金属与塑料:KyronMAX™ 案例研究
在运用短切碳纤维 KyronMAX™ 注塑成型复合材料的基础上,我们与一家汽车 OEM 展开合作,帮助其减轻商用汽车钢支架的重量。
我们通过与 OEM 工程团队紧密合作,采用特殊预测映射技术和严格测试过程,帮助其最终使用碳纤维复合材料重新设计支架,用以取代先前使用的钢铁。
尽管三维零件几何结构复杂,但 KyronMAX™ 具有独特的机械性能、采用全新充模设计,有助于打造更加可持续、持续可靠、轻质的替代方案。
行业:汽车
解决方案:使用注塑成型复合材料重新设计钢支架。
产品:KyronMAX™
结果:碳纤维支架更加轻质、可靠,带来行业变革
降低零件重量,同时维持结构完整性
由于顾客希望中期换型,更换支架,同时维持原部件观感,因此设计和打造可靠且牢固的替换件尤其困难。
新支架的形状、厚度和材质必须与钢支架相似,并满足汽车部件的外部和内部要求。必须仔细考虑结构完整性、尺寸稳定性、抗紫外线性能和全天候工作能力。
推荐使用我们的高性能短切碳纤维 KyronMAX™ 注塑成型复合材料,与传统玻璃和其他碳纤维填充的系统相比,该材料具有更高的机械强度。
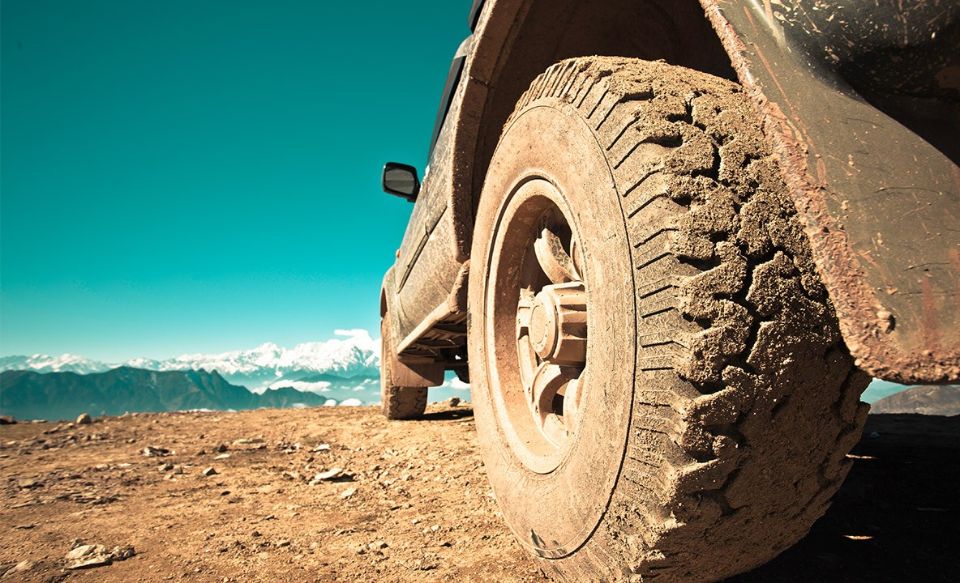
使用短纤维复合材料,满足零件强度要求
我们的材料专家与 OEM 的工程团队紧密合作,通过测试适用成型方法预测新支架的优缺点。
我们对客户的原设计方案进行了初始模流分析,结果表明零件会在达到所需强度一半时即出现故障。我们向客户提出了若干设计修改和充模调整建议,改善了碳纤维整体取向分布和流动情况。
因此,与原钢制零件相比,碳纤维零件不仅外观相似,而且总体积更小、无需补充加强筋,符合 OEM 的强度和安全要求。
使用 KyronMAX™ 和我们的全新充模设计可以提供 80% 的熔接缝强度,而竞品复合材料仅可提供 40%。
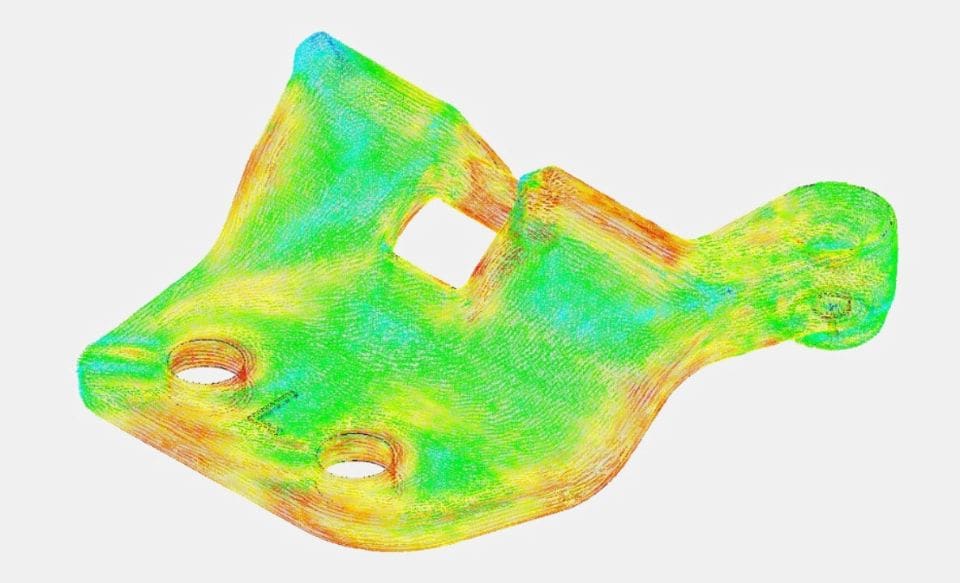
零件更加可靠、更可持续和轻质
多数公司难以在碳纤维成型期间精准预测和映射颗粒流动情况,我们属于其中为数不多的一家。我们不仅运用此项技术精准预测零件强度和劣势,还采用先进的碳纤维复合材料将原支架的重量减轻 76%。
重量减轻还有助于减少耗气量,客户可据此利用占比更高的可回收材料生产更加可持续的汽车。
- 材料性能可预测
- 重量整体减轻 79%(所有硬顶汽车)
- 汽车部件成本降低 38% 以上
- 二氧化碳排放减少
- 汽车重心下降,汽车整体性能提高
- 生产过程更加可持续
- 碳纤维材料可回收
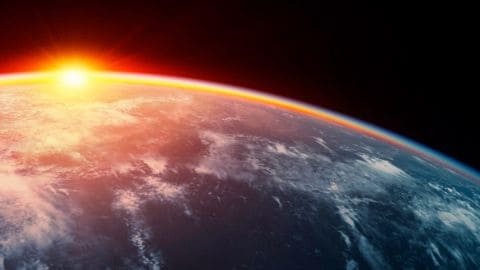