Simplifiez la fabrication grâce à des pièces moulées par injection
Parcourez notre gamme de matériaux plastiques et composites moulés par injection, découvrez notre aide complète à la conception des moules, ainsi que nos technologies avancées de prototypage et de test.
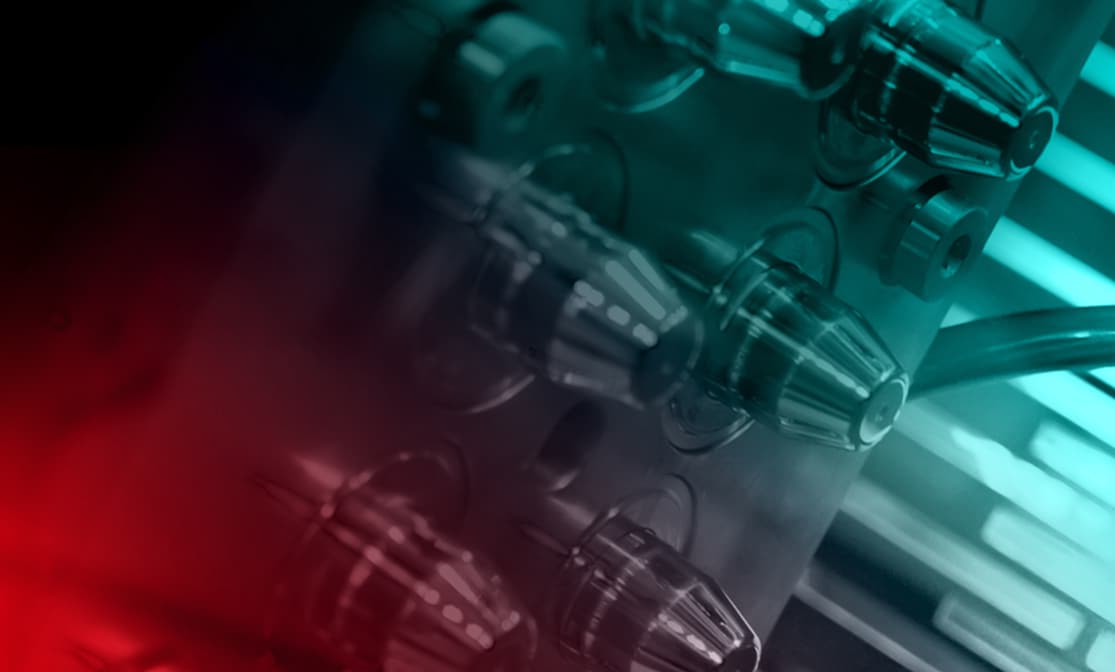
La division Advanced Materials du Mitsubishi Chemical Group conçoit, teste et produit des composants moulés par injection qui jouent un rôle essentiel dans des systèmes utilisés dans des secteurs aussi variés que l’automobile, le médical et l’électronique.
L’interaction entre les composants moulés par injection et le reste du produit fini est pour le moins complexe. En plus du respect des normes strictes de fonctionnalité et de performance, ils doivent également prendre en considération l’influence qu’ils exercent sur la perception des utilisateurs.
Depuis le lancement du programme de moulage par injection en 1933, Mitsubishi Chemical Group a énormément investi dans le développement des capacités de production, des connaissances et des technologies pour produire des pièces injectées à la fois très performantes, et économiques.
Notre service sur le moulage par injection repose sur :
- Notre large gamme de matériaux;
- Notre expertise et notre aide à la conception;
- nos méthodes éprouvées de prototypage et de test.
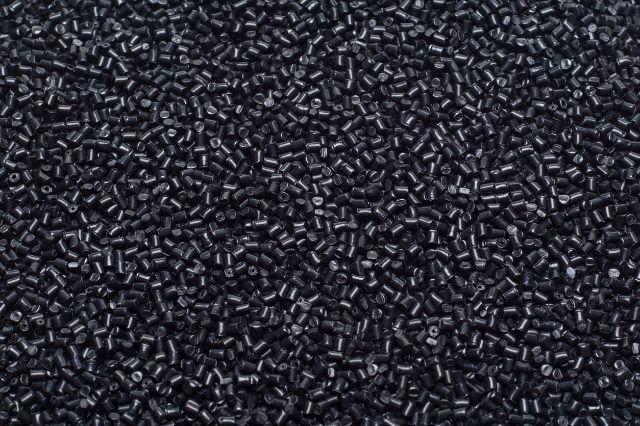
Matériaux moulables par injection
Nos équipes techniques travaillent étroitement avec les clients pour développer une compréhension privilégiée des performances de leurs pièces et des spécifications budgétaires, afin qu’ils puissent choisir au sein de notre large gamme, le meilleur plastique, le meilleur composite.
Alors que la majorité des plastiques techniques ne sont disponibles qu'uniquement sous forme de demi-produits, nous pouvons proposer l'injection pour la plupart des matériaux techniques de notre offre. C’est le cas, notamment, pour nos plastiques techniques généraux (PA, PP, POM), ainsi que l'Ertalyte™ PET-P et le Techtron™ PPS. Cette option est également disponible pour nos composites et thermoplastiques hautes performances (composites en fibre de carbone KyronMAX™, Duratron™ PAI et PEI, Ketron™ PEEK) en cas d'applications extrêmes nécessitant une résistance mécanique exceptionnelle.
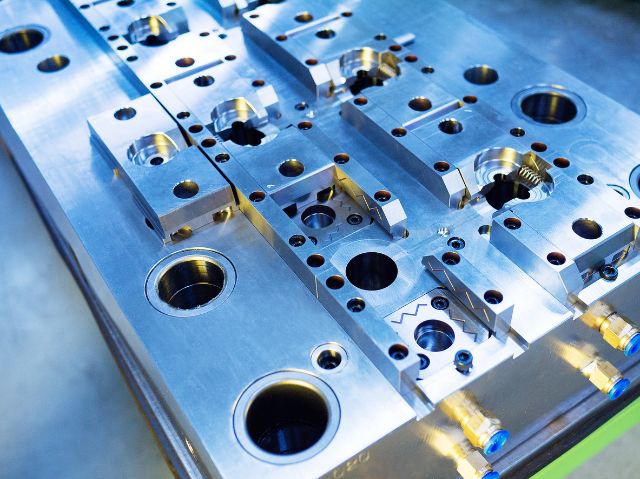
Une aide à la conception de la pièce au moule.
En tant que partenaire global, nous vous accompagnons tout au long de la production de vos pièces injectées, et ceci dès la conception de la pièce et du moule. Nos services d’aide à la conception reposent sur diverses technologies spécialisées pour la fabrication (DFM, Design For Manufacturing), l’assemblage (DFA, Design For Assembly) et le désassemblage (DFD, Fesign For Disassembly), ainsi que sur plusieurs outils de conception assistée par ordinateur (CAO).
La productivité et la durée de vie d'une pièce injectée sont directement liées à la qualité des outils utilisés. Nos capacités à fabriquer en interne des moules de haute qualité augmentent l'efficacité de la production, et garantissent de traduire en transparence les spécifications initiales de conception en pièces finies injectées. Nos ingénieurs qualifiés utilisent des équipements de fabrication de moules à la pointe de la technologie pour développer une gamme d'outils de haute qualité (moules multi-empreintes, canaux chauds, systèmes d'inserts et de surmoulage), pour améliorer la longévité des pièces tout en réduisant les délais de fabrication.
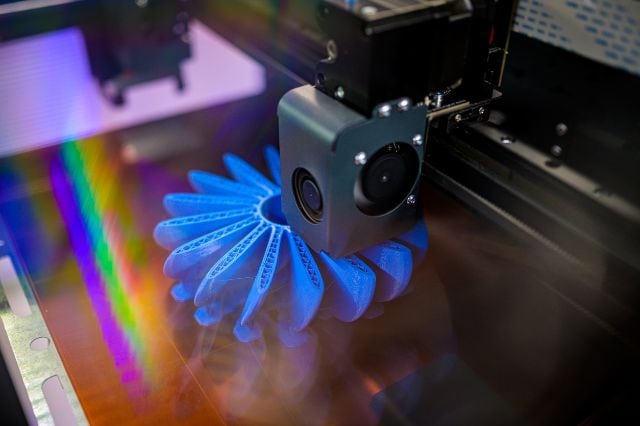
Des solutions intelligentes d’outillage et de prototypage
Nos solutions polyvalentes de création d’outils imprimés par injection soluble SPRINT (Soluble Printed Injection Tooling) nous permettent de créer des prototypes moulés par injection fonctionnels en seulement quelques jours. D’une qualité et d’une précision remarquables, les prototypes SPRINT simplifient les tests et diminuent le coût et les délais de fabrication des moules. D’autre part, Mitsubishi Chemical Group est le fournisseur d'une gamme d'outillages maîtres avec inserts de forme remplaçables; nous pouvons ainsi fabriquer plusieurs pièces prototypes avec la même structure de moule. Cette technique réduit considérablement les coûts d’outillage et les délais de production, et permet même de produire en petites séries en restant rentable.
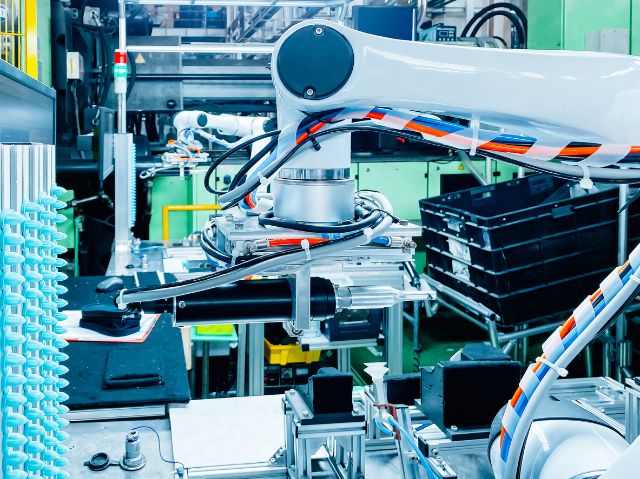
Moulage par injection automatisé
Grâce à un très haut niveau d'automatisation, Mitsubishi Chemical Group est en mesure de proposer des gains de productivité et un niveau de qualité toujours plus importants à ses clients. Cette automatisation, mise en œuvre principalement lors de l'assemblage et l'emballage sous couvert de l'assurance qualité, élimine les erreurs humaines et permet une cohérence qui conduit au « zéro défaut ». L'automatisation est également appliquée à la manutention des résines et à d'autres opérations de post-moulage.
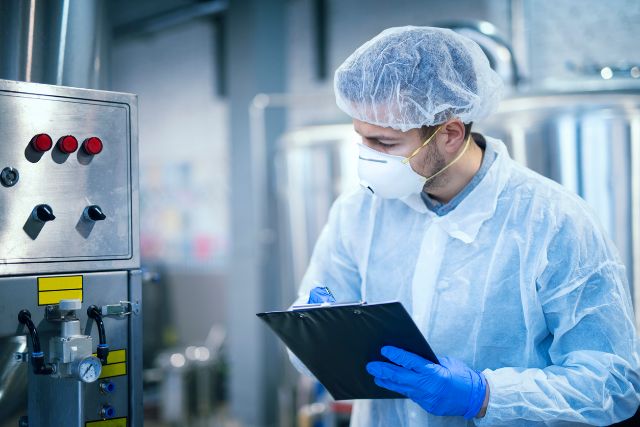
Moulage par injection en salle blanche
A la pointe de la technologie, Mitsubishi Chemical Group exploite une salle blanche de 600 m2 certifiée Classe 100 000 (ISO 8); notre entreprise respecte ainsi les normes d'hygiène les plus strictes exigées notamment pour les technologies médicales.
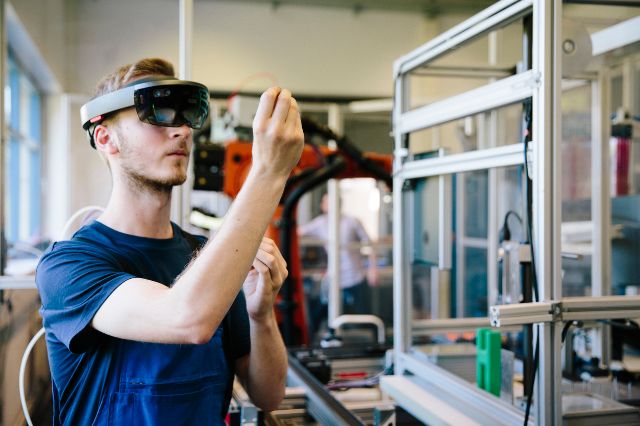
Moulage 2K et 3K
Notre processus de fabrication repose sur les dernières technologies de moulage par injection, parmi lesquelles le moulage à multicomposant et à bi-injection, le moulage par transfert et le moulage rétractable. Nous pouvons ainsi créer des moules intégraux ou à coins afin de diminuer le coût et le délai d’assemblage du produit. Nos sites de Tielt en Belgique et de Budapest en Hongrie, sont spécialisés dans le moulage 2K et 3K ( K pour composant ).
Pièces moulées par injection dans divers secteurs
Médical
À travers le monde, les fabricants d’instruments et de dispositifs en plastique pour les hôpitaux, les professionnels de santé, les laboratoires médicaux ou les établissements de recherche doivent se conformer à des règles strictes d’hygiène et de qualité. Grâce à notre expertise technique, à nos installations de fabrication dernier cri, à notre maîtrise des réglementations et à une automatisation poussée, nos produits respectent ce cahier des charges. Nous fabriquons notamment des pièces d’optique, des produits à usage unique, des systèmes de diagnostic à domicile et des produits courants de santé moulés par injection pour le secteur médical. Nous proposons également le moulage par injection en salle blanche.
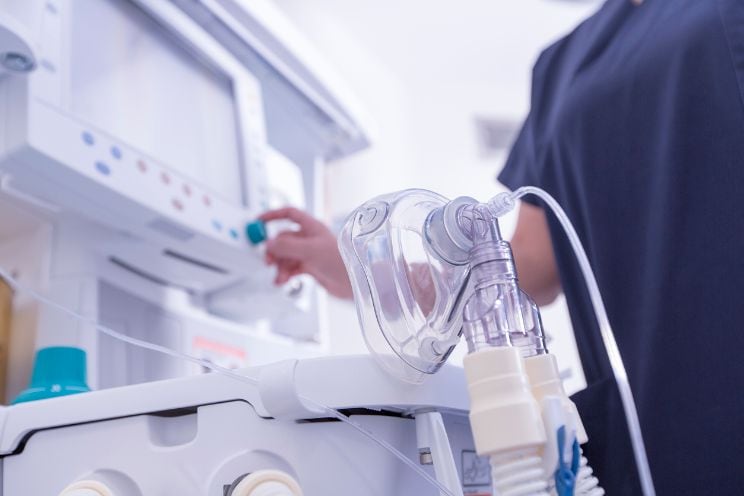
Automobile
Mitsubishi Chemical Group fournit des composants à de grands revendeurs automobiles du monde entier, conquis par sa chaîne logistique à intégration verticale complète, du développement à la production et jusqu’à l’assemblage des produits. Nos pièces moulées par injection offrent une extrême précision et une sécurité renforcée pour les applications électriques, intérieures et motrices du secteur automobile.
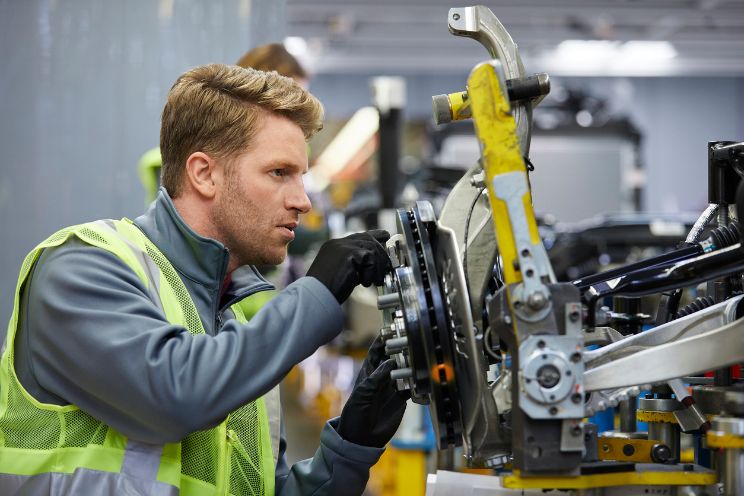
Électrique et Électronique
Notre double compétence en développement de moules et de produits est particulièrement intéressante pour le secteur de l’électronique. La demande pour des composants technologiquement plus sophistiqués et esthétiquement plus plaisants ne cesse d’augmenter. C’est pourquoi nous sommes le partenaire idéal pour concevoir et fabriquer des composants et systèmes en plastique dans ce secteur. Nous fabriquons notamment des boîtiers électriques, des cadres et des supports techniques, ainsi que des composants électromagnétiques.
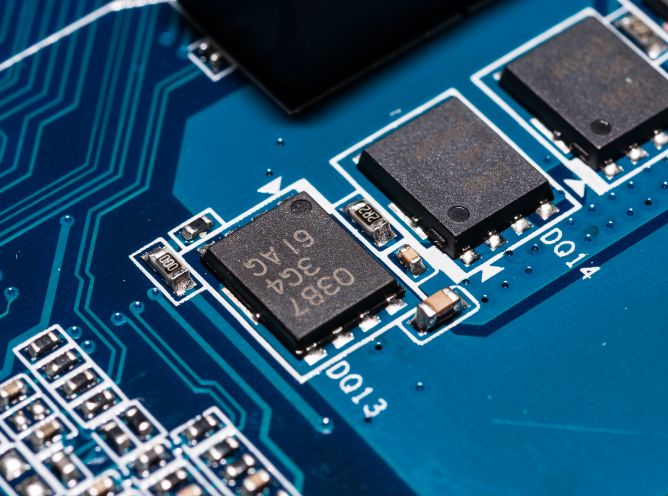
Industrie
Mitsubishi Chemical Group cumule des années d’expérience en conception de produits et ne cesse de développer sa vaste gamme de plastiques techniques et hautes performances. Appliqués dans l’industrie, nos composants thermoplastiques avancés respectent les normes de performance les plus strictes, supportent de grands efforts de charge et résistent aux fortes températures, entre autres propriétés essentielles.
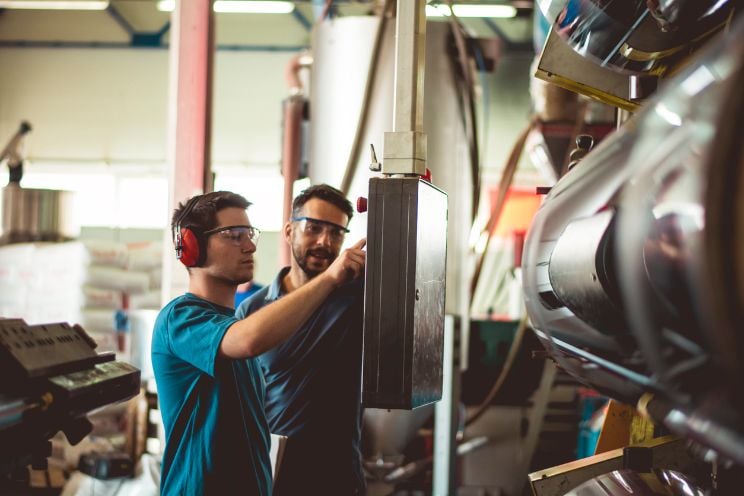
Conditionnement fonctionnel
Mitsubishi Chemical Group soutient activement les entreprises spécialisées dans les boissons, dans les soins aux personnes et dans le bien-être. Nous ne nous contentons pas de répondre aux besoins immédiats de nos clients : nous utilisons notre sens de la collaboration pour les aider à développer des solutions innovantes et personnalisées sur toute une gamme de produits, créant ainsi une valeur ajoutée sur le long terme.
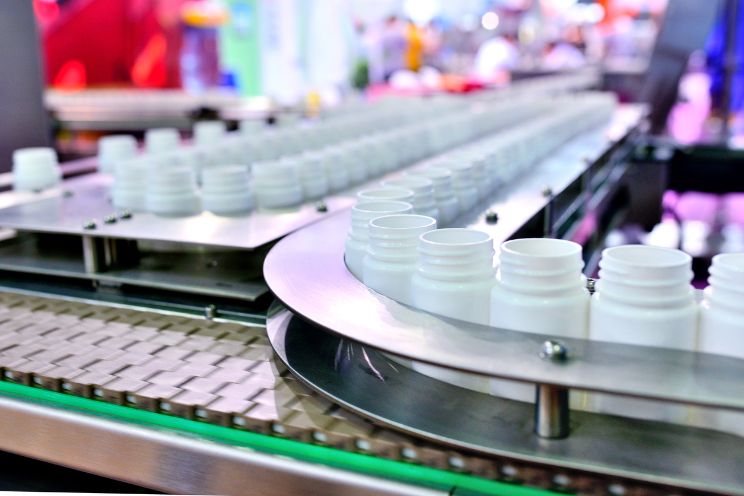
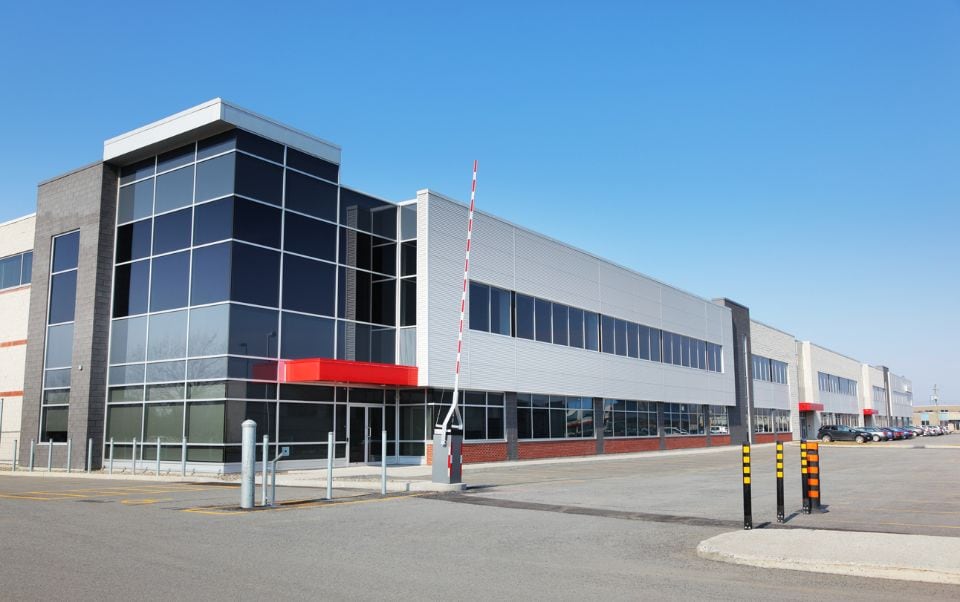
Mitsubishi Chemical Group dédie deux de ses sites à ses services de moulage par injection. Tous deux sont équipés de chaînes d’assemblage entièrement automatisées pour offrir une qualité et une homogénéité maximales. Notre équipement dernier cri comprend des machines de moulage par injection affichant une force de verrouillage comprise entre 30 et 800 tonnes métriques, dont plusieurs machines de moulage 2K et 3K. Nous proposons également des services de réparation et de modification d’outils sur site, afin de garantir la disponibilité des moules pour la production.
Tielt, Belgique (16 600 m2, environ 168 000 pi2)
Ce site de production est spécialisé dans la CAO, la fabrication de moules, la maintenance et la réparation d’outils, le prototypage, le moulage par injection, les tests, les opérations secondaires (assemblage, impression, peinture et stérilisation), la logistique et l’expédition, ainsi que dans le développement d’outils internes.
Szigetszentmiklós (Budapest), Hongrie (6 600 m2, environ 71 000 pi2)
Ce site de production propose le moulage par injection, la maintenance et la réparation d’outils, les tests, les opérations secondaires, le conditionnement, la logistique et l’expédition.
La nature même des composants en plastique moulé par injection nécessite une collaboration étroite entre le fabricant et le fournisseur. Comme partenaire global intégré verticalement, Mitsubishi Chemical Group intervient dès les premières phases de développement et de production, en proposant notamment une aide à la conception et à la sélection des matériaux. Nos services de moulage par injection ont permis de créer des composants plébiscités dans de nombreuses industries, de l’automobile au médical, en passant par les produits électroniques.
Contactez notre équipe de spécialistes en remplissant le formulaire de contact. Nous sommes prêts à relever votre prochain défi.
Contactez-nous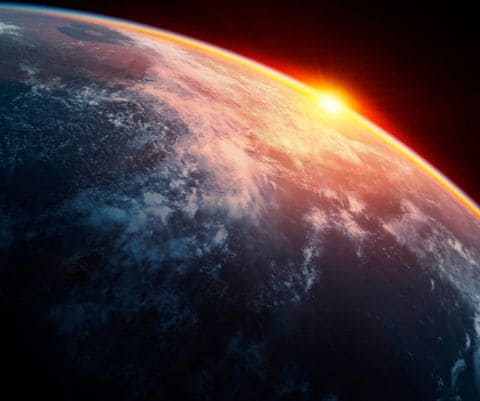