Forschung und Entwicklung für bessere Leistung im Flüssigkeits-Management
Die Mitsubishi Chemical Group ist führend in der Entwicklung fortschrittlicher Werkstoffe für den Transport und die Verarbeitung von Gasen und Flüssigkeiten. Wir bieten maßgeschneiderte Lösungen für das Fluidmanagement in verschiedenen Industriezweigen, darunter auch auf dem Energiemarkt. Unser Angebot umfasst Materialinnovationen, Forschung, Entwicklung und Tests, um die bestmöglichen Lösungen zu gewährleisten. Entlang des gesamten Projektablaufs gewährleisten wir Kompetenz, pünktliche Lieferung und zuverlässige Materialqualität.
Wir sind vertikal integriert mit bewährten Hochleistungspolymeren und fortschrittlichen Fertigungs- und Roboteranlagen. Unsere Anwendungsingenieure und Geschäftsteams stehen Ihnen mit all ihrem Wissen zur Seite, um Ihre Idee bis zum fertigen Bauteil zu realisieren.
Durch die intensive Zusammenarbeit mit Chemikern und Ingenieuren verbessern unsere Produkte die Sicherheit, Langlebigkeit und Effizienz im modernen Flüssigkeitsmanagement. Im Einklang mit unserer KAITEKI Philosophie trägt unser Angebot auch dazu bei, eine Kreislaufwirtschaft zu ermöglichen und den Kohlenstoff-Fußabdruck zu reduzieren, während wir gleichzeitig sicherstellen, dass die Geräte unserer Kunden nicht ausfallen oder die Umwelt schädigen.
- Technologie und Instrumente für proaktive FuE und Werkstoffinnovation
- Vertikale Integration und vielfältige globale Produktions- und Lieferkapazitäten
- Partner für die Zusammenarbeit vom Konzept bis zum Funktionsteil
- Ausweitung und Verbesserung des dynamischen Betriebs von Geräten
- Verkürzte Vorlaufzeit für kritische und nicht kritische Anwendungen
- Unterstützung bei Entwurf und Entwicklung von Prototypen
Unser umfangreiches Portfolio an hochentwickelten technischen Materialien erfüllt und übertrifft globale und regionale OEM-Spezifikationen und ermöglicht einen langlebigeren, sichereren und effizienteren Betrieb. Aufgrund der verlängerten Lebensdauer und unseres Engagements für Nachhaltigkeit trägt unser breites Angebot an technischen Kunststoffen dazu bei, sowohl wirtschaftliche als auch ökologische Vorteile bei Anwendungen im Flüssigkeitsmanagement zu erzielen.
- Langlebiger, zuverlässiger Betrieb
- Langlebige Materialien für das Fluidmanagement
- Verbesserte Betriebssicherheit
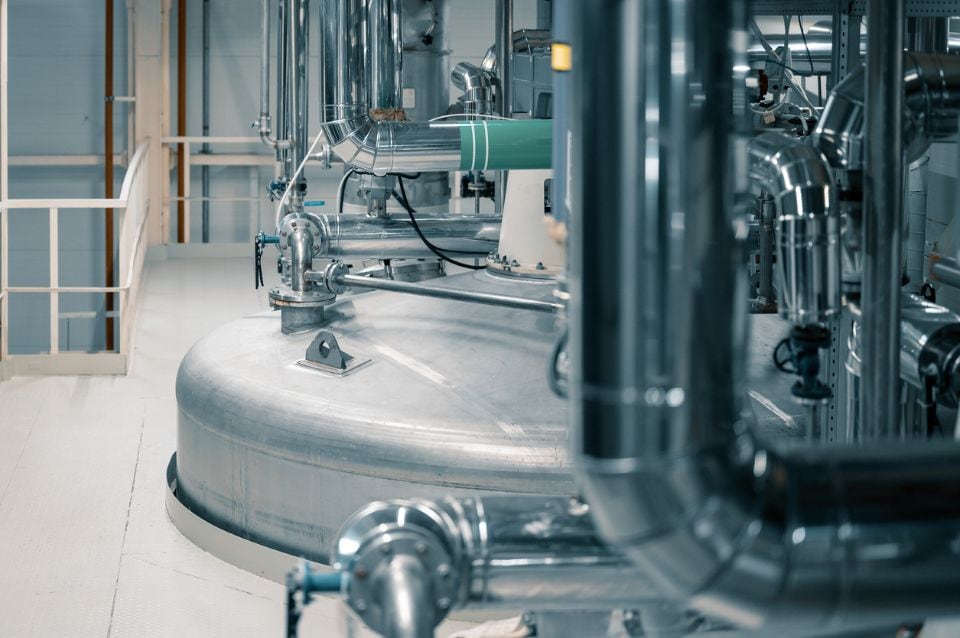
Nachhaltige Forschung und Entwicklung für innovative Materialien im Fluidmanagement
Mit unserem breiten Materialportfolio kann unser Angebot an individuelle Industriespezifikationen angepasst werden, wie zum Beispiel Temperatur, chemische Belastung, mechanische Festigkeit, Flexibilitätsanforderungen und Sicherheitsaspekte. Die Entwicklung unserer Hochleistungsmaterialien – einschließlich unserer einzigartigen Palette an Fluorosint™ Materialien (verstärktes PTFE) – führte zu besserer Anlagen-Effizienz beim Transport von Gas und Flüssigkeiten.
Unsere Technologien und Dienstleistungen verkürzen Durchlaufzeiten, sorgen für eine längere Nutzungsdauer der Teile und bieten eine bessere Wertschöpfung – und das alles mit fachkundiger Unterstützung vom Konzept bis zum funktionsfähigen Teil.
Treffen Sie unser Team auf Events für Erneuerbare Energien
Veranstaltungskalender Erneuerbare Energien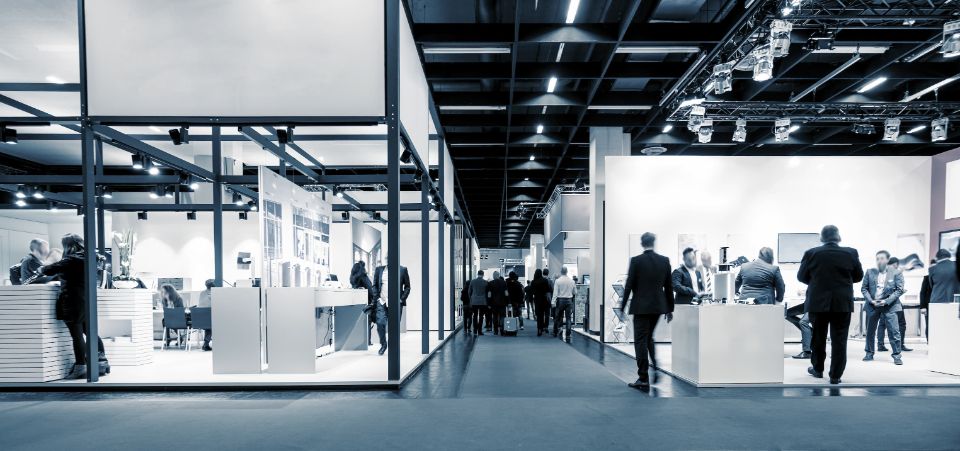
Setzen Sie sich mit unseren Spezialistenteams in Verbindung und füllen Sie hierzu das Kontaktformular aus. Wir sind auf Ihre nächste Herausforderung vorbereitet.
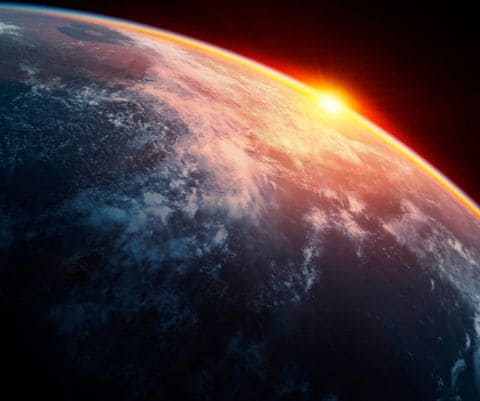