedoch Kühlmittel in den folgenden Fällen:
- Beim Bohren oder Trennen von Kunststoffen – zwei Prozesse, die hohe Reibungswärme erzeugen.
- Bei der Bearbeitung von besonders kerbempfindlichen Werkstoffen, wie Ertalyte™ PET-P, Duratron™ PAI, Duratron™ PBI und glas- oder kohlefaserverstärkten Produkten.
- Wenn es darum geht, optimale Oberflächengüten und enge Toleranzen zu erreichen.
Tipps zur Auswahl eines Kühlmittels
- Sprühnebel und Druckluft sind sehr wirksame Mittel zur Kühlung der Schnittfläche.
- Allzweck-Schneidflüssigkeiten auf Erdölbasis sind zwar für viele Metalle und Kunststoffe geeignet, können aber bei amorphen Kunststoffen wie Altron™ PC, Sultron™ PSU, Sultron™ PPSU und Duratron™ U1000 PEI zu Spannungsrissen führen.
- Zwei für die meisten Kunststoffe geeignete Kühlmittelspülungen sind Trim E190 und Tim Sol LC SF.
-
Was ist Tempern?
Das Tempern ist ein Wärmebehandlungsverfahren, das die physikalischen Eigenschaften eines Kunststoffs verbessert, indem es zur leichteren Formbearbeitbarkeit seine Dehnbarkeit erhöht und seine Härte verringert. Durch das Tempern werden innere Spannungen im Kunststoff abgebaut, wodurch das bearbeitete Teil eine höhere Formbeständigkeit erhält. Beim Tempern wird ein Kunststoffteil über einen bestimmten Zeitraum auf die Hälfte seiner Schmelztemperatur erwärmt und dann mit einer bestimmten Geschwindigkeit abgekühlt.
Tempern vor der Bearbeitung
Viele Kunststoffhalbzeuge der Mitsubishi Chemical Group Advanced Materials Division werden in einem speziellen Spannungsabbauprogramm getempert. Dadurch werden die prozessbedingt entstandenen inneren Spannungen minimiert. Dadurch wird sichergestellt, dass das Material während und nach der Bearbeitung formstabil bleibt.
Tempern nach der Bearbeitung
Einige bearbeitete Kunststoffteile müssen nach der Bearbeitung getempert werden, um die Maß- oder Qualitätsanforderungen zu erfüllen. Das Nachtempern hat jedoch mehrere Vorteile:
- Verbesserte chemische Beständigkeit – PC-, PSU- und PEI-Materialien können durch Nachtempern unempfindlicher gegenüber Spannungsrissbildung werden.
- Bessere Ebenheit, engere Toleranzen– Teile mit extrem engen Toleranzen, die eine präzise Ebenheit und unsymmetrische Konturen erfordern, müssen manchmal zwischen den Bearbeitungsvorgängen getempert werden.
- PAI mit hoher Druckgeschwindigkeit und geringem Verschleiß– Extrudierte oder spritzgegossene-Duratron™ PAI-Teile, die hohe Druckgeschwindigkeiten oder einen möglichst geringen Verschleißfaktor erfordern, profitieren von einer zusätzlichen Aushärtung nach der Bearbeitung. Dieser Aushärtungsprozess optimiert die Verschleißeigenschaften. Nur PAI profitiert von einem solchen Zyklus.
Tipps zum Tempern von Kunststoffen- Eine bessere Ebenheit kann durch Schruppen, Tempern und Fertigbearbeitung mit einem sehr leichten Schnitt erreicht werden.
- Um das Potenzial für eingearbeitete Spannungen zu verringern, sollten Sie die Fertigungsrichtlinien für das jeweilige Material beachten. Wichtig: Die Richtlinien variieren je nach Materialtyp.
- Stellen Sie sicher, dass die Teile in der erforderlichen Form oder Ebenheit fixiert sind, um Verformungen zu vermeiden. Heben Sie die Fixierung erst auf, wenn die Teile den gesamten Zyklus durchlaufen haben und sich kühl anfühlen.
- Die Fertigbearbeitung auf engtolerierte Endmaße sollte nach dem Tempern erfolgen.
- Bei dünnen Querschnitten sind Änderungen der Aufheiz- und Haltezeit möglich.
-
-
Richtlinien zur Fehlerbehebung bei technischen Kunststoffen
-
- Gewindebohrung
- Nicht ordnungsgemäß geschärfter Bohrer
- Zu geringer Abstand
- Vorschub zu stark
- Verbrannte oder geschmolzene Oberfläche
- Falscher Bohrertyp
- Nicht ordnungsgemäß geschärfter Bohrer
- Vorschub zu gering
- Stumpfer Bohrer
- Steg zu dick
- Absplitternde Oberfläche
- Vorschub zu stark
- Zu großer Abstand
- Zu viel Schränkung (dünner Steg, wie beschrieben)
- Rattern
- Zu großer Abstand
- Vorschub zu gering
- Bohrerüberstand zu groß
- Zu viel Schränkung (dünner Steg, wie beschrieben)
- Vorschubspuren oder spiralförmige Linien am Innendurchmesser
- Vorschub zu stark
- Bohrer nicht zentriert
- Bohrergrund nicht zentriert
- Überdimensionierte Löcher
- Bohrergrund nicht zentriert
- Steg zu dick
- Zu geringer Abstand
- Vorschubgeschwindigkeit zu hoch
- Spitzenwinkel zu groß
- Unterdimensionierte Löcher
- Stumpfer Bohrer
- Zu großer Abstand
- Spitzenwinkel zu klein
- Löcher nicht konzentrisch
- Vorschub zu stark
- Spindeldrehzahl zu niedrig
- Bohrer dringt zu weit in das nächste Stück ein
- Abstechwerkzeug verlässt die Feder und lenkt den Bohrer ab
- Steg zu dick
- Drehzahl des Bohrers am Anfang zu hoch
- Bohrer nicht in der Mitte montiert
- Bohrer nicht richtig geschärft
- Grat an der Trennstelle
- Stumpfes Abstechwerkzeug
- Der Bohrer geht nicht vollständig durch das Werkstück
- Schnelles Abstumpfen des Bohrers
- Vorschub zu gering
- Spindeldrehzahl zu hoch
- Unzureichende Schmierung durch das Kühlmittel
- Gewindebohrung
-
- Geschmolzene Oberfläche
- Stumpfe oder reibende Kante
- Zu geringer Seitenabstand
- Vorschubgeschwindigkeit zu niedrig
- Spindeldrehzahl zu hoch
- Raue Oberfläche
- Vorschub zu stark
- Falsche Freiwinkel
- Scharfe Spitze am Werkzeug (leichter Nasenradius erforderlich)
- Werkzeug nicht in der Mitte montiert
- Grate an den Schnittkanten
- Keine Schräge an scharfen Ecken zugelassen
- Stumpfes Werkzeug
- Zu geringer Seitenabstand
- Der Anschnittwinkel ist am Werkzeug nicht vorgesehen (das Werkzeug sollte sich allmählich aus dem Schnitt lösen, nicht plötzlich)
- Risse oder Absplitterungen an den Ecken
- Zu viel positive Schränkung am Werkzeug
- Werkzeug wird nicht in den Schnitt geführt (schlägt plötzlich auf das Werkstück)
- Stumpfes Werkzeug
- Werkzeug unter der Mitte montiert
- Scharfe Spitze am Werkzeug (leichter Nasenradius erforderlich)
- Rattern
- Zu großer Spitzenradius am Werkzeug
- Werkzeug nicht fest montiert
- Material nicht richtig gestützt
- Schnittbreite zu groß (zwei Schnitte verwenden)
- Geschmolzene Oberfläche
-
- Geschmolzene Oberfläche
- Stumpfes Werkzeug
- Zu geringer Seitenabstand
- Unzureichende Kühlmittelzufuhr
- Raue Oberfläche
- Vorschub zu stark
- Werkzeug unsachgemäß geschärft
- Schneide nicht geschliffen
- Spiralförmige Markierungen
- Werkzeug reibt beim Rückzug
- Grat an der Spitze des Werkzeugs
- Konkave oder konvexe Oberflächen
- Spitzenwinkel zu groß
- Werkzeug nicht rechtwinklig zur Spindel
- Werkzeugablenkung
- Vorschub zu stark
- Werkzeug von oben oder unten mittig montiert
- Federn oder Grate an der Trennstelle
- Spitzenwinkel nicht groß genug
- Stumpfes Werkzeug
- Vorschub zu stark
- Grate am Außendurchmesser
- Keine Kammer vor Abstichdurchmesser
- Stumpfes Werkzeug
- Geschmolzene Oberfläche
-
-
Laden Sie das komplette Toolkit für Maschinenbediener herunter
-
Empfohlene Drehzahlen, Werkzeuge und vieles mehr
Weitere Informationen über unsere thermoplastischen Produkte Laden Sie unser „Toolkit für Maschinenbediener“ herunter, ein vollständiger Fertigungsleitfaden mit empfohlenen Drehzahlen und Werkzeugen für eine Reihe von Werkstoffen der Mitsubishi Chemical Group.
-
Kontaktieren Sie unsere Spezialistenteams, indem Sie das Kontaktformular ausfüllen. Wir sind gespannt auf Ihre nächste Aufgabe.
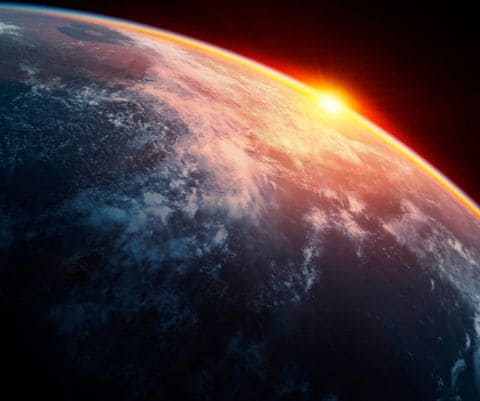