Guide de sélection des matériaux plastiques
Une meilleure conception, une fabrication plus rapide, des coûts et délais de production réduits, de meilleures performances… Les OEM ne manquent pas d'arguments pour adopter les plastiques techniques. Ce guide en cinq étapes vous aide à choisir la matière thermoplastique la plus adaptée à tous vos besoins.
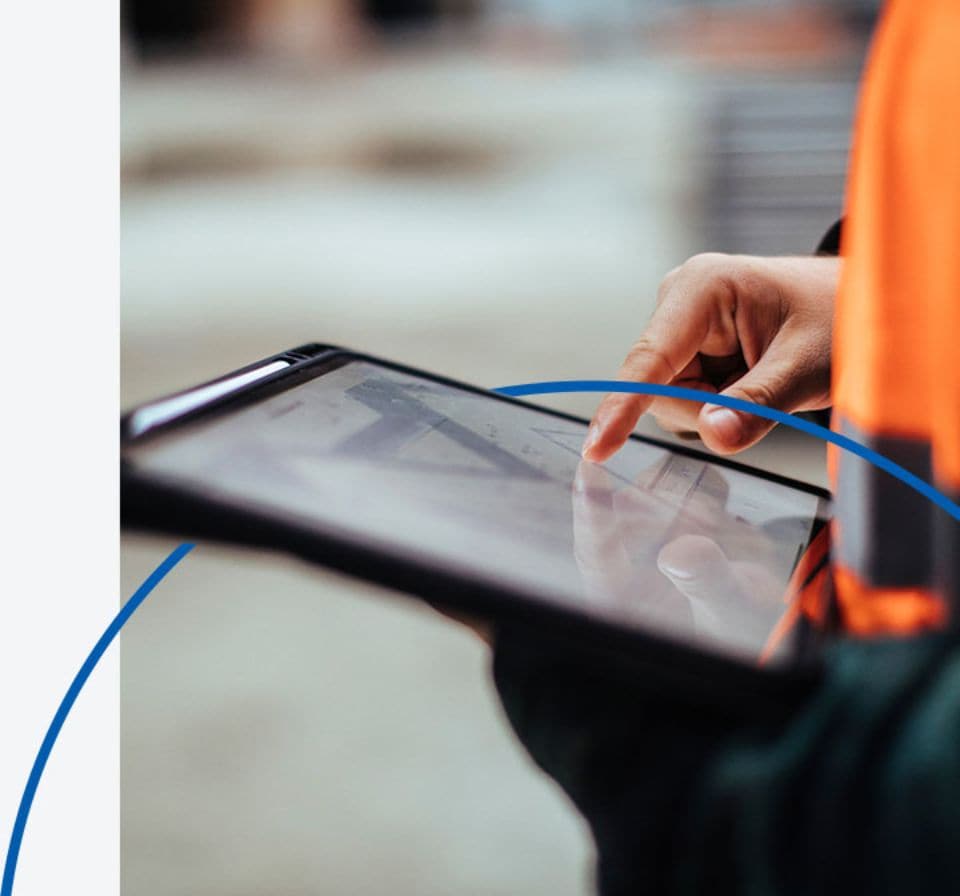
De plus en plus de plastiques hautes performances remplacent des matériaux comme le bronze, l'acier inoxydable, l'aluminium et la céramique. Voici les principaux arguments pour passer au plastique :
- Meilleure durée de vie des pièces
- Lubrification inutile
- Diminution de l'usure des pièces en contact
- Fonctionnement des équipements/lignes plus rapide
- Réduction de la consommation énergétique des équipements
- Tenue chmique et résistance à la corrosion et à l'inertie
- Réduction du poids
Face aux nombreux plastiques disponibles sur le marché, il peut être compliqué de choisir le plus approprié à votre application. Nous avons donc créé le guide ci-dessous pour toutes les personnes qui découvrent le monde des plastiques techniques.
1. Quel est l'objectif de l'application générale ?
-
Sera-t-il utilisé pour une application de type palier soumis à l'usure ?
Les propriétés d'usure sont améliorées par le bisulfure de molybdène (MoS2), le graphite, la fibre de carbone et les lubrifiants polymères (PTFE, cires). Pour les applications supports soumises à usure, la première caractéristique à prendre en considération est la performance à l'usure, exprimée par le PV (Pression-Vitesse) et le facteur K. Calculez le PV (pression en N/mm² × vitesse en m/s) puis, à l'aide du graphique ci-dessous, sélectionnez les matériaux dont le PV maxi est supérieur au PV calculé pour l'application. Vous pouvez affiner votre choix en vérifiant le facteur K des matériaux. En général, plus le facteur K est bas, plus la durée de vie du matériau est longue.
S’agit-il d’une application structurelle statique ou dynamique ?
Les pièces de structures sont généralement conçues pour résister en continu à des contraintes équivalentes à 25 % de leur résistance maximale à une température donnée. Cette règle permet de compenser le fluage dû à la viscoélasticité du plastique. Les courbes isométriques de contrainte-temps ci-dessous vous aiderons à déterminer l’évolution de la résistance d’un matériau dans le temps à température ambiante et à 150°C.
2. Quelles sont les exigences thermiques du matériau plastique ?
-
Cet indicateur correspond à la température de ramollissement d'un matériau généralement acceptée comme limite de température maximale pour les composants modérément, à fortement sollicités, et sans contrainte.
-
La température de service en continu est généralement indiquée comme la température au-dessus de laquelle une dégradation significative et permanente des propriétés physiques se produit après une exposition à long terme. Cette directive ne doit pas être confondue avec les températures de fonctionnement continu, ou d'utilisation, signalées par les organismes de réglementation tels que l'Underwriters Laboratories (UL).
-
Le point de fusion des matériaux cristallins et la température de transition vitreuse des matériaux amorphes sont les températures extrêmes à court terme, auxquelles la stabilité de forme est maintenue. Pour la plupart des matières plastiques techniques, leur utilisation à (ou au-dessus de) ces températures doit être évitée.
3. À quels produits chimiques sera exposé le matériau plastique ?
-
Prédire les exigences de résistance chimique dans une application peut être difficile, car plusieurs facteurs comme la concentration, la température, la durée et la contrainte peuvent avoir une influence sur une bonne adéquation. Pour cette raison, nous recommandons de tester les matériaux dans des conditions réelles d'utilisation.
En règle générale, les thermoplastiques ont l'avantage de bien résister à une large palette de produits chimiques, et ont de bonnes chances de convenir aux spécifications de votre application.
Par exemple, le nylon, l'acétal et le PET-P Ertalyte™ ont des propriétés de résistance chimique qui conviennent généralement aux interactions avec la plupart des produits chimiques utilisés dans les applications industrielles standards. Les matériaux cristallins hautes performances tels que les PTFE chargés Fluorosint™, le Techtron™PPS et le Ketron™ PEEK conviennent davantage aux environnements chimiques plus extrêmes.
4. Autres critères à prendre en compte
-
- Dureté/résistance relative aux impacts
- Stabilité dimensionnelle
- Inflammabilité
- Propriétés électriques
- Résistance aux UV et aux rayonnements, capacité d'autoclavage, dégazage, etc.
- Conformité aux organismes et aux réglementations
Les matériaux avec un allongement à la traction, une résistance aux chocs Izod et à la traction plus élevés sont généralement plus résistants et moins sensibles aux entailles quand ils sont soumis à des charges avec impacts.
-
Les plastiques techniques peuvent se contracter et se dilater 2 à 20 fois plus que de nombreux métaux au fil des variations de température. Le coefficient de dilatation thermique linéaire est utilisé pour estimer le taux de dilatation des matériaux plastiques techniques. Il est exprimé à la fois sous forme de température et de valeur moyenne. La Figure 6 indique comment certains plastiques techniques réagissent aux températures élevées.
Le coefficient d'élasticité et la capacité d'absorption d'eau contribuent également à la stabilité dimensionnelle du matériau. Vérifiez donc les effets de l'humidité et de la vapeur.
-
Des organismes tels que la Food and Drug Administration (FDA), le ministère de l'Agriculture des États-Unis (USDA), l'Underwriters Laboratory (UL), l'association 3A-Dairy et l'American Bureau of Shipping (ABS) définissent, ou approuvent fréquemment des directives spécifiques pour l'usage des matériaux à leur secteur d'activité. Référez-vous à ces cadres de référence pour analyser les données relatives aux performances des matériaux.
5. Quel produit plastique convient le mieux à votre pièce ?
-
Mitsubishi Chemical Group propose aux concepteurs la plus grande variété de dimensions et de configurations pour les produits thermoplastiques et les pièces semi-finies. Examinez toutes les options de produits pour choisir la forme la plus économique et réduire vos coûts de fabrication.
Consultez les méthodes de traitement que nous recommandons en fonction des différents produits :
Description des produits Méthode de traitement recommandée Longues sections
Petits diamètresExtrusion Ronds plurial plein, plaques, bandes, profilés, tubes, bagues Demi-produits de grande dimension
PréformesCoulage Configurations spéciales de Ronds pleins, plaques, tubes Produits techniques avancés de petite dimension Moulage par compression Ronds, disques, plaques, tubes Pièces de petites dimensions en matériaux hautes performances
Petits diamètres
Moulage par injection Ronds, disques, plaques, tubes Remarque : d'applications en applications, de nombreux choix de matériaux restent inchangés. Cependant, il existe des différences de propriétés physiques basées sur la technique de transformation utilisée pour créer le produit.
Par exemple :
- Les pièces moulées par injection présentent la plus grande anisotropie (les propriétés dépendent de la direction).
- Les produits extrudés ont un comportement légèrement anisotrope.
- Les produits moulés par compression sont isotropes : leurs propriétés sont les mêmes dans toutes les directions.
-
L'usinabilité d'un thermoplastique doit être prise en compte lors de la sélection des matériaux. Un matériau difficile à usiner ne conviendra pas forcément aux pièces particulièrement complexes, en plus de coûter plus cher.
Tous les matériaux thermoplastiques de Mitsubishi Chemical Group ont été stabilisés afin d'éliminer les contraintes internes et améliorer leur usinabilité. En général, lors de l'usinage, les thermoplastiques renforcés (fibres de carbone, verre) sont significativement plus sensibles à l'entaille, et plus abrasifs pour les outils, que les thermoplastiques non chargés ; en revanche, les thermoplastiques renforcés sont généralement plus stables.
En raison de leur extrême dureté, l'usinage de des matériaux à base imide (Duratron™ PAI, Duratron™PI et Duratron™PBI) peut être compliqué, et doit être réalisé avec des outils en polycristallin diamant et carbure. Pour vous aider à évaluer leur usinabilité, passez en revue la cote d'usinabilité relative de nos produits
-
1. Quel est l'objectif de l'application générale ?
-
Sera-t-il utilisé pour une application de type palier soumis à l'usure ?
Les propriétés d'usure sont améliorées par le bisulfure de molybdène (MoS2), le graphite, la fibre de carbone et les lubrifiants polymères (PTFE, cires). Pour les applications supports soumises à usure, la première caractéristique à prendre en considération est la performance à l'usure, exprimée par le PV (Pression-Vitesse) et le facteur K. Calculez le PV (pression en N/mm² × vitesse en m/s) puis, à l'aide du graphique ci-dessous, sélectionnez les matériaux dont le PV maxi est supérieur au PV calculé pour l'application. Vous pouvez affiner votre choix en vérifiant le facteur K des matériaux. En général, plus le facteur K est bas, plus la durée de vie du matériau est longue.
S’agit-il d’une application structurelle statique ou dynamique ?
Les pièces de structures sont généralement conçues pour résister en continu à des contraintes équivalentes à 25 % de leur résistance maximale à une température donnée. Cette règle permet de compenser le fluage dû à la viscoélasticité du plastique. Les courbes isométriques de contrainte-temps ci-dessous vous aiderons à déterminer l’évolution de la résistance d’un matériau dans le temps à température ambiante et à 150°C.
-
-
2. Quelles sont les exigences thermiques du matériau plastique ?
-
Cet indicateur correspond à la température de ramollissement d'un matériau généralement acceptée comme limite de température maximale pour les composants modérément, à fortement sollicités, et sans contrainte.
-
La température de service en continu est généralement indiquée comme la température au-dessus de laquelle une dégradation significative et permanente des propriétés physiques se produit après une exposition à long terme. Cette directive ne doit pas être confondue avec les températures de fonctionnement continu, ou d'utilisation, signalées par les organismes de réglementation tels que l'Underwriters Laboratories (UL).
-
Le point de fusion des matériaux cristallins et la température de transition vitreuse des matériaux amorphes sont les températures extrêmes à court terme, auxquelles la stabilité de forme est maintenue. Pour la plupart des matières plastiques techniques, leur utilisation à (ou au-dessus de) ces températures doit être évitée.
-
-
3. À quels produits chimiques sera exposé le matériau plastique ?
-
Prédire les exigences de résistance chimique dans une application peut être difficile, car plusieurs facteurs comme la concentration, la température, la durée et la contrainte peuvent avoir une influence sur une bonne adéquation. Pour cette raison, nous recommandons de tester les matériaux dans des conditions réelles d'utilisation.
En règle générale, les thermoplastiques ont l'avantage de bien résister à une large palette de produits chimiques, et ont de bonnes chances de convenir aux spécifications de votre application.
Par exemple, le nylon, l'acétal et le PET-P Ertalyte™ ont des propriétés de résistance chimique qui conviennent généralement aux interactions avec la plupart des produits chimiques utilisés dans les applications industrielles standards. Les matériaux cristallins hautes performances tels que les PTFE chargés Fluorosint™, le Techtron™PPS et le Ketron™ PEEK conviennent davantage aux environnements chimiques plus extrêmes.
-
-
4. Autres critères à prendre en compte
-
- Dureté/résistance relative aux impacts
- Stabilité dimensionnelle
- Inflammabilité
- Propriétés électriques
- Résistance aux UV et aux rayonnements, capacité d'autoclavage, dégazage, etc.
- Conformité aux organismes et aux réglementations
Les matériaux avec un allongement à la traction, une résistance aux chocs Izod et à la traction plus élevés sont généralement plus résistants et moins sensibles aux entailles quand ils sont soumis à des charges avec impacts.
-
Les plastiques techniques peuvent se contracter et se dilater 2 à 20 fois plus que de nombreux métaux au fil des variations de température. Le coefficient de dilatation thermique linéaire est utilisé pour estimer le taux de dilatation des matériaux plastiques techniques. Il est exprimé à la fois sous forme de température et de valeur moyenne. La Figure 6 indique comment certains plastiques techniques réagissent aux températures élevées.
Le coefficient d'élasticité et la capacité d'absorption d'eau contribuent également à la stabilité dimensionnelle du matériau. Vérifiez donc les effets de l'humidité et de la vapeur.
-
Des organismes tels que la Food and Drug Administration (FDA), le ministère de l'Agriculture des États-Unis (USDA), l'Underwriters Laboratory (UL), l'association 3A-Dairy et l'American Bureau of Shipping (ABS) définissent, ou approuvent fréquemment des directives spécifiques pour l'usage des matériaux à leur secteur d'activité. Référez-vous à ces cadres de référence pour analyser les données relatives aux performances des matériaux.
-
-
5. Quel produit plastique convient le mieux à votre pièce ?
-
Mitsubishi Chemical Group propose aux concepteurs la plus grande variété de dimensions et de configurations pour les produits thermoplastiques et les pièces semi-finies. Examinez toutes les options de produits pour choisir la forme la plus économique et réduire vos coûts de fabrication.
Consultez les méthodes de traitement que nous recommandons en fonction des différents produits :
Description des produits Méthode de traitement recommandée Longues sections
Petits diamètresExtrusion Ronds plurial plein, plaques, bandes, profilés, tubes, bagues Demi-produits de grande dimension
PréformesCoulage Configurations spéciales de Ronds pleins, plaques, tubes Produits techniques avancés de petite dimension Moulage par compression Ronds, disques, plaques, tubes Pièces de petites dimensions en matériaux hautes performances
Petits diamètres
Moulage par injection Ronds, disques, plaques, tubes Remarque : d'applications en applications, de nombreux choix de matériaux restent inchangés. Cependant, il existe des différences de propriétés physiques basées sur la technique de transformation utilisée pour créer le produit.
Par exemple :
- Les pièces moulées par injection présentent la plus grande anisotropie (les propriétés dépendent de la direction).
- Les produits extrudés ont un comportement légèrement anisotrope.
- Les produits moulés par compression sont isotropes : leurs propriétés sont les mêmes dans toutes les directions.
-
L'usinabilité d'un thermoplastique doit être prise en compte lors de la sélection des matériaux. Un matériau difficile à usiner ne conviendra pas forcément aux pièces particulièrement complexes, en plus de coûter plus cher.
Tous les matériaux thermoplastiques de Mitsubishi Chemical Group ont été stabilisés afin d'éliminer les contraintes internes et améliorer leur usinabilité. En général, lors de l'usinage, les thermoplastiques renforcés (fibres de carbone, verre) sont significativement plus sensibles à l'entaille, et plus abrasifs pour les outils, que les thermoplastiques non chargés ; en revanche, les thermoplastiques renforcés sont généralement plus stables.
En raison de leur extrême dureté, l'usinage de des matériaux à base imide (Duratron™ PAI, Duratron™PI et Duratron™PBI) peut être compliqué, et doit être réalisé avec des outils en polycristallin diamant et carbure. Pour vous aider à évaluer leur usinabilité, passez en revue la cote d'usinabilité relative de nos produits
-
Vous souhaitez échanger avec un expert en sélection des matériaux ? Parlez-en à nos équipes spécialisées en remplissant le formulaire de prise de contact. Nous sommes prêts à relever votre prochain défi.
Contactez-nous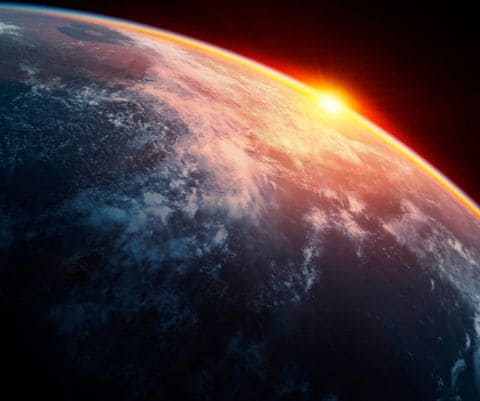