Métal contre plastique : étude de cas KyronMAX™
Pour aider un équipementier automobile à réduire le poids des supports en acier équipant ses véhicules commerciaux, nous avons utilisé nos composites KyronMAX™ moulables par injection en fibre courte de carbone.
En collaboration étroite avec les équipes techniques, nous avons mis en œuvre nos technologies exclusives de mappage prédictif, et des processus de test rigoureux, pour établir la nouvelle conception finale de ces supports en remplaçant l'acier par des composites en fibre de carbone.
Malgré la complexité géométrique de cette pièce tridimensionnelle, les propriétés mécaniques uniques du KyronMAX™ et notre nouvelle méthode de remplissage des moules nous ont permis de produire une alternative durable et légère offrant une fiabilité constante.
Secteur : automobile
Solution : repenser les supports en acier grâce à l'injection composites.
Produit : KyronMAX™
Résultats : un support en fibre de carbone plus léger et plus fiable qui a révolutionné le secteur
Réduire le poids de la pièce sans perdre en intégrité structurelle
Comme notre client souhaitait remplacer les supports au milieu de l'année modèle sans modifier l'aspect d'origine des composants, il a été particulièrement difficile de concevoir et de créer une pièce de remplacement à la fois fiable et solide.
Les nouveaux supports devaient non seulement avoir la forme, l'épaisseur et la texture des supports en acier d'origine, mais aussi répondre aux exigences des composants automobiles pour l'extérieur et l'intérieur. Il convenait de considérer avec attention leur intégrité structurelle, leur stabilité dimensionnelle, leur résistance aux UV et leur capacité de fonctionnement, quelles que soient les conditions météorologiques.
Nous avons recommandé nos composites à fibres de carbone courtes hautes performances moulables par injection KyronMAX™ qui offrent une résistance mécanique bien supérieure à celle des charges conventionnelles de verre ou de noir de carbone.
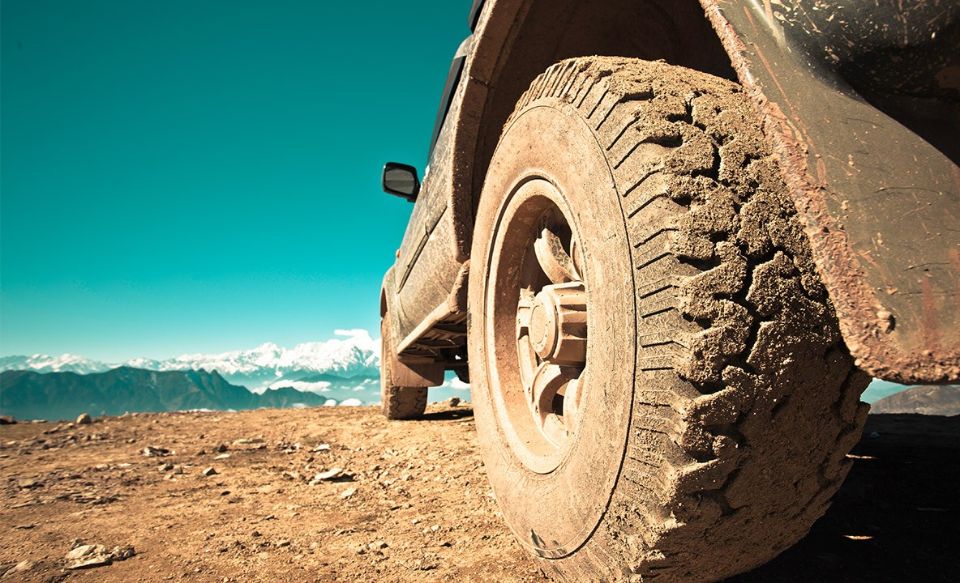
Atteindre la résistance voulue avec des composites à fibre courte
Nos experts en matériaux ont collaboré étroitement avec les ingénieurs de l'OEM pour prédire les points forts et les points faibles des nouveaux supports en testant différentes méthodes de moulage pour identifier la meilleure.
Notre première analyse du flux de remplissage du moule sur les conceptions initialement proposées par le client a révélé que la résistance de la pièce serait inférieure de moitié environ à ses attentes. Nous avons alors suggéré diverses modifications de la conception et certains réglages du remplissage, qui ont permis d'améliorer le flux et l'alignement général de la fibre de carbone.
Nous avons ainsi obtenu une pièce en fibre de carbone très semblable d'aspect à sa version d'origine en acier, mais moins volumineuse, ne nécessitant pas de nervures de renfort supplémentaires et répondant aux exigences de l'OEM en termes de sécurité et de résistance.
Avec le KyronMAX™ et notre nouveau concept de remplissage des moules, nous avons obtenu 80% de résistance dans la ligne de fusion, contre seulement 40% avec les autres matériaux composites envisagés.
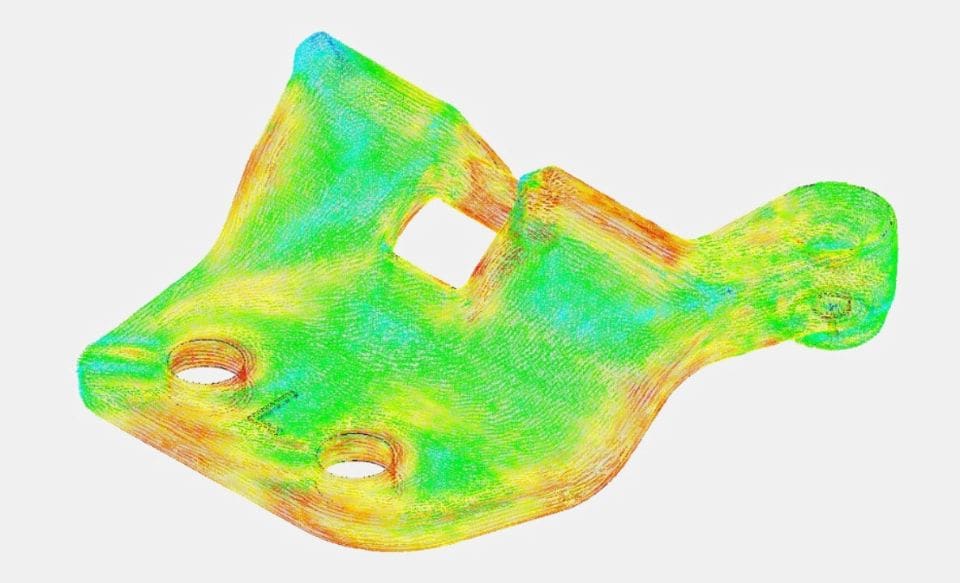
Des pièces plus fiables et plus durables, mais beaucoup plus légères
Nous faisons partie des rares entreprises capables de prédire et de mapper précisément le flux des particules de fibre de carbone dans un moule. Avec nos matériaux composites avancés en fibre de carbone et grâce à cette technologie, nous avons pu non seulement prévoir les forces et les faiblesses de la pièce, mais aussi réduire son poids de 76% par rapport aux supports d'origine.
Cela contribue aussi à réduire la consommation de carburant, ce qui permet à notre client de produire des véhicules plus durables avec davantage de matériaux recyclés.
- Performances du matériau prévisibles
- Poids global réduit de 79% (par véhicule équipé d'un toit rigide amovible)
- Économie de plus 38% sur le coût du composant
- Émissions de CO₂ réduites
- Centre de gravité plus bas et performances globales du véhicule améliorées
- Processus de production plus durable
- Matériau en fibre de carbone recyclable
Vous cherchez quelque chose en particulier ? Contactez notre équipe de spécialistes en remplissant le formulaire de contact. Nous sommes prêts à relever votre prochain défi.
Contactez-nous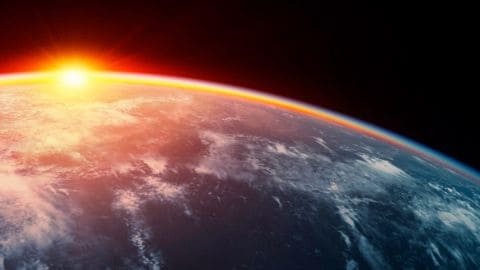